High purity metal powders refer to metallic powders with extremely low levels of impurities, often 99.9% pure or higher. They are utilized across a wide range of advanced applications where contamination-free materials are critical for performance and reliability.
Overview of High Purity Metal Powders
High purity metal powders possess unique properties that make them indispensable for sophisticated technologies. This guide covers key aspects of these powders:
Table 1: Overview of high purity metal powders
Parameter | Einzelheiten |
---|---|
Common metals used | Nickel, cobalt, copper, iron, titanium, tungsten, molybdenum, tantalum, rhenium |
Reinheitsgrade | 99.9% to 99.999%+ |
Partikelgrößen | Sub-micron to 100 microns |
Produktionsmethoden | Vacuum induction melting, gas atomization, chemical reduction |
Key applications | Electronics, optics, medical devices, aerospace components, additive manufacturing |
Vorteile | Enhanced performance, reliability, precision |
Herausforderungen | High production costs, contamination risks |
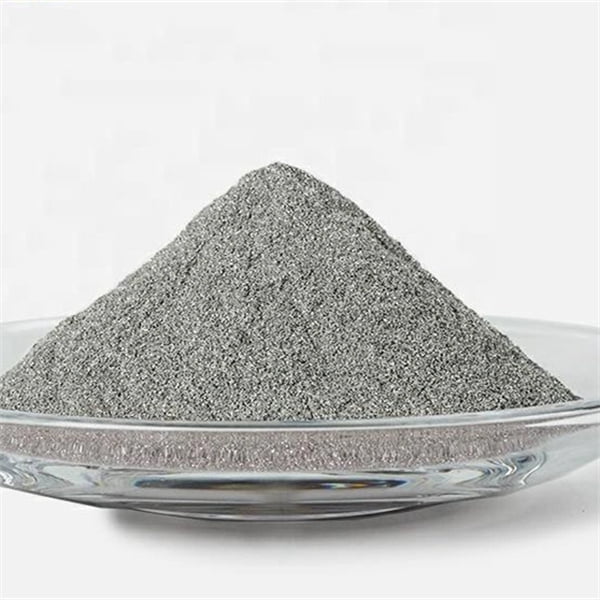
Arten von Hochreine Metallpulver
Metall/Legierung | Produktionsverfahren | Reinheit | Anwendungen | Wesentliche Merkmale |
---|---|---|---|---|
Aluminum & Aluminum Alloys | Atomization, Chemical Vapor Deposition (CVD) | Up to 99.99% (4N) | * Additive Manufacturing (3D Printing) * Aerospace components * Heat exchangers * High-performance filters | Spherical or near-spherical particles for good flowability and packing density. High thermal and electrical conductivity. |
Tungsten & Tungsten Alloys | Hydrogen Reduction, Ammonium Paratungstate (APT) | Up to 99.995% (4N5) | * High-temperature furnace components * X-ray tubes and targets * Electrodes for inert gas welding * Armor-piercing projectiles | High melting point, excellent strength at high temperatures, good resistance to corrosion and erosion. |
Titan und Titan-Legierungen | Disintegration, Hydride-Dehydride (HDH) process | Up to 99.9% (3N) | * Biomedical implants * Aircraft components * Sporting goods (golf clubs, bicycles) * Chemical processing equipment | High strength-to-weight ratio, excellent biocompatibility, good corrosion resistance. |
Precious Metals (Gold, Platinum, Palladium) | Electrolysis, Chemical Reduction | Up to 99.999% (5N) | * Electronics (electrical contacts, connectors) * Catalytic converters * Fuel cells * Jewelry | High electrical conductivity, good resistance to corrosion and oxidation. |
Rare Earth Metals (Yttrium, Neodymium, Dysprosium) | Electrolysis, Metal-Organic Framework (MOF) methods | Up to 99.95% (4N5) | * Permanent magnets * Lasers * Solid-state lighting * Catalysts | Unique magnetic properties, high catalytic activity for various chemical reactions. |
High Purity Metal Powder Production Methods
Methode | Beschreibung | Vorteile | Benachteiligungen | Anwendungen |
---|---|---|---|---|
Zerstäubung | Molten metal is disintegrated into fine droplets using a high-velocity gas or water stream. | * High production rate * Suitable for a wide range of metals and alloys * Produces spherical or near-spherical powders with good flowability * Can achieve high purity levels | * High energy consumption * Requires sophisticated equipment * May introduce internal voids or oxides in the powder particles | * Additive Manufacturing (3D Printing) * Metal Injection Molding (MIM) * Production of high-performance filters and heat exchangers |
Elektrolyse | An electric current is used to extract metal ions from a metal salt solution and deposit them as a metal powder on a cathode. | * Produces very high purity powders (up to 5N) * Well-suited for reactive metals like copper and precious metals * Offers good control over particle size and morphology | * Relatively slow process compared to atomization * Limited to metals that can be readily dissolved in electrolytes * Can be energy-intensive | * Electronics (electrical contacts, connectors) * Catalytic converters * Fuel cells * High-conductivity copper for electrical applications |
