Überblick über Elektronenstrahl-Schmelzanlage
Das Elektronenstrahlschmelzen (EBM) ist eine additive Fertigungstechnologie, bei der Metallpulver mit Hilfe eines Hochleistungselektronenstrahls unter Vakuumbedingungen Schicht für Schicht zu vollständig dichten Teilen verschmolzen werden. EBM-Maschinen bieten unübertroffene Baugeschwindigkeiten und mechanische Eigenschaften, die mit anderen Metall-3D-Druckverfahren nicht erreicht werden können.
Zu den wichtigsten Merkmalen der EBM-Technologie gehören:
Tabelle 1: Überblick über die Elektronenstrahlschmelztechnologie
Attribut | Beschreibung |
---|---|
Wärmequelle | Hochintensiver Elektronenstrahl |
Umwelt | Hochvakuum |
Rohstoff | Metall-Pulverbett |
Strahlsteuerung | Elektromagnetische Linsen und Spulen |
Bau-Modus | Schichtweises Schmelzen von Metallpulver |
Anwendungen | Luft- und Raumfahrt, Medizintechnik, Automobilindustrie, Werkzeugbau |
Durch präzise Strahlfokussierung und schnelles Scannen verschmilzt EBM leitfähige Materialien wie Titan, Nickellegierungen, Werkzeugstähle und Refraktärmetalle zu vollständig dichten Komponenten mit hervorragenden Eigenschaften, die nur von Knetprodukten übertroffen werden.
Die kontrollierte Vakuumumgebung verhindert Verunreinigungen, während die intelligente Energiezufuhr und die hohen Vorwärmtemperaturen Eigenspannungen, die zu Verzug oder Rissen führen können, minimieren.
Das Verständnis dieser Kernprinzipien verdeutlicht, warum EBM außergewöhnliche mechanische Leistungen liefert, die für die anspruchsvollsten Industrieanwendungen maßgeschneidert sind.
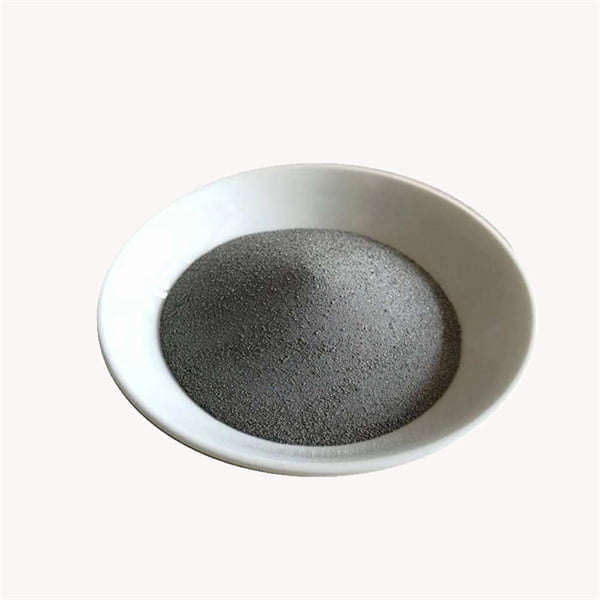
Arten von Elektronenstrahlschmelzsystemen
Merkmal | Beschreibung | Auswirkungen auf die Systemnutzung |
---|---|---|
Konfiguration der Elektronenkanone | Elektronenstrahlschmelzsysteme verwenden eine Elektronenkanone zur Erzeugung eines hochenergetischen Strahls, der selektiv Metallpulver schmilzt. Es gibt zwei Hauptkonfigurationen für Elektronenkanonen: * Sidewinder: Die Elektronenstrahlquelle ist horizontal neben der Baukammer angeordnet. Diese Konstruktion ermöglicht ein größeres Baukammervolumen, kann aber den Zugang für die Nachbearbeitung einschränken. * Top Gun: Die Elektronenstrahlquelle befindet sich direkt über der Baukammer. Diese Konfiguration bietet einen einfacheren Zugang für die Teileentnahme und Überwachung, kann aber den maximalen Bauraum einschränken. |
Die Wahl der Pistolenkonfiguration hängt von der Priorität zwischen Bauvolumen und Zugänglichkeit ab. Sidewinders sind ideal für die Produktion größerer Teile mit hohem Durchsatz, während Top Guns besser für Forschungs- und Entwicklungsanwendungen geeignet sind, bei denen eine häufige Überwachung und Manipulation der Teile erforderlich ist. |
Modus Strahlschmelzen | EBM-Systeme können in zwei primären Strahlschmelzmodi arbeiten: * Rasterscan: Der Elektronenstrahl tastet das Pulverbett in einem vorgegebenen Muster schnell ab und schmilzt dabei Schicht für Schicht bestimmte Bereiche auf. Diese Methode ist für einfache Geometrien effizient, kann aber auf gekrümmten Oberflächen zu treppenförmigen Artefakten führen. * Vektor-Scan: Der Elektronenstrahl folgt einem definierten Vektorpfad, um das Pulver zu schmelzen. Diese Methode bietet eine bessere Kontrolle über die Geometrie des Schmelzbads und die Oberflächengüte, insbesondere bei komplizierten Merkmalen. Allerdings kann die Vektorabtastung bei einfachen Geometrien langsamer sein als die Rasterabtastung. |
Die Wahl zwischen Raster- und Vektorscanmodi hängt von dem gewünschten Gleichgewicht zwischen Geschwindigkeit, Auflösung und Oberflächenqualität ab. Das Rasterscannen wird für die Massenproduktion von Teilen mit einfachen Geometrien bevorzugt, während das Vektorscannen besser für komplexe Teile geeignet ist, die eine hohe Genauigkeit und Oberflächengüte erfordern. |
