Spritzgussfähiges Pulver bezieht sich auf eine Art von Ausgangsmaterial, das beim Pulverspritzgießen verwendet wird, einem industriellen Fertigungsverfahren zur Herstellung komplexer und hochpräziser Metallteile. Dieses Pulver ist eine Mischung aus feinen Metallpulvern und polymeren Bindemitteln, die im Spritzgussverfahren in großen Mengen zu komplexen netzförmigen Teilen verarbeitet werden können.
Vorteile der Verwendung von spritzgießbarem Pulver
Vorteil | Beschreibung | Nutzen Sie |
---|---|---|
Komplexe Geometrien: IMP ermöglicht die Herstellung komplizierter Formen mit feinen Merkmalen, die mit herkömmlichen Spritzgießtechniken nur schwer oder gar nicht zu erreichen sind. Diese Designfreiheit öffnet die Türen für innovative Komponenten in verschiedenen Branchen. | Im Gegensatz zu herkömmlichen Formmaterialien wie geschmolzenen Kunststoffen wird bei IMP ein Bindemittelsystem verwendet, das die Pulverpartikel während des Formprozesses zusammenhält. Dies ermöglicht die Herstellung von Teilen mit inneren Kanälen, Hinterschneidungen und anderen komplexen Geometrien. | |
Materialeffizienz: IMP fördert die endkonturnahe Fertigung und minimiert den Materialabfall im Vergleich zu subtraktiven Verfahren wie der spanenden Bearbeitung. Dies ist besonders bei teuren oder leistungsstarken Materialien von Vorteil. | Die präzise Steuerung der Pulververteilung während des Spritzgießens minimiert den übermäßigen Materialverbrauch. Im Gegensatz zu herkömmlichen Verfahren, bei denen während der Probeläufe Ausschuss anfällt, ermöglicht IMP außerdem schnellere Design-Iterationen bei minimalem Materialabfall. | |
Breite Materialauswahl: IMP bietet im Vergleich zum traditionellen Spritzgießen eine größere Auswahl an Materialien. Diese Vielseitigkeit ermöglicht die Herstellung von Teilen mit spezifischen, auf die jeweilige Anwendung zugeschnittenen Eigenschaften. | Neben den Standardpolymeren, die beim Spritzgießen verwendet werden, kann IMP auch Metallpulver, Keramik und sogar Verbundwerkstoffe einsetzen. Dies ermöglicht die Herstellung von Teilen mit einzigartigen Kombinationen von Festigkeit, Leitfähigkeit oder Biokompatibilität. | |
Leistungsstarke Teile: Die Fähigkeit, Metall- und Keramikpulver in IMP zu verwenden, ermöglicht die Herstellung von Hochleistungsteilen mit außergewöhnlicher Festigkeit, Hitzebeständigkeit oder Abnutzungseigenschaften. | Spritzgegossene Metallteile (MIM) können mechanische Eigenschaften erreichen, die mit denen von Knetmetallen vergleichbar sind, so dass sie sich für anspruchsvolle Anwendungen eignen. Ähnlich bieten keramische IMP-Teile eine hervorragende Verschleißfestigkeit und Hochtemperaturleistung. | |
Potenzial für die Massenproduktion: Ursprünglich wurde die IMP-Technologie für die Herstellung von Prototypen verwendet, ist aber inzwischen so ausgereift, dass sie eine kostengünstige Massenproduktion komplexer Teile ermöglicht. | Der hohe Automatisierungsgrad der IMP-Prozesse ermöglicht eine effiziente Produktion großer Mengen von Teilen mit gleichbleibender Qualität. Dies macht es zu einer praktikablen Option für Anwendungen mit hohen Stückzahlen. | |
Verbesserte Oberflächengüte: Im Vergleich zu herkömmlichen Metallgusstechniken kann mit IMP manchmal eine glattere Oberfläche der fertigen Teile erzielt werden. | Durch die Verwendung von feinen Pulvern und den kontrollierten Formgebungsprozess können Oberflächenfehler minimiert werden, so dass möglicherweise weniger umfangreiche Nachbearbeitungsschritte wie Polieren erforderlich sind. |
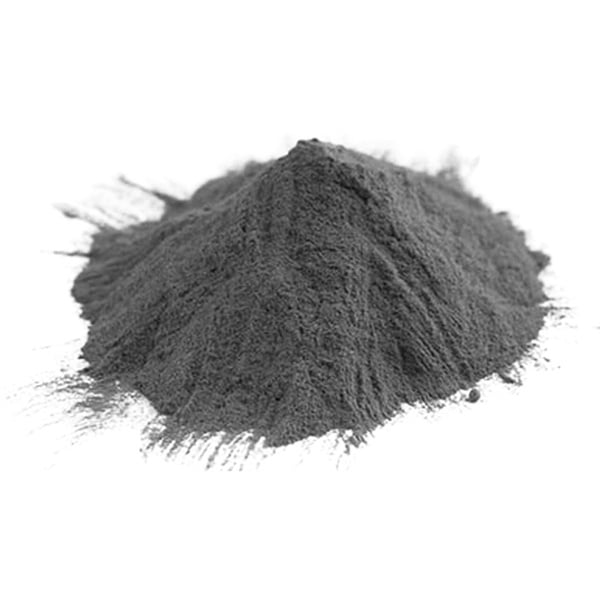
Zusammensetzung des spritzgießbaren Pulvers
Komponente | Beschreibung | Funktion |
---|---|---|