Hydride-Dehydride (HDH) Process (for Titanium) | Titanium is reacted with hydrogen to form a titanium hydride intermediate, which is then crushed and dehydrided to produce titanium powder. | * Well-suited for producing high-purity titanium powders * Offers good control over powder morphology * Can be used to produce spherical titanium powders | * Complex process with multiple steps * Requires careful control of process parameters to avoid contamination * Limited production capacity compared to atomization | * Biomedical implants * Aircraft components * Sporting goods (golf clubs, bicycles) |
Chemische Gasphasenabscheidung (CVD) | Metal atoms or molecules are deposited from a gaseous phase onto a substrate to form a metal powder. | * Can produce very high purity powders (up to 5N) * Suitable for producing powders with unique compositions or nanostructures * Offers good control over powder morphology | * Slow and expensive process with low production rates * Limited to producing fine powders * Requires specialized equipment and expertise | * Additive Manufacturing of high-performance components * Production of advanced catalysts and filters |
Solid-State-Reduktion | Metal oxides are reduced using a reducing agent (e.g., hydrogen) to produce metal powder. | * Relatively simple and inexpensive process * Suitable for a wide range of metals and alloys | * Limited control over powder purity and morphology * May produce powders with irregular shapes and broad size distributions * Not ideal for very high purity applications | * Friction materials (brake pads) * Production of ferrous components for low-cost applications |
Applications and Benefits of High Purity Metal Powders
The unique properties of contamination-free metal powders serve critical needs in various spheres:
Table 4: Key application areas for high purity metal powders
Industrie | Anwendungen | Gewünschte Eigenschaften | Vorteile |
---|---|---|---|
Elektronik | Conductors, capacitors, circuits, microchips | High conductivity, low resistance | Miniaturization, fast processing speeds |
Luft- und Raumfahrt | Jet engine and airframe components | Strength under extreme conditions | Lighter and efficient structures |
Medizinische Geräte | Implants, imaging agents, radiation shielding | Biokompatibilität, Korrosionsbeständigkeit | Improved body acceptance, precise visualization |
Optik | Telescopes, microscopes, lasers | Extreme surface precision | Sharper resolution and focus |
Additive Fertigung | 3D printed critical components | Reliable material properties | Design freedom, rapid prototyping |
Stringent quality demands of cutting-edge technologies fuel the need for contamination-free high purity metal powders.
High Purity Metal Powder Suppliers
High purity powder metallurgy is an extremely specialized field with only a few major global producers having the expertise and infrastructure for quality powder manufacturing:
Table 5: Leading suppliers of high purity metal powders
Unternehmen | Bediente Märkte | Metals Offered | Partikelgrößen | Reinheitsgrade |
---|---|---|---|---|
BASF | Aerospace, medical, optics | Nickel, cobalt | 15μm to 150μm | Up to 99.995% |
Sandvik | Additive manufacturing, automotive | Nickel, cobalt, titanium | 10μm to 45μm | Bis zu 99,9% |
AMETEK | Elektronik, Verteidigung | Tungsten, molybdenum | 0.5μm to 10μm | Bis zu 99,999% |
Jien Nickel | Alloys, batteries | Nickel, copper | Up to 100μm | Bis zu 99,99% |
Atlantic Ausrüstungsingenieure | R&D, universities | Nickel, iron, copper | Up to 325 mesh | Up to 99.9%+ |
Leading metal powder producers offer tailored ultra-high purity solutions to niche industries.