Vakuum System Design | Das Elektronenstrahlschmelzen erfordert eine Hochvakuumumgebung (in der Regel unter 10^-4mbar), um die Oxidation des geschmolzenen Metalls zu verhindern und die Strahlstabilität zu gewährleisten. Es gibt zwei gängige Vakuumsystemkonstruktionen: * Diffusionspumpe: Bei dieser traditionellen Bauweise werden Diffusionspumpen eingesetzt, um das erforderliche Vakuumniveau zu erreichen. Diffusionspumpen sind zuverlässig und bewährt, erfordern jedoch eine routinemäßige Wartung und können relativ langsam sein, um ein optimales Vakuumniveau zu erreichen. * Kryopumpen: Bei dieser neueren Technologie werden Kryopumpen eingesetzt, um Gasmoleküle durch extreme Kühlung einzufangen. Kryopumpen bieten im Vergleich zu Diffusionspumpen schnellere Abpumpzeiten und geringeren Wartungsbedarf. Sie haben jedoch höhere Anfangsinvestitionskosten und erfordern möglicherweise zusätzliche Rohrleitungen für die Versorgung mit Flüssigstickstoff. |
Die Wahl des Vakuumsystems hängt von Faktoren wie Budget, Wartungsanforderungen und gewünschten Zykluszeiten ab. Diffusionspumpen sind eine kosteneffiziente Wahl für etablierte Produktionsumgebungen, während Kryopumpen Vorteile für Anwendungen mit hohem Durchsatz oder Forschungsumgebungen bieten, bei denen schnelle Durchlaufzeiten im Vordergrund stehen. |
Pulverabgabe-System | Die gleichmäßige Verteilung des Metallpulvers auf der Bauplattform ist entscheidend für den Erfolg von EBM-Bauten. Es werden zwei primäre Pulverzufuhrsysteme eingesetzt: * Beschichtung der Klinge: Eine Klinge oder ein Rechen verteilt nach jedem Schmelzzyklus eine dünne Pulverschicht auf der Bauplattform. Die Schaufelbeschichtung ist eine einfache und zuverlässige Methode, kann aber aufgrund von Schwankungen des Schaufeldrucks und -winkels zu Unregelmäßigkeiten in der Pulverdichte führen. * Rückspulung: Ein Hochdruck-Gasstrom unterbricht das Pulverbett, wodurch die Pulverpartikel zurückprallen und eine neue Schicht auftragen. Das Recoil-Verfahren bietet eine gleichmäßigere Pulververteilung als die Schaufelbeschichtung, erfordert aber eine sorgfältige Optimierung des Gasdrucks, um eine Störung der bereits geschmolzenen Schichten zu vermeiden. |
Die Wahl des Pulverzufuhrsystems beeinflusst die Schichtqualität und die Wiederholbarkeit. Die Schaufelbeschichtung eignet sich für die Produktion von Kleinserien oder Anwendungen, bei denen die Pulverdichte weniger kritisch ist. Die Rückspulenbeschichtung wird für hochpräzise Teile bevorzugt, die eine gleichmäßige Pulververteilung erfordern. |
Grundlagen des Elektronenstrahlschmelzverfahrens
Bühne | Beschreibung | Vorteile | Überlegungen |
---|---|---|---|
Vorbereitung des Pulvers | Die im EBM verwendeten Metallpulver werden sorgfältig hergestellt, um eine optimale Fließfähigkeit, Partikelgrößenverteilung und chemische Reinheit zu gewährleisten. Die Partikelgröße spielt eine entscheidende Rolle, da zu feine Pulver die Ausbreitung von Schichten behindern können, während zu grobe Pulver zu Balling und schlechtem Schmelzen führen können. Eine strenge Kontrolle von Sauerstoff, Stickstoff und anderen Elementen ist unerlässlich, um die Porosität zu minimieren und die gewünschten mechanischen Eigenschaften zu erzielen. | * Konsistente Materialeigenschaften während des gesamten Bauprozesses * Geringeres Risiko von Mängeln wie Porosität und Rissbildung |
* Hohe Vorlaufkosten für hochwertige Metallpulver * Notwendigkeit einer speziellen Handhabung und Lagerung aufgrund der möglichen Reaktivität |