Basis-Pulver | Sie bilden das primäre Funktionsmaterial des endgültigen Teils und können in drei Haupttypen eingeteilt werden: Metall-Pulver: Fein verteilte metallische Partikel aus verschiedenen Legierungen, wie Edelstahl, Werkzeugstahl oder Superlegierungen. Keramische Pulver: Keramische Materialien wie Aluminiumoxid, Zirkoniumdioxid oder Siliziumnitrid in Pulverform. Polymer-Pulver: Thermoplastische Polymere, die üblicherweise beim Spritzgießen verwendet werden, wie Nylon oder Polypropylen. |
Die Wahl des Basispulvers bestimmt die endgültigen Eigenschaften des Formteils, wie Festigkeit, Verschleißfestigkeit oder thermische Leistung. |
Bindemittel-System | Es handelt sich dabei um eine entscheidende Komponente, die als temporärer Klebstoff fungiert und die Basis-Pulverteilchen während des Formprozesses zusammenhält. Das Bindemittelsystem besteht in der Regel aus: Thermoplastisches Polymer: Ein thermoplastischer Kunststoff, der während des Spritzgießens schmilzt und die Fließfähigkeit und Haftung mit dem Grundpulver ermöglicht. * Wachse oder Zusatzstoffe: Diese können die Fließeigenschaften verbessern, die Entbinderungseffizienz erhöhen oder die Dispersion des Pulvers im Bindemittel unterstützen. |
Das Bindemittelsystem sorgt dafür, dass sich das Pulver beim Einspritzen wie ein formbares Ausgangsmaterial verhält und ermöglicht die Herstellung komplexer Formen. |
Porenbildner | Dies sind optionale Zusatzstoffe, die temporäre Poren im Formteil erzeugen. Sie können sein: * Organische Materialien: Diese brennen beim Entbindern aus und hinterlassen ein Netz von Poren, die das Entfernen des Bindemittelsystems erleichtern. * Chemische Auslaugungsmittel: Diese lösen sich in einem speziellen Lösungsmittel während eines Nachbearbeitungsschritts auf, wodurch eine kontrollierte Porenstruktur entsteht. | Porenbildner ermöglichen die Schaffung poröser Strukturen im fertigen Teil, was für Anwendungen wie Filter oder Knochenimplantate von Vorteil sein kann. |
Merkmale des verwendeten Metallpulvers
Charakteristisch | Beschreibung | Bedeutung für MIM |
---|---|---|
Partikelgröße und -verteilung | Die Größe und Verteilung der Metallpulverpartikel hat einen erheblichen Einfluss auf die folgenden Aspekte von MIM: Formfüllung & Grünfestigkeit: Feinere Pulver bieten in der Regel eine bessere Packungsdichte und können die Formfüllung beim Einspritzen verbessern. Zu feine Partikel können jedoch die Fließfähigkeit beeinträchtigen und zu Problemen bei der Verarbeitung führen. Eine enge Partikelgrößenverteilung gewährleistet eine gleichmäßige Packung und minimiert Hohlräume im Formteil, was zu einer guten Grünfestigkeit (Festigkeit des Teils vor dem Sintern) beiträgt. Sinterverhalten und endgültige Eigenschaften: Die Partikelgröße beeinflusst den Sinterprozess, bei dem sich die Partikel zu einer festen Struktur verbinden. Pulver mit einer größeren Größenverteilung können zu einer inhomogenen Sinterung führen und möglicherweise die endgültigen mechanischen Eigenschaften des Teils beeinträchtigen. |
Die sorgfältige Auswahl der Partikelgröße und -verteilung ist entscheidend für eine gute Formfüllung, Grünfestigkeit und optimale Leistung des endgültigen Sinterteils. |
Morphologie der Partikel | Dies bezieht sich auf die Form der Metallpulverpartikel. Im Idealfall bevorzugen MIM-Verfahren Pulver mit kugelförmiger oder nahezu kugelförmiger Morphologie. | Sphärische Partikel fließen leichter und verbessern die Formfüllung und Packungsdichte. Unregelmäßig geformte Partikel können Hohlräume bilden und die Fließfähigkeit behindern, was zu Defekten im Formteil führen kann. |
Offensichtliche Dichte und Klopfdichte | Diese Eigenschaften stellen die Schüttdichte des Pulvers unter verschiedenen Bedingungen dar. Scheinbare Dichte: Dies bezieht sich auf die Dichte des Pulvers im Ruhezustand unter Berücksichtigung der Zwischenräume zwischen den Partikeln. Dichte der Gewindebohrer: Dies spiegelt einen dichteren Zustand wider, der durch ein standardisiertes Zapfverfahren erreicht wird. |