Carefully vet suppliers based on application needs and rigor of quality assurance protocols. Materials must adhere to strict cleanliness standards.
Choosing Right High Purity Metal Powder
Selecting optimal high purity powders entails matching application requirements to material properties:
Table 6: High purity metal powder selection guidelines
Parameter | Einzelheiten |
---|---|
Desired material properties | Strength, corrosion resistance, conductivity, magnetism |
Betriebsbedingungen | Temperatures, pressures, stresses |
Target component design | Geometries, precision needs |
Production method specifications | Particle sizes, size distribution, flow characteristics |
Purity levels mandated | Based on contamination risks and impact |
Supplier qualifications | Quality certifications, testing capabilities |
Budgetzwänge | Balance performance needs with costs |
- Collaborate with powder producers early when developing new applications.
- Validate claims of purity levels and properties through rigorous testing.
- Leverage suppliers’ technical expertise in tailoring materials.
Careful consideration of multiple factors helps select ideal high purity powders for specific uses.
Installing and Handling Hochreine Metallpulver
Schritt | Beschreibung | Bedeutung | Überlegungen |
---|---|---|---|
Facility Preparation | Establish a dedicated workspace for handling high purity metal powders. | Minimizes contamination risk and ensures proper powder flow. | * Designate a cleanroom or controlled environment with filtered air and low humidity. * Install dedicated equipment for powder handling (e.g., gloveboxes, inert gas purging systems). * Implement procedures for cleaning and maintaining the workspace to prevent contamination. |
Powder Transfer | Employ appropriate techniques to transfer powders from their original containers to processing equipment. | Maintains powder integrity and minimizes waste. | * Minimize exposure to air and moisture during transfer. * Use sealed containers or inert gas transfer systems. * Utilize dedicated transfer tools (e.g., scoops, funnels) made from compatible materials (e.g., stainless steel). |
Lagerung | Store powders in a controlled environment to maintain their purity and flowability. | Ensures consistent powder performance and minimizes degradation. | * Store powders in their original sealed containers or in designated, air-tight containers. * Maintain a dry, low-humidity environment (ideally with inert gas atmosphere for highly reactive powders). * Label containers clearly with identification information and handling precautions. * Rotate stock to ensure FIFO (First-In-First-Out) principle for powder usage. |
Persönliche Schutzausrüstung (PSA) | Wear appropriate PPE to protect personnel from potential health hazards. | Ensures worker safety when handling potentially hazardous materials. | * Wear gloves, safety glasses, and respirators appropriate for the specific powder being handled. * Lab coats or other protective clothing may be necessary depending on the application. * Follow proper procedures for donning and doffing PPE to minimize contamination risk. |
Waste Management | Establish procedures for handling and disposing of waste powder to minimize environmental impact. | Promotes a safe and responsible work environment. | * Segregate waste powder from unused powder to prevent contamination. * Utilize designated containers for waste powder disposal. * Dispose of waste powder according to local and federal regulations * Consider recycling options where feasible. |
Comparing Metal Powders for Additive Manufacturing
Additive manufacturing holds enormous promise for producing high performance components, leveraging ultra-high purity metal powders:
Table 8: Comparing metal powders for additive manufacturing
Parameter | Nickel-Pulver | Titan-Pulver | Aluminium-Pulver |
---|---|---|---|
Kosten | Höher | Höchste | Niedrigste |
Mechanische Eigenschaften | Ductile, moderate strength | Extremely strong and light | Light, low strength |
Thermische Eigenschaften | Resistant to ~1000°C | Resistant to ~600°C | Resistant to ~400°C |
Korrosionsbeständigkeit | Hoch | Ausgezeichnet | Mäßig |
Anwendungen | Komponenten für die Luft- und Raumfahrt, Werkzeugbau | Aerospace structures, medical implants | Automotive parts, consumer products |
AM Process Compatibility | Compatible with all major processes | Limited to DED and PBF only | Compatible with all major processes |
- Nickel offers best balance of performance and capabilities.