Vakuumkammer | Beim Elektronenstrahlschmelzen ist ein Hochvakuum erforderlich (in der Regel zwischen 10-⁴ und 10-⁹ Pa), um Oxidation und Verunreinigung des geschmolzenen Metalls zu verhindern. Dies wird durch leistungsstarke Vakuumpumpen erreicht, die Luftmoleküle aus der Kammer absaugen. Die Abwesenheit von Sauerstoff ermöglicht die Verarbeitung von reaktiven Metallen wie Titan und Tantal. | * Minimiert die Wechselwirkung zwischen geschmolzenem Metall und atmosphärischen Gasen * Ermöglicht die Herstellung von Teilen mit hoher Dichte und hervorragenden mechanischen Eigenschaften |
* Komplexe und teure Vakuumpumpsysteme erforderlich * Zusätzliche Überlegungen zur Feuchtigkeitskontrolle, um Spritzer und Unregelmäßigkeiten zu vermeiden |
Erzeugung von Elektronenstrahlen | Das Herzstück der EBM ist eine Elektronenkanone, die einen gebündelten Strahl hochenergetischer Elektronen aussendet. Ein elektrisches Feld erhitzt einen Glühfaden (Kathode), wodurch dieser Elektronen freisetzt. Diese Elektronen werden durch eine Hochspannung auf eine Anode beschleunigt und durch elektromagnetische Spulen weiter konzentriert. Der so entstehende Strahl weist eine außergewöhnliche Leistungsdichte auf und ist in der Lage, selbst hochschmelzende, refraktäre Metalle zu schmelzen. | * Präzise Kontrolle über Größe und Tiefe des Schmelzbeckens * Tiefes Eindringen für komplexe Geometrien mit inneren Merkmalen |
* Erfordert Hochspannung und ausgeklügelte Strahlenkontrollsysteme * Wartung und Kalibrierung der Elektronenkanone sind entscheidend |
Pulverförderung und -ausbringung | Ein Schaufel- oder Walzenmechanismus verteilt sorgfältig eine dünne Schicht Metallpulver auf der Bauplattform. Diese Schichtdicke, die in der Regel zwischen 30 und 100 Mikrometer beträgt, wird durch die gewünschte Auflösung und die Teilegeometrie vorgegeben. | * Gewährleistet eine gleichmäßige Schichtdicke für konstante Materialeigenschaften * Ermöglicht die Erstellung komplizierter Merkmale |
* Präzise Kontrolle des Pulververteilungsmechanismus ist entscheidend * Die Fließfähigkeit des Pulvers und die Partikelgrößenverteilung können die Streueffizienz beeinflussen. |
Selektives Schmelzen | Der Elektronenstrahl, der von computergesteuerten Abtastspiegeln geführt wird, schmilzt selektiv bestimmte Bereiche des Pulverbettes entsprechend einem aufgeschnittenen 3D-Modell auf. Das ungeschmolzene Pulver dient als Stütze für überhängende Strukturen, wodurch externe Stützstrukturen, wie sie bei anderen additiven Fertigungsverfahren üblich sind, überflüssig werden. | * Hohe Präzision und Genauigkeit bei der Erstellung komplexer Geometrien * Fähigkeit zur Erstellung interner Funktionen und Kanäle |
* Eine sorgfältige Planung des Scanpfads ist notwendig, um das Schmelzen zu optimieren und die Eigenspannung zu minimieren. |
Schicht für Schicht aufbauen | Nach dem Schmelzen einer einzelnen Schicht wird eine neue Pulverschicht darauf aufgebracht. Der Elektronenstrahl schmilzt dann selektiv bestimmte Bereiche innerhalb dieser neuen Schicht und verschmilzt sie mit der zuvor geschmolzenen Schicht. Dieser Prozess wird iterativ fortgesetzt, bis das gesamte 3D-Objekt fertiggestellt ist. | * Erzeugt schrittweise komplexe Geometrien * Ermöglicht eine effiziente Nutzung des Materials und minimiert den Abfall. |
* Die Bauzeit kann im Vergleich zu anderen AM-Verfahren aufgrund des schichtweisen Vorgehens länger sein. |
Wärmemanagement und Bauplattform | Das Wärmemanagement spielt beim EBM eine wichtige Rolle. Die Bauplattform wird in der Regel auf eine Temperatur knapp unter dem Schmelzpunkt des Pulvers vorgeheizt, um die Fließfähigkeit zu verbessern und die Verbindung zu fördern. Ein wassergekühlter Kupfertiegel unterstützt die Wärmeabfuhr und verhindert ein Verziehen des fertigen Teils. | * Minimiert thermische Spannungen und den Aufbau von Eigenspannungen * Trägt zur Maßhaltigkeit und Qualität der Teile bei |