Eine höhere Gewindedichte ist bei MIM im Allgemeinen wünschenswert, um eine effiziente Materialausnutzung und eine gute Maßgenauigkeit des Endprodukts zu erreichen. Sie trägt auch zu einer besseren Packung während des Formens bei und minimiert die Schrumpfung während des Sinterns. |
Chemische Zusammensetzung | Die spezifischen Elemente oder Legierungen, die im Metallpulver verwendet werden, bestimmen die endgültigen Eigenschaften des gesinterten Teils. | Durch die Wahl der Zusammensetzung des Metallpulvers lassen sich Eigenschaften wie Festigkeit, Korrosionsbeständigkeit oder Verschleißfestigkeit auf die spezifischen Anforderungen der Anwendung abstimmen. Beim MIM können verschiedene Metalllegierungen verwendet werden, darunter Edelstahl, Werkzeugstahl und sogar Hochleistungslegierungen wie Inconel. |
Fließfähigkeit | Dies bezieht sich auf die Leichtigkeit, mit der das Pulver unter Schwerkraft oder Krafteinwirkung fließt. | Eine gute Fließfähigkeit ist für eine gleichmäßige Verteilung des Pulvers beim Spritzgießen unerlässlich. Pulver mit schlechter Fließfähigkeit können zu Unregelmäßigkeiten in der Packungsdichte und möglichen Defekten im fertigen Teil führen. |
Normen für Metallpulver
Die verwendeten Metallpulver müssen den Normen für Zusammensetzung und Körnung entsprechen:
Standardgehäuse | Standard | Beschreibung | Bedeutung in der IMP |
---|---|---|---|
ASTM International (ASTM) | ASTM B930 - Standard Guide for Powder Characterization of Metal Injection Molding (MIM) Feedstock | Diese Norm beschreibt verschiedene Prüfverfahren zur Charakterisierung der Eigenschaften von Metallpulvern, die für MIM verwendet werden. | Bietet einen Rahmen für die Bewertung von Faktoren wie Partikelgrößenverteilung, Morphologie, Fließfähigkeit und scheinbare Dichte. Dies gewährleistet Konsistenz und Qualitätskontrolle bei den für IMP-Anwendungen verwendeten Metallpulvern. |
** | ** | * ASTM B783 - Standard Specification for Stainless Steel Powders for Metal Injection Molding (MIM) Applications | Diese Norm definiert spezifische Anforderungen an die chemische Zusammensetzung, die Partikelgrößenverteilung und die Fließfähigkeit von Edelstahlpulvern, die für MIM verwendet werden. |
** | ** | * ASTM D4000 - Standardklassifizierungssystem für die Spezifikation von Kunststoffmaterialien | Diese Norm bezieht sich zwar nicht ausschließlich auf IMP, bietet aber ein Klassifizierungssystem für verschiedene Arten von Kunststoffen, einschließlich solcher, die möglicherweise als Bindemittel in IMP-Rohstoffen verwendet werden. |
Internationale Organisation für Normung (ISO) | * ISO 3095 - Metallische Pulver - Bestimmung der Durchflussmenge mit einem Hall-Durchflussmesser | Diese Norm legt ein Verfahren zur Messung der Fließfähigkeit von Metallpulvern mit einem Hall-Durchflussmesser fest. | Bietet einen standardisierten Ansatz für die Bewertung der Fließfähigkeit, ein entscheidendes Merkmal für eine gute Formfüllung und gleichbleibende Teilequalität bei IMP. |
** | ** | * ISO 4497 - Kunststoffe - Bestimmung der Schmelzflussrate (MFR) und der Schmelzvolumenflussrate (MVR) von Thermoplasten | Diese Norm beschreibt ein Verfahren zur Messung der Schmelzflussrate (MFR) von thermoplastischen Materialien, die für die Bindemittelkomponente in IMP-Rohstoffen relevant sein kann. |
Schritte im Herstellungsprozess
Der Herstellungsprozess umfasst die folgenden Hauptschritte:
Schritt | Beschreibung | Bedeutung |
---|---|---|