- Titanium excels where strength-to-weight ratio is critical.
- Aluminum suits cost-sensitive applications despite limitations.
Material choice depends on balancing critical component requirements with production economics.
High Purity Metal Powder Market Outlook
Global demand for ultra-high purity powders is projected to grow substantially driven by rising adoption in sophisticated technologies:
Table 9: Growth drivers for high purity metal powder market
Faktor | Beitrag | Branchen |
---|---|---|
Miniaturization of electronics | Higher conductivity powders needed | Consumer gadgets, aerospace systems |
Expanding additive manufacturing | Enables complex component fabrication | Luft- und Raumfahrt, Medizintechnik, Automobilindustrie |
Rising alloy grades | Require raw metals with <10 ppm impurities | Superalloys for extreme environments |
Investment in R&D | Enables evaluating more materials and applications | Academia, government labs |
- Market predicted to reach around $500 million by 2030.
- High purity cobalt, titanium, nickel leading growth.
- USA, Europe, China leading production and consumption.
Consistent demand from exacting industries sustains the market for contamination-free ultra-high purity metal powders.
Challenges With Hochreine Metallpulver
While possessing enormous potential, some inherent challenges exist with handling these materials:
Table 10: Challenges associated with high purity metal powders
Ausgabe | Beschreibung | Minderungsstrategien |
---|---|---|
Kosten | Require substantial investments in infrastructure and processing | Develop economies of scale as adoption increases |
Verunreinigung | Risk degradation of desired properties | Follow stringent handling protocols |
Safety hazards | Flammability, explosivity, toxicity concerns | Precautions for containment, PPE |
Waste handling | Recover used powder without pollution | Methods for purification and reuse |
Lack of Standards | Varying methods to demonstrate purity levels | Harmonize testing protocols globally |
Technical and economic barriers exist, but are being actively addressed allowing greater access to these specialized powders.
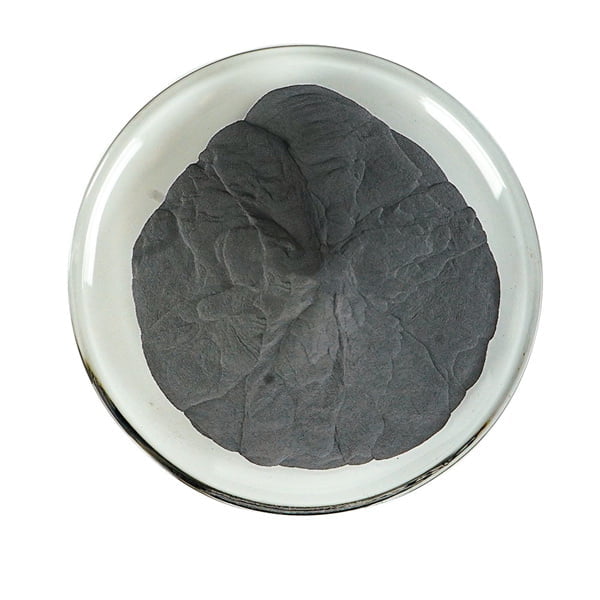
FAQ
Q: What level of purity is considered “high” for metal powders?
A: Generally 99.9% or higher purity signifies contamination-free high purity metal powders. Some ultra-high purity grades go up to 99.999% (5N) or more.
Q: Does high purity translate to higher powder costs?
A: Yes, costs are substantially higher than conventional metal powders due to specialized production methods required. Prices increase exponentially with higher purity levels.
Q: How to assess the actual purity of purchased metal powders?
A: Rigorously test incoming raw material lots using methods like ICP-MS chemical analysis to verify claimed purity certifications from suppliers.
Q: Does particle shape/morphology matter for high purity powders?
A: Spheroidal powders are typically preferred for ease of flow and density. Irregular shapes make handling and processing more difficult.
Q: How are high purity metal powder manufacturers improving capabilities?
A: Investments in technologies like chemically-driven powder synthesis allow lower contamination levels. Automation increases consistency.