* Eine sorgfältige Kontrolle der Vorwärmtemperatur und der Abkühlgeschwindigkeit ist erforderlich. |
Teileentnahme und Nachbearbeitung | Nach Abschluss des Bauprozesses wird die Kammer wieder auf Atmosphärendruck gebracht. Das gebaute Teil bleibt an der Bauplattform haften und muss getrennt werden. Eventuell vorhandene Stützstrukturen werden vorsichtig mit mechanischen Techniken entfernt. Je nach Anwendung können Nachbearbeitungsschritte wie Wärmebehandlung, heißisostatisches Pressen oder maschinelle Bearbeitung eingesetzt werden, um die gewünschte Oberflächenbeschaffenheit und mechanischen Eigenschaften zu erreichen. | * Minimierung der Nachbearbeitungsschritte durch hohe Dichte und netznahe Formgebung * Ermöglicht die Erstellung von Funktionsteilen |
* Die Entfernung erfordert Sorgfalt, damit empfindliche Teile nicht beschädigt werden. * Wärmebehandlung oder andere Nachbearbeitungsschritte können die Gesamtbearbeitungszeit verlängern. |
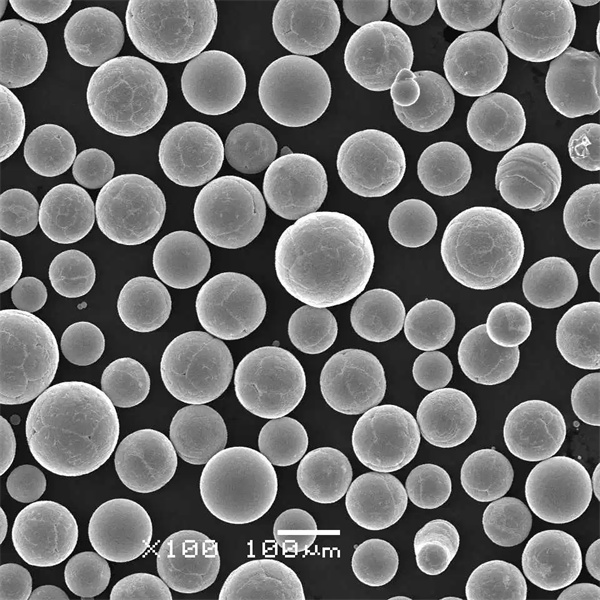
Wichtige Spezifikationen von Elektronenstrahl-Schmelzanlage
Spezifikation | Beschreibung | Auswirkungen auf Teilequalität und Produktion |
---|---|---|
Strahlleistung (kW) | Dies bezieht sich auf die gesamte Ausgangsleistung des Elektronenstrahls. | Eine höhere Strahlleistung führt zu schnelleren Schmelzgeschwindigkeiten und einem höheren Durchsatz. Sie ermöglicht auch die Verarbeitung dickerer Schichten und dichterer Materialien. Allerdings kann eine zu hohe Leistung zu Überhitzung und Verformung des Teils führen. |
Umschlag bauen (mm) | Dies definiert die maximalen Abmessungen (Länge, Breite, Höhe) eines Teils, das in einem einzigen Bauvorgang hergestellt werden kann. | Ein größerer Bauraum bietet eine größere Designflexibilität für komplexe Geometrien. Allerdings erhöht sich dadurch auch der Platzbedarf der Maschine, der Pulververbrauch und die Gesamtbauzeit. |
Vakuum Niveau (Pa) | Der Druck in der EBM-Kammer ist entscheidend für die Vermeidung von Oxidation und Verunreinigung während des Schmelzvorgangs. | Ein hohes Vakuum (niedriger Pa-Wert) gewährleistet eine minimale Wechselwirkung zwischen dem geschmolzenen Metall und den atmosphärischen Gasen, was zu Teilen mit hervorragenden mechanischen Eigenschaften und hoher Dichte führt. Das Erreichen und Aufrechterhalten eines tieferen Vakuums erfordert jedoch leistungsstärkere Pumpen, was die Kosten und die Komplexität der Maschine erhöht. |
Schichtdicke (μm) | Die Dicke jeder einzelnen Schicht des Metallpulvers, das während des Bauprozesses verteilt und geschmolzen wird. | Dünnere Schichten bieten feinere Details und glattere Oberflächen. Allerdings benötigen sie aufgrund der höheren Anzahl der benötigten Schichten mehr Zeit für den Aufbau. Umgekehrt können dickere Schichten schneller aufgebaut werden, was jedoch zu einer raueren Oberfläche und potenziellen inneren Porosität führen kann. |
Materialkompatibilität | Die Bandbreite an Metallpulvern, die das EBM-System verarbeiten kann. | Eine breitere Materialkompatibilität ermöglicht die Herstellung von Teilen aus verschiedenen Legierungen mit spezifischen Eigenschaften, die für verschiedene Anwendungen geeignet sind. Einige Werkstoffe haben jedoch einen höheren Schmelzpunkt oder erfordern eine spezielle Handhabung, was die Maschinenoptionen einschränken kann. |
In-Situ-Überwachung | Die Möglichkeit, den Schmelzprozess in Echtzeit mit Kameras oder anderen Sensoren zu überwachen. | Die In-situ-Überwachung ermöglicht die frühzeitige Erkennung von Fehlern wie Spritzern oder Schichtrissen, so dass noch während der Fertigung Korrekturmaßnahmen ergriffen werden können. Dies kann die Ausbeute erheblich verbessern und das Risiko von Bauteilausfällen verringern. |