1. Pulveraufbereitung & Mischen | Das Grundpulver (Metall, Keramik oder Polymer) wird sorgfältig ausgewählt und entsprechend den gewünschten Endeigenschaften vorbehandelt. Zusatzstoffe wie Porenbildner oder Schmiermittel können beigefügt werden. Das Pulver wird dann genau gewogen und mit dem Bindemittelsystem gemischt, um ein homogenes Ausgangsmaterial zu erhalten. | In diesem Schritt wird die Grundlage für die Eigenschaften des endgültigen Teils geschaffen. Die sorgfältige Auswahl und das genaue Mischen gewährleisten ein gleichmäßiges Materialverhalten während der Verarbeitung. |
2. Spritzgießen | Das vorbereitete IMP-Rohmaterial wird bis zu einem halbgeschmolzenen Zustand erhitzt und unter hohem Druck in einen geschlossenen Formhohlraum eingespritzt. Das Werkzeug bildet die gewünschte Form des endgültigen Teils nach. | In dieser Phase wird die Geometrie des Teils festgelegt. Ein gleichmäßiger Durchfluss und Druck während der Einspritzung sind entscheidend, um genaue Teileabmessungen und minimale Fehler zu erzielen. |
3. Entbinden | Das geformte Teil, auch "Grünteil" genannt, wird einem Entbinderungsprozess unterzogen, um das Bindersystem zu entfernen. Dies kann erreicht werden durch: * Lösungsmittel-Entbinderung: Das Teil wird in ein Lösungsmittel getaucht, das das Bindemittel auflöst und die Pulverstruktur zurücklässt. * Thermisches Entbindern: Das Teil wird einem kontrollierten Erhitzungszyklus unterzogen, bei dem sich das Bindemittel thermisch zersetzt und als Gas entweicht. | Eine wirksame Entbinderung ist entscheidend, um die gewünschte Endform und Porosität zu erreichen, ohne die empfindliche Pulverstruktur zu beschädigen. |
4. Sintern | Das entbinderte Teil wird hohen Temperaturen in einer kontrollierten Atmosphäre (oft unter Vakuum oder Inertgas) ausgesetzt. Dieser Prozess fördert die Diffusion und Bindung zwischen den Pulverpartikeln, wodurch ein festes und nahezu netzförmiges Bauteil entsteht. | Das Sintern bestimmt die endgültigen mechanischen Eigenschaften des Teils, wie Festigkeit, Dichte und Maßhaltigkeit. Eine präzise Temperaturkontrolle und Atmosphärenmanagement sind unerlässlich. |
5. Nachbearbeitung | Je nach den Erfordernissen der Anwendung kann das gesinterte Teil zusätzlichen Veredelungsschritten unterzogen werden, wie z. B.: * Zerspanung oder Schleifen: Zum Erreichen präziser Maßtoleranzen oder Oberflächengüten. * Wärmebehandlung: Zur Verbesserung bestimmter mechanischer Eigenschaften wie Festigkeit oder Härte. * Beschichtung oder Infiltration: Zur Verbesserung von Oberflächeneigenschaften wie Verschleißfestigkeit oder Korrosionsbeständigkeit. | Nachbearbeitungen können die Funktionalität und Ästhetik des endgültigen IMP-Teils weiter verbessern. |
Anwendungen von Spritzgussteilen
Spritzgussfähiges Pulver kann für die Herstellung verschiedener komplizierter und hochpräziser Teile in verschiedenen Branchen verwendet werden:
Industrie | Anwendungsbeispiele | Vorteile des Spritzgießens |
---|---|---|
Automobilindustrie | Innenraumkomponenten (Armaturenbretter, Türverkleidungen, Konsolen) Teile unter der Motorhaube (Gebläseabdeckungen, Ansaugkrümmer) Funktionelle Komponenten (Zahnräder, Kettenräder) |
Großserienproduktion von komplexen Formen mit präzisen Merkmalen. Leichte Teile für bessere Kraftstoffeffizienz. Große Auswahl an Materialien für unterschiedliche Leistungsanforderungen (Haltbarkeit, Hitzebeständigkeit). |
Unterhaltungselektronik | Elektronikgehäuse (Telefone, Laptops, Tablets) Steckverbinder und Tasten Interne Komponenten (Klammern, Zahnräder) |
Massenproduktion komplizierter Teile mit hoher Maßhaltigkeit. Glatte Oberflächen für Ästhetik und Benutzerkomfort. Eine Vielzahl von Farben und Texturen kann durch die Wahl des Materials und der Formgebungstechniken erreicht werden. |
Medizinische Geräte | Chirurgische Instrumente (Griffe, Griffe) Prothesenkomponenten (Kniegelenke, Zahnimplantate) Medizinische Einwegkomponenten (