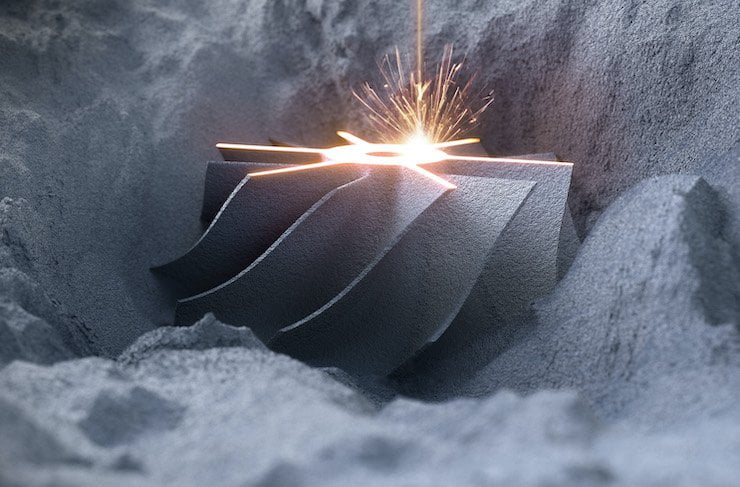
Die additive Fertigung, auch bekannt als 3D-Druck, ist eine transformative Methode zur Herstellung von Teilen und Produkten. Eine der am häufigsten verwendeten additiven Fertigungstechniken ist Selektives Laserschmelzen (SLM). SLM ist ein Pulverbettschmelzverfahren, bei dem ein Hochleistungslaser selektiv Materialpulver miteinander verschmilzt, um Teile Schicht für Schicht aufzubauen.
Mit SLM können komplexe Geometrien mit komplizierten inneren Merkmalen direkt aus 3D-CAD-Daten erstellt werden. Es minimiert auch den Materialabfall und bietet eine Designflexibilität, die bei der herkömmlichen Fertigung nicht möglich ist. SLM erfordert jedoch eine spezielle Ausrüstung, optimierte Verarbeitungsparameter und ein Verständnis der Materialeigenschaften.
Dieser umfassende Leitfaden enthält alles, was Sie über die additive Fertigung durch selektives Laserschmelzen wissen müssen. Er erklärt die Technologie, typische Materialien, Anwendungen, Vorteile und Einschränkungen, Spezifikationen, Lieferanten, Kosten, Vergleiche mit anderen 3D-Druckverfahren und vieles mehr. Lesen Sie weiter und werden Sie ein SLM-Experte!
So funktioniert der SLM-3D-Druck
Beim SLM wird ein fokussierter Laserstrahl verwendet, um Metallpulver zu schmelzen und miteinander zu verschmelzen. Die Teile werden auf der Grundlage von geschnittenen 3D-CAD-Modelldaten additiv Schicht für Schicht aufgebaut. Hier sind die wichtigsten Aspekte des SLM-Verfahrens:
SLM Additive Manufacturing Prozess Übersicht
Prozess-Schritt | Beschreibung |
---|---|
Vorbereitung des 3D-Modells | Das CAD-Modell wird in dünne 2D-Scheiben umgewandelt, um den Laserschmelzweg zu steuern. Für Überhänge können Stützstrukturen hinzugefügt werden. |
Pulverstreuung | Ein Wiederbeschichtungsmechanismus verteilt eine Schicht Metallpulver gleichmäßig auf der Bauplattform. |
Laserschmelzen | Ein fokussierter Hochleistungslaser schmilzt das Pulver selektiv auf der Grundlage der einzelnen 2D-Scheiben und verschmilzt die Partikel zu einem Feststoff. |
Untere Bauplattform | Nach der Fertigstellung einer Schicht senkt sich die Bauplattform ab, und neues Pulver wird aufgetragen. |
Wiederholen Sie die Schritte | Die Schritte Pulverauftragen, Laserschmelzen und Absenken wiederholen sich, bis das Teil fertig ist. |
Nachbearbeitung | Das Teil wird von überschüssigem Pulver befreit und muss dann möglicherweise von Halterungen befreit, gereinigt, wärmebehandelt, oberflächenbehandelt, geprüft usw. werden. |
Der schichtweise Ansatz ermöglicht die Schaffung komplexer, organischer Formen mit komplizierten inneren Hohlräumen und Tunneln, die mit herkömmlichen Methoden wie dem Gießen oder der maschinellen Bearbeitung von massiven Blöcken nicht hergestellt werden könnten.