Schmelzepool Geometriekontrolle | Der Grad der Präzision, mit dem der Elektronenstrahl fokussiert und manipuliert werden kann, um die Form des geschmolzenen Metallbades zu steuern. | Die präzise Steuerung des Schmelzbades minimiert wärmebeeinflusste Zonen und Eigenspannungen, was zu Teilen mit verbesserter mechanischer Leistung und Ermüdungsfestigkeit führt. Dies ist besonders wichtig für Anwendungen mit hohen Belastungsanforderungen. |
System zur Pulverbeschichtung | Der Mechanismus, der verwendet wird, um nach dem Schmelzen jeder Schicht frisches Metallpulver auf die Bauplattform zu bringen und zu verteilen. | Ein effizientes Wiederbeschichtungssystem gewährleistet eine gleichmäßige Pulverschichtdicke und minimiert das Risiko einer Verunreinigung durch Restpulverpartikel. Üblich sind blatt- und walzenbasierte Systeme, die jeweils ihre eigenen Vorteile und Einschränkungen haben. |
Software zur Unterstützung der Generierung | Die Software, die für den Entwurf und die Erstellung von Stützstrukturen innerhalb des 3D-Modells verwendet wird. | Gut konzipierte Stützstrukturen sind entscheidend für die Vermeidung von Bauteilverformungen und die Gewährleistung einer angemessenen Wärmeableitung während der Fertigung. Moderne Software kann die Platzierung der Stützen optimieren und den Materialabfall minimieren. |
Nachbearbeitungsanforderungen | Der Grad der Nachbearbeitung, der erforderlich ist, um die gewünschten endgültigen Teileigenschaften zu erreichen. | EBM-Teile erfordern in der Regel nur eine minimale Nachbearbeitung im Vergleich zu anderen additiven Fertigungsverfahren. Je nach Anwendung können jedoch die Entfernung der Stützstruktur und die Oberflächenbearbeitung erforderlich sein. |
Wirtschaftlichkeit der Einführung des Elektronenstrahlschmelzens
Faktor | Auswirkungen auf die Verabschiedung | Erläuterung |
---|---|---|
Investitionsausgaben | Hoch | EBM-Maschinen sind mit hohen Anschaffungskosten verbunden, die je nach Produktionsvolumen und Fähigkeiten zwischen $500.000 und mehreren Millionen Dollar liegen. Dies kann für kleinere Hersteller oder für diejenigen, die neu in der additiven Fertigung sind, eine erhebliche Hürde darstellen. |
Operative Kosten | Gemischt | EBM bietet zwar Vorteile wie geringeren Materialabfall und eine endkonturnahe Fertigung, verursacht aber auch Kosten für Pulvermaterial, Energieverbrauch (aufgrund des Hochleistungselektronenstrahls) und mögliche Nachbearbeitungsschritte wie die Entfernung von Trägern. Diese Kosten können jedoch durch den geringeren Bearbeitungsaufwand und die verbesserte Leistung der Teile ausgeglichen werden. |
Teil Komplexität | Positiv | EBM zeichnet sich durch die Herstellung komplexer, nahezu unmöglicher Geometrien mit internen Kanälen und Gittern aus. Dies eröffnet Designfreiheit für leichte, hochfeste Komponenten in der Luft- und Raumfahrt, der Medizintechnik und anderen Branchen. Die Fähigkeit, komplizierte Merkmale zu erzeugen, kann die höheren Kosten rechtfertigen, die mit EBM verbunden sind. |
Produktionsvolumen | Begrenzt | EBM-Maschinen haben im Vergleich zu einigen anderen additiven Fertigungstechnologien langsamere Fertigungsraten. Daher eignen sie sich weniger für große Produktionsserien. Allerdings glänzt EBM bei Anwendungen, bei denen Individualisierung, kleine Losgrößen und Leistung von größter Bedeutung sind. |
Materialkompatibilität | Erweitern Sie | EBM kann ein breiteres Spektrum an Materialien verarbeiten als viele andere 3D-Druckverfahren, darunter reaktive und refraktäre Metalle, einige Legierungen und sogar bestimmte Keramiken. Diese Vielseitigkeit öffnet Türen für neue Anwendungen in anspruchsvollen Umgebungen. Die fortlaufende Entwicklung kompatibler Materialien wird die Akzeptanz weiter fördern. |
Arbeit und Fachwissen | Spezialisiert | Der Betrieb und die Wartung von EBM-Maschinen erfordern qualifiziertes Personal mit Kenntnissen über Vakuumsysteme, Elektronenstrahltechnologie und Metallpulverhandhabung. Der Mangel an solchem Fachwissen kann für einige Unternehmen eine Hürde darstellen, was sich auf die Akzeptanz auswirkt. |
Rentabilität der Investition (ROI) | Langfristig | Die wirtschaftliche Lebensfähigkeit von EBM hängt von einer langfristigen Perspektive ab. Zwar sind die Anfangskosten hoch, aber die Vorteile von EBM (z. B. leichtere, stabilere Teile, weniger Abfall) führen häufig zu Kosteneinsparungen und Leistungsverbesserungen über den gesamten Lebenszyklus eines Produkts. |
Staatliche Anreize | Positiv | Staatliche Unterstützung für Forschung und Entwicklung im Bereich der additiven Fertigung, einschließlich EBM, kann die Einführung beschleunigen, indem sie die Eintrittsbarrieren senkt und die Innovation fördert. Steuererleichterungen oder Zuschüsse können Anreize für Unternehmen schaffen, in die EBM-Technologie zu investieren. |
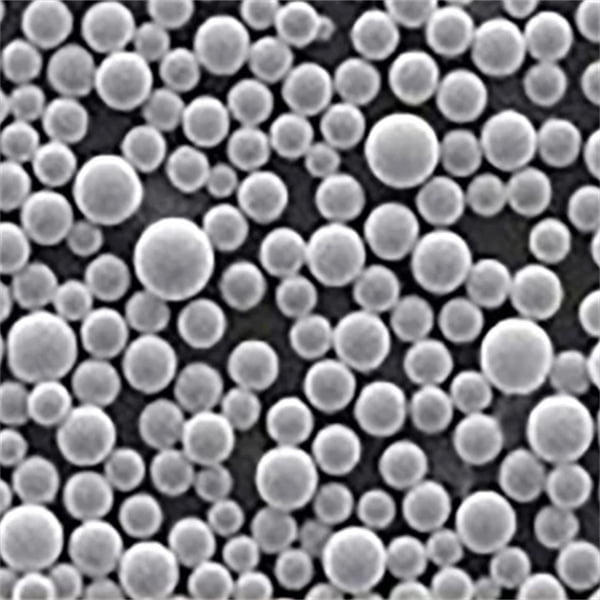
Beliebte Materialien für EBM
Material Klasse | Beispiele für Legierungen | Eigenschaften | Anwendungen |
---|---|---|---|
Titan-Legierungen | Ti-6Al-4V, Ti-6Al-4V ELI | * Ausgezeichnetes Verhältnis von Festigkeit zu Gewicht * Hohe Biokompatibilität * Korrosionsbeständig |
* Komponenten für die Luft- und Raumfahrt (Tragflächen, Fahrwerk) * Medizinische Implantate (Knieprothesen, Zahnimplantate) * Sportartikel (Golfschläger, Fahrradrahmen) |
Nickel-Basis-Legierungen | Inconel 625, Inconel 718 | * Außergewöhnliche Hochtemperaturfestigkeit * Oxidations- und Korrosionsbeständigkeit * Gute Schweißbarkeit |
* Turbinenschaufeln und -scheiben für Düsentriebwerke * Wärmetauscher für die chemische Verarbeitung * Laufradwellen für Pumpen |
Kobalt-Chrom-Legierungen | CoCrMo, Haynes 214 | * Hohe Verschleißfestigkeit * Biokompatibel (begrenzte Anwendungen) * Gute Härte |
* Gelenkersatz (Hüfte, Knie) * Schneidwerkzeuge und Verschleißteile * Zahnimplantate (eingeschränkte Verwendung wegen möglicher Bedenken hinsichtlich Chrom) |
Rostfreie Stähle | 17-4PH, 316L | * Gute Korrosionsbeständigkeit * Mäßige Stärke * Biokompatibel (begrenzte Anwendungen) |
* Medizinische Instrumente * Chemische Verarbeitungsanlagen * Komponenten für die Lebensmittel- und Getränkeindustrie |
Aufkommende Materialien | * Wolfram (W) * Tantal (Ta) * Niob (Nb) * Molybdän (Mo) | * Ultrahoher Schmelzpunkt * Ausgezeichnete Hochtemperatureigenschaften * Begrenzte Forschung und Entwicklung |
* Mögliche Anwendungen in der Luft- und Raumfahrt, im Verteidigungsbereich und in der Nuklearindustrie (aufgrund des hohen Schmelzpunkts und der Beständigkeit gegen extreme Umgebungsbedingungen) |
Vorteile des Elektronenstrahlschmelzens
Nutzen Sie | Beschreibung | Auswirkungen |
---|---|---|
Hochdichte, nahezu netzförmige Teile | EBM erzeugt Teile mit einer Dichte von mehr als 99,5% der theoretischen Dichte des verwendeten Metallpulvers. Dadurch wird die bei anderen additiven Fertigungsverfahren übliche Porosität (winzige Lufteinschlüsse) beseitigt, was zu Teilen mit außergewöhnlicher Festigkeit, Ermüdungsbeständigkeit und Maßhaltigkeit führt. | Dies ermöglicht die Herstellung funktioneller Metallkomponenten für anspruchsvolle Anwendungen in der Luft- und Raumfahrt (Turbinenschaufeln, Triebwerksgehäuse), in der Medizin (Zahnimplantate, Prothesen) und in der Automobilindustrie (leichte, leistungsstarke Teile). |
Hervorragende mechanische Eigenschaften | Durch die Hochvakuumumgebung und den präzisen Schmelzprozess im EBM werden Oxidation und Verunreinigung minimiert, so dass die inhärenten Eigenschaften des Metallpulvers erhalten bleiben. Dies führt zu Teilen mit hervorragender Zugfestigkeit, Kriechfestigkeit (Fähigkeit, Verformungen unter Belastung bei hohen Temperaturen standzuhalten) und Bruchzähigkeit. | Die von EBM hergestellten Teile können erheblichen Belastungen standhalten, arbeiten effektiv bei hohen Temperaturen und widerstehen der Rissausbreitung, was sie ideal für Anwendungen macht, die eine lange Lebensdauer und strukturelle Integrität in rauen Umgebungen erfordern. |
Verarbeitung von refraktären und reaktiven Metallen | Im Gegensatz zu herkömmlichen Herstellungsverfahren, die durch hohe Schmelzpunkte und Reaktivität eingeschränkt sind, eignet sich EBM hervorragend für die Verarbeitung anspruchsvoller Materialien wie Titanlegierungen, Tantal und Inconel. Die Vakuumumgebung verhindert Oxidation und ermöglicht eine präzise Steuerung des Schmelzprozesses, was eine erfolgreiche Fertigung gewährleistet. | Dies erweitert die Konstruktionsmöglichkeiten für Branchen wie die Luft- und Raumfahrt und die Biomedizin, wo Bauteile ein außergewöhnliches Verhältnis von Festigkeit zu Gewicht, Biokompatibilität (Kompatibilität mit lebendem Gewebe) und Hochtemperaturleistung erfordern. |
Gestaltungsfreiheit für komplexe Geometrien | Der schichtweise Ansatz von EBM ermöglicht die Schaffung komplizierter interner Merkmale, Kanäle und Gitterstrukturen, die mit herkömmlichen Techniken nicht möglich sind. Diese Designflexibilität optimiert die Gewichtsverteilung, verbessert die Wärmeübertragung und ermöglicht die Herstellung von Komponenten mit überlegener Funktionalität. | Dieser Vorteil revolutioniert das Produktdesign in Branchen wie der Luft- und Raumfahrt, wo leichte, hochfeste Komponenten mit komplexen Kühlkanälen für die Effizienz von Motoren entscheidend sind. Er ermöglicht auch die Herstellung maßgeschneiderter medizinischer Implantate, die perfekt auf die Anatomie eines Patienten abgestimmt sind. |
Minimale Unterstützungsstrukturen | Aufgrund der hohen Eigenfestigkeit der mit EBM hergestellten Teile sind während des Bauprozesses nur minimale Stützstrukturen erforderlich. Dies reduziert die Nachbearbeitungszeit und den Materialabfall sowie das Risiko einer Beschädigung der Stützstrukturen am fertigen Bauteil. | Dies führt zu kürzeren Produktionszeiten, niedrigeren Gesamtkosten und der Möglichkeit, komplizierte Geometrien zu erstellen, die mit herkömmlichen Methoden nur schwer oder gar nicht zu realisieren wären. |
Reduzierter Materialabfall | EBM ist ein additives Fertigungsverfahren, d. h. das Material wird schichtweise hinzugefügt, um die gewünschte Form zu erhalten. Dies minimiert den Materialabfall im Vergleich zu subtraktiven Verfahren wie der maschinellen Bearbeitung, bei der ein erheblicher Teil des Rohmaterials entfernt wird, um die endgültige Form zu erhalten. | Dieser Vorteil fördert die Nachhaltigkeit und senkt die Produktionskosten durch die Maximierung der Materialausnutzung. Darüber hinaus kann unbenutztes Pulver aus der Baukammer oft für nachfolgende Bauvorgänge wiederverwendet werden, was den Abfall weiter minimiert. |
Überblick über Elektronenstrahl-Schmelzanlage Anbieter
Eine Vielzahl etablierter industrieller Hersteller und spezialisierter neuer Marktteilnehmer bieten Lösungen für das Elektronenstrahlschmelzen an, die von der Forschung bis zur Großserienproduktion in der Luft- und Raumfahrt, der Medizintechnik, der Automobilindustrie und der Industrie skalierbar sind.
Tabelle 8: Führende Hersteller von Elektronenstrahlschmelzsystemen
Anbieter | Einzelheiten | Ziel-Segmente |
---|---|---|
GE-Zusatzstoff | Pionier der EBM-Technologie | Luft- und Raumfahrt, Medizintechnik, Automobilindustrie |
Sciaky | Größte Umschlaggröße | Strukturen für die Luft- und Raumfahrt |
Wayland-Zusatzstoff | Preisgünstige Metall-AM-Plattformen | Kleine Maschinenbaubetriebe |
JEOL | EBM-Systeme für die Forschung | Universitäten |
Nanodimension | Multi-Material-Fähigkeiten | Elektronik, Verteidigung |
Der Branchenführer Arcam EBM, jetzt Teil von GE Additive, hat sich dank patentierter Lösungen schon früh eine Führungsposition erarbeitet und dominiert weiterhin die etablierten Kategorien medizinische Implantate und Luft- und Raumfahrt.
In der Zwischenzeit versuchen neue Marktteilnehmer wie Wayland, die Akzeptanz zu erhöhen, indem sie sich mit kostengünstigen Startplattformen an kleine und mittlere Hersteller wenden.
Die Zusammenarbeit zwischen Herstellern, Forschern und Endnutzern in den Bereichen Werkstoffe, Bauteilqualifizierung und Maschinenoptimierung wird letztlich dazu führen, dass sich EBM in weiteren kritischen Anwendungen durchsetzt.

Zukunftsaussichten für die Einführung des Elektronenstrahlschmelzens
Aufgrund der überragenden Produktionsgeschwindigkeit und der außergewöhnlichen mechanischen Eigenschaften, die mit anderen additiven oder konventionellen Verfahren nicht möglich sind, scheint die Einführung von EBM in der Luft- und Raumfahrt, in der Medizintechnik, in der Automobilindustrie und in der Industrie in den nächsten 5 bis 7 Jahren massiv zuzunehmen.
Es wird erwartet, dass ein breiteres Bewusstsein für die Vorteile von EBM über das Prototyping hinaus bis hin zur Serienproduktion die Investitionen in Anlagen vorantreiben wird, da Unternehmen den 3D-Druck nutzen, um ihre Lieferketten neu zu gestalten.
Größere Bauräume, die jetzt im Handel erhältlich sind, ermöglichen auch die Konsolidierung von Baugruppen in weniger Komponenten, wodurch die Lagerlogistik und die Vorlaufzeiten weiter optimiert werden.
Sinkende Systemkosten in Verbindung mit einer höheren Materialverfügbarkeit müssen jedoch den Zugang kleinerer Hersteller zur EBM-Technologie weiter verbessern. Die Rationalisierung von Hilfsmitteln für die Pulverhandhabung und von Nachbearbeitungsabläufen wird die Einführung ebenfalls erleichtern.
Insgesamt erhält EBM eine starke Dynamik aufrecht, um eine immer breitere Palette von Produktionsanwendungen zu durchdringen, dank unübertroffener Abscheidungsraten und außergewöhnlicher Materialeigenschaften im Vergleich zu alternativen Metalladditiven oder herkömmlichen Herstellungsverfahren.
FAQ
F: Welche Infrastruktur ist erforderlich, um EBM zu unterstützen?
A: Rechnen Sie mit mehr als 500 m² für die Maschine selbst, mit mehr Platz für Pulverhandhabungsstationen und Nachbearbeitung. Eine Betonbodenverstärkung für Maschinenlasten von mehr als 12.000 Pfund ist typisch.
F: Wie viele Bediener werden pro EBM-Maschine benötigt?
A: Je nach Automatisierungsgrad und Produktionsvolumen kann ein Techniker mehrere EBM-Einheiten betreuen. Zusätzliches Personal kümmert sich um den Pulverbetrieb, Nachbearbeitungsaufgaben, Wartung und Technik.
F: Welche Materialien können nicht mit der EBM-Technologie verarbeitet werden?
A: Nicht leitende Polymere können nicht mit Elektronenstrahlen bearbeitet werden. EBM eignet sich jedoch für praktisch alle leitfähigen Metalllegierungssysteme, die sonst hergestellt werden können.
F: Welche Sicherheitsrisiken sind mit der EBM-Technologie verbunden?
A: Elektronenstrahl-Hochspannung birgt das Risiko eines Lichtbogens und erfordert entsprechende Schutzmaßnahmen und Kontrollen. Die Exposition gegenüber reaktivem Metallpulver erfordert auch Protokolle für Brand- und Inhalationsgefahren, die Schutzausrüstung und Schulungen erfordern.
F: Ist für EBM eine zweite Wärmebehandlung erforderlich?
A: Bestimmte Legierungen profitieren von einer Wärmebehandlung, um das Gefüge weiter zu verbessern und die mechanischen Eigenschaften anzupassen. Durch die schnellen Erstarrungszyklen und die hohen Vorwärmtemperaturen, die dem EBM-Verfahren eigen sind, entfallen diese Nachbearbeitungsschritte jedoch in der Regel.