SLM wird auch unter ähnlichen Bezeichnungen wie Selektives Lasersintern (SLS), Direktes Metall-Lasersintern (DMLS) und Pulverbettfusion (PBF) bezeichnet. Die Kernaspekte dieser pulverbasierten Verfahren sind im Wesentlichen identisch, mit kleinen Unterschieden in der Ausstattung.
SLM-Materialien
Eine breite Palette von Metallen, Legierungen und Keramiken kann mit der SLM-Technologie der additiven Fertigung bearbeitet werden. Zu den am häufigsten verwendeten gehören rostfreie Stähle, Kobalt-Chrom, Titan, Aluminium und Superlegierungen auf Nickelbasis. Die Materialoptionen werden mit der Weiterentwicklung der Technologie ständig erweitert.
Gängige SLM-Materialien und -Verwendungen
Material | Anwendungen |
---|---|
Rostfreier Stahl (316L, 17-4PH) | Kostengünstige Prototypen, funktionelle Metallteile wie Ventile, Pumpengehäuse |
Titan-Legierungen (Ti-6Al-4V) | Komponenten für die Luft- und Raumfahrt, medizinische Implantate, Automobilteile |
Kobalt-Chrom (CoCr) | Zahnkronen und -brücken, orthopädische Knie-/Hüftimplantate |
Aluminium-Legierungen (AlSi10Mg) | Leichte Drohnen, Halterungen für die Luft- und Raumfahrt, Prototypen für die Automobilindustrie |
Inconel (IN625, IN718) | Turboladerräder, Brennkammern, Motoren für die Luft- und Raumfahrt |
Werkzeugstähle (H13, Maraging-Stahl) | Spritzgussformen, Umformwerkzeuge, Werkzeugvorrichtungen |
Die beliebteste Option ist 316L-Edelstahlpulver aufgrund seiner Festigkeit, Korrosionsbeständigkeit, hochwertigen Oberflächen und niedrigeren Kosten im Vergleich zu exotischen Legierungen.
Materialien für das SLM durchlaufen eine strenge Qualitätskontrolle mit kugelförmigen Pulverpartikeln mit einem Durchmesser von durchschnittlich 15-100 Mikrometern. Feinere Pulver verbessern die Auflösung, während gröbere Pulver schneller, aber mit geringerer Genauigkeit hergestellt werden.
SLM-Anwendungen
SLM wird für die Herstellung von Prototypen, kundenspezifischen Werkzeugen und Kleinserien von komplexen, leistungsstarken Metallkomponenten mit verbesserten mechanischen Eigenschaften geschätzt. Hier sind einige der führenden Anwendungen in den wichtigsten Branchen:
SLM Additive Manufacturing Anwendungsbereiche
Industrie | Allgemeine SLM-Anwendungen |
---|---|
Luft- und Raumfahrt | Turbinenschaufeln, Kraftstoffeinspritzdüsen, Wärmetauscher, Strukturhalterungen, Satellitenantennen |
Medizinische | Personalisierte Implantate (Hüfte, Knie usw.), chirurgische Instrumente, kieferorthopädische Geräte |
Automobilindustrie | Prototypen für Hochleistungsfahrzeuge, kundenspezifische Halterungen, leichte Querlenker |
Industriell | Formen und Matrizen für die konforme Kühlung, Vorrichtungen für die Montage und Inspektion |
Öl und Gas | Kundenspezifische Ventile, Pumpen, Dichtungen, Bohrgeräte für den Hochdruckbedarf |
Verteidigung | Drohnen, Anpassung von Handfeuerwaffen, Komponenten für Fahrzeuge und Schutzwesten |
Die Fähigkeit, Baugruppen zu Einzelteilen zusammenzufassen, Designs schnell anzupassen und die Vorlaufzeiten im Vergleich zu herkömmlichen Fertigungsmethoden von Monaten auf Tage zu verkürzen, untermauert den zunehmenden Einsatz von SLM für Produktionsanwendungen in diesen Branchen.
SLM Drucker Hersteller
Viele Unternehmen stellen SLM-Geräte her, die auch als 3D-Drucker bezeichnet werden. Zu den wichtigsten Anbietern von professionellen 3D-Druckern für den industriellen Einsatz gehören:
Führende Anbieter von SLM-Maschinen
Unternehmen | Einzelheiten |
---|---|
EOS | Fundierte SLM-Technologie, umfangreiche Materialoptionen wie EOS Titanium Ti64, umfangreiche Verwendung in der Luft- und Raumfahrt |
3D-Systeme | Breite Produktpalette von Desktop- bis zu Industriedruckern |
GE-Zusatzstoff | Führender US-Anbieter, Binderjet- und Laser-Pulverbett-Optionen |
Renishaw | Hochpräzisionsoptiken für Mikroanwendungen, umfangreiche Materialtests |
SLM-Lösungen | Zuverlässige Arbeitspferde mit automatisiertem Pulverhandling |
Trumpf | Robuste deutsche Ingenieurskunst kombiniert mit Lasern |
Velo3D | Neuartiger stützenfreier Ansatz ermöglicht neue Geometrien |
Während die Anschaffungskosten für eine industrielle SLM-Maschine zwischen $150.000 und über $1 Million liegen, ist die Auswahl des richtigen Systems für den verfügbaren Platz, den Materialbedarf, die Genauigkeitsanforderungen und die Budgetüberlegungen entscheidend. Führende Hersteller bieten verschiedene Baugrößen, Multi-Laser-Konfigurationen für Geschwindigkeit, spezielle Parameter für Qualität und Wiederholbarkeit bei verschiedenen Legierungen, Software-Automatisierungsfunktionen und vieles mehr.
SLM-Materialeigenschaften
Auf SLM-Maschinen gedruckte Teile weisen aufgrund der schichtweisen Herstellung und der schnellen Erstarrung einzigartige Eigenschaften im Vergleich zu herkömmlichen Guss- und Bearbeitungsmethoden auf.
Vergleich der mechanischen Eigenschaften - SLM vs. traditionelle Fertigung
Eigentum | SLM Additive Mfg | Traditionelle Mfg |
---|---|---|
Dichte | Nahezu 100% dicht | 99% aus Guss/Knete |
Oberfläche | Schichtlinien sichtbar, Ra 6-14 μm | Glattere Oberfläche |
Zugfestigkeit | In der Regel 10-20% höher | Geringere Stärke |
Dehnung beim Bruch | Verringert um 5-15% | Höhere Dehnung |
Härte | Bis zu 2-fache Verbesserung bei einigen Legierungen | Geringere Härte |
Die hohen Abkühlungsraten des SLM-Verfahrens, die 106 °C/s überschreiten, erzeugen feinere Mikrostrukturen mit metastabilen Phasen. Dies führt zu einer maximalen Dichte bei der Pulverkonsolidierung und zu hervorragenden mechanischen Eigenschaften wie erhöhter Streck- und Zugfestigkeit. Die Dehnung ist bei SLM-Teilen in der Regel geringer, da die hohe Härte und das Vorhandensein von Eigenspannungen die Duktilität einschränken.
Durch geeignete Wärmebehandlungen und heißisostatisches Pressen (HIP) können innere Spannungen abgebaut, die physikalischen Eigenschaften weiter optimiert und die Konsistenz verbessert werden. Insgesamt kann SLM eine Dichte von mehr als 99,5% erreichen, um funktionale Metallteile zu erhalten, die im Wesentlichen mit der traditionellen Fertigung identisch sind.
SLM vs. anderer 3D-Druck
Vergleich von SLM mit anderen additiven Fertigungsverfahren
SLM | Binder Jetting | FDM | SLA | |
---|---|---|---|---|
Materialien | Metalle | Metalle, Sandformen | Kunststoffe | Harze |
Rohe Eingaben | Pulverbett | Pulverbett | Filament auf Spule | Faß mit flüssigem Harz |
Prozess | Laser schmelzt Pulver | Bindemittel Klebstoffpulver | Filament erhitzt und extrudiert | Laser härtet Harzschichten |
Wichtigste Eigenschaft | Hohe Dichte | Günstige Metallformen | Thermoplastische Kunststoffe | Glatte Oberfläche |
Stärken | Komplexe Metallteile | Kerne/Formen für den schnellen Sandguss | Funktionale Prototypen | Glatte Oberfläche |
Schwachstellen | Geringere Geschwindigkeit | Spröde, geringe Dichte | Schwache Mechanik | Begrenzte Materialoptionen |
SLM unterscheidet sich von anderen Pulverbettschmelzverfahren wie dem Elektronenstrahlschmelzen (EBM) durch seine schnelleren Scangeschwindigkeiten zur Herstellung von Teilen mit geringeren Eigenspannungen und höherer Auflösung. SLM produziert vollständig dichte, funktionale Metallteile, während der Binderjet-3D-Druck zwar schneller ist, aber mehr Nachbearbeitungsaufwand mit sich bringt. FDM- und SLA-Systeme sind SLM- und EBM-Anlagen in Bezug auf die verfügbare Materialstärke weit unterlegen.
SLM-Spezifikationen
3D-Drucker, die mit der Technologie des selektiven Laserschmelzens arbeiten, werden durch mehrere Schlüsselparameter spezifiziert, die die Materialien, die Präzision und die herstellbaren Teilegrößen bestimmen.
Wichtige Spezifikationen der SLM-Maschine
Parameter | Typischer Bereich | Beschreibung |
---|---|---|
Laserleistung | 200-500W | Höhere Leistung verbessert die Baugeschwindigkeit, verringert aber die Auflösung der feinen Merkmale |
Schichtdicke | 20-100 μm | Dünnere Schichten verbessern die Details, verlängern aber die Bauzeit |
Balkengröße | 50-80 μm | Die Größe des Fokuspunkts beeinflusst die Detailgenauigkeit und die Kontrolle des Schmelzbads |
Volumen aufbauen | 100-500 mm Würfel | Maximale Teileabmessungen, die das System produzieren kann |
Inertes Gas | Stickstoff oder Argon | Schützt vor Oxidation; Argon ermöglicht bessere Materialeigenschaften |
Scangeschwindigkeit | Bis zu 10 m/s | Schnelleres Scannen erhöht die Fertigungszeiten für Teile |
Diese Kernparameter der Maschine sowie Faktoren wie die eingebaute Heizung zum Vorwärmen des Pulvers und die Steuerung der Abkühlgeschwindigkeit ermöglichen die Abstimmung der mechanischen Eigenschaften. Die Schutzgasumgebung in der Kammer verhindert auch die Oxidation, während die Laser tausende Male pro Bauteil über das Metallpulverbett rastern.
Genauigkeit und Oberflächengüte
Die Maßgenauigkeit und die Oberflächengüte von SLM-gedruckten Teilen liegen in einem relativ großen Bereich, der von den gewählten Parametern, der Komplexität der Geometrie, der Nachbearbeitung und der Technik des Bedieners abhängt.
SLM-Genauigkeit und Oberflächengüte
Metrisch | Bereich | Beschreibung |
---|---|---|
Maßgenauigkeit | ± 0,1-0,3% mit ±50 μm typisch | Maß für den Unterschied zwischen CAD und gebautem Teil |
Mindestwanddicke | 0,3-0,5 mm | Die dünnsten Merkmale, die gedruckt werden können |
Oberflächenrauhigkeit (Ra) | 6-14 μm | Höhere Rauhigkeit als bei bearbeiteten Teilen |
Porosität | <1% Dichte | Nahezu vollständig dichte Teile bei optimalen Parametern |
Eigenspannungen | 50-500 MPa | Muss durch Wärmebehandlung entlastet werden |
Geeignete Ausrichtung, Stützstrukturen, Vorwärmung der Bauplatte, optimierte Scanstrategien und Nachbearbeitungsschritte wie CNC-Bearbeitung und Polieren können die Oberflächengüte verbessern. Die Maßgenauigkeit hängt auch stark von der richtigen Kalibrierung der Geräte ab.
Nachbearbeitungsanforderungen
Nachdem das SLM-System die Herstellung eines Bauteils abgeschlossen hat, sind in der Regel weitere Nachbearbeitungsschritte erforderlich, bevor die Teile in Betrieb genommen werden können. Diese Schritte können umfassen:
- Entnahme von Teilen aus dem Pulverkuchen
- Beseitigung von Stützstrukturen
- Spannungsabbauende Wärmebehandlungen
- Heißisostatisches Pressen (HIP)
- Oberflächenschleifen, Sandstrahlen, Perlstrahlen, Polieren
- Zerstörungsfreie Prüfung
Die Nachbearbeitung zielt darauf ab, die Oberflächenrauheit zu verringern, Eigenspannungen abzubauen, Mikroporositäten zu schließen und die Maßgenauigkeit und Ästhetik zu verbessern.
Spezifische Verfahren werden durch den Materialtyp, die Produktionsabsicht (Prototyp vs. Funktionsteil), die Leistungsanforderungen und die erforderlichen kritischen Toleranzen bestimmt.
Kostenanalyse
Die Ermittlung der Investitionsrentabilität für die Anschaffung und den Betrieb eigener SLM-Fertigungskapazitäten für die additive Fertigung hängt von vielen Variablen ab.
SLM-Kostenüberlegungen
Kostenfaktor | Beschreibung |
---|---|
Maschinenausstattung | $150k - $1M+ je nach Bauvolumen, Multi-Laser-Optionen, zusätzliche Funktionen wie automatisierte Pulververarbeitung und -rückgewinnung |
Anforderungen an die Einrichtung | Inertgas-Handling-System, Entlüftungsfilter, explosionsgeschützte Konstruktion, Temperatur-/Feuchtigkeitsregelung |
Installation und Schulung | In der Regel 2 Wochen für die Einrichtung der Maschine, Kalibrierung und Softwareeinweisung |
Arbeit | Maschinenbedienung weniger intensiv als bei der CNC-Bearbeitung, aber immer noch Bediener erforderlich; CAM-Experte empfohlen |
Materialien | $100-500 pro kg Pulver; Wiederverwertbarkeit variiert; optimierte Parameter pro Legierung |
Nachbearbeitung | Arbeit, Werkzeuge, ausgelagerte Wärmebehandlung, Oberflächenbehandlung |
Software | $10k-$25k-Bereich für Vorverarbeitung, Simulation, Fernüberwachungsanwendungen |
F&E Iterationen | Testen von Parametern für neue Teile mit dem für die Qualifizierung wichtigen Agile-Prozess |
Auftragsvolumen | Kleine/mittlere Chargen sind ideal im Vergleich zum Gießen/Gießen großer Mengen |
Wägen Sie die Gesamtbetriebskosten gegen Werttreiber wie:
- Designfreiheit für Gewichtsreduzierung, kundenspezifische Anpassung, Teilekonsolidierung
- Verkürzung der Vorlaufzeit von Monaten auf Tage/Stunden
- Vereinfachung der Lieferkette durch Fertigung auf Abruf
- Leistungsverbesserungen wie erhöhte Festigkeit und Härte
- Nachhaltige Produktion mit minimalem Abfall gegenüber subtraktiven Methoden
- Verlängerte Lebensdauer hochwertiger Teile wie in der Luft- und Raumfahrt und in der Medizintechnik
Die Quantifizierung von Produktivitäts- und Innovationsgewinnen ist entscheidend. Mit etwas Erfahrung können die Gesamtkosten pro mit SLM hergestelltem Teil mit denen der CNC-Bearbeitung bei kleineren Produktionsserien mithalten.
Industrie-Normen
Da es sich um eine relativ neue Technologie handelt, werden derzeit noch Anstrengungen unternommen, um branchenweite Spezifikationen, Codes und Normen für die additive SLM-Fertigung einzuführen.
SLM-Standardisierungs-Landschaft
Normungsgremium | Umfang | Spezifische Normen |
---|---|---|
ASTM F42 | Additive Fertigungsverfahren | Prüfmethoden, Terminologie, Prozessparameter, Umgebungen, Materialien, Gesundheit und Sicherheit |
Amerika macht | Normen für die additive Fertigung | Roadmap für AM-Standards für Materialien, Prozesse und Datenformate in den Bereichen Verteidigung, Luft- und Raumfahrt sowie Schifffahrt |
ISO TC 261 | AM-Normen | 17 veröffentlicht, 46 in der Entwicklung: Terminologie, Prozesse, Arbeitsabläufe, QA, Umgebungen, Sicherheit |
ASME | Bewertung der Konformität | Programm für die Qualifizierung von AM-Teilen; zertifiziert AM-Prozesse für die Einhaltung von Vorschriften |
Die Zertifizierung nach diesen Normen gewährleistet Wiederholbarkeit und Zuverlässigkeit bei der Auftragsvergabe für AM-Teile in der gesamten Lieferkette. Die Einhaltung der Normen ermöglicht auch eine breitere Akzeptanz in regulierten Sektoren wie der Luft- und Raumfahrt und der Medizintechnik.
Fallstudien
Zahlreiche Unternehmen nutzen die Designfreiheit und die kurzen Vorlaufzeiten von SLM, um leichtere und stabilere Komponenten zu fertigen - von Raketen für die Luft- und Raumfahrt bis hin zu Formel-1-Autos.
SLM Additive Manufacturing Anwendungsbeispiele
Industrie | Unternehmen | Teil | Vorteile |
---|---|---|---|
Luft- und Raumfahrt | SpaceX | SuperDraco-Motorkammer | 75% Kostenreduzierung, geliefert in Tagen statt Monaten |
Luftfahrt | Boeing | 777X Klammern | Konsolidierte Baugruppen, 60% mit geringerem Gewicht |
Automobilindustrie | Bugatti | Bremssattel | Reduzierte Masse durch 40%, optimierter Flüssigkeitsstrom |
Medizinische | Zimmer Biomet | Wirbelsäulen-Implantate | Maßgeschneiderte Formen für die Anatomie, osteokonduktive Strukturen zur Unterstützung des Knochenwachstums |
Diese Anwendungen zeigen, dass SLM-Teile die herkömmlichen Fertigungsbeschränkungen übertreffen. Je mehr Unternehmen AM-Technologien einsetzen, desto größer werden die Innovationsmöglichkeiten.
SLM Additive Fertigung - FAQs
Häufig gestellte Fragen zu SLM
Frage | Antwort |
---|---|
Wie funktioniert der SLM-Druck? | SLM baut Teile Schicht für Schicht aus Metallpulver auf, wobei ein Laserstrahl das Material auf der Grundlage von CAD-Daten selektiv schmilzt und verschmilzt. |
Welche Materialien sind verfügbar? | Am beliebtesten sind Edelstahl 316L und 17-4, Titanlegierung Ti64, Kobalt-Chrom, Aluminium AlSi10Mg, Werkzeugstahl, Nickelsuperlegierungen |
Was sind die wichtigsten Vorteile gegenüber der maschinellen Bearbeitung? | Konstruktionsfreiheit für Leichtbaustrukturen, kundenspezifische Anpassung, Teilekonsolidierung; kürzere Lieferzeiten; weniger Abfall; verbesserte mechanische Eigenschaften |
Was bestimmt die Oberflächenbeschaffenheit? | Schichtauflösung, Bauparameter, Ausrichtung, Nachbearbeitungsschritte wie Perlstrahlen |
Welche Genauigkeit kann SLM erreichen? | Eine Maßgenauigkeit von ±0,1-0,3% ist für die meisten Anwendungen typisch, wobei die Mindestwandstärken bei 0,3-0,5 mm liegen. |
Braucht der SLM-Prozess Unterstützung? | Bei erheblichen Überhängen sind je nach Ausrichtung und Geometrie Stützkonstruktionen erforderlich |
Welche Nachbearbeitung ist erforderlich? | Die Schritte können das Entfernen von Stützen, Spannungsentlastung, heißisostatisches Pressen, Oberflächenbearbeitung wie Schleifen oder Polieren umfassen. |
Für welche Anwendungen ist SLM geeignet? | Schnelle Prototypen, kundenspezifische Werkzeuge, wie Vorrichtungen, und direkte Metallteile für den Endgebrauch in der Luft- und Raumfahrt, Medizin-, Dental- und Automobilindustrie |
Wie sieht es mit der Qualität im Vergleich zur traditionellen Fertigung aus? | Mit optimierten Parametern erreichen oder übertreffen >99% dichte SLM-Teile mechanische Eigenschaften und Lebensdauer |
Wie sollte das Design für SLM angepasst werden? | Konforme Kanäle, Gitter, Topologieoptimierung - all das eignet sich hervorragend für AM. Leitlinien helfen bei der Anpassung von Teilen. |
Diese FAQ fasst die Antworten auf die wichtigsten Fragen zur additiven Fertigung durch selektives Laserschmelzen zusammen. SLM ermöglicht neue Leistungsmaßstäbe dank völliger Designfreiheit.
Die Zukunft von SLM
Die Verbreitung von SLM nimmt weiter zu, da immer mehr Branchen die Grenzen der additiven Fertigung ausloten. Fortschritte bei Ausrüstung, Software, Materialien und Qualitätsprozessen werden die Anwendungsmöglichkeiten erweitern.
Erwarten Sie eine breitere Verfügbarkeit von spezialisierten Maschinen und Bearbeitungsparametern aus mehreren Legierungen von führenden Druckerherstellern. Hybride Systeme, die komplementäre Prozesse wie Fräsen, Bohren und Inspektion umfassen, werden ebenfalls für die integrierte Fertigung entwickelt. Automatisierte Pulverentfernung und -rückgewinnung werden die Kosten senken.
Die Überwachung in Echtzeit ermöglicht noch strengere Prozesskontrollen und eine geschlossene Qualitätssicherung. Algorithmen des maschinellen Lernens können die Gebäudeleistung optimieren. In dem Maße, in dem sich die Standards für bewährte Verfahren verfestigen, werden die Nutzer auch mehr Vorhersehbarkeit gewinnen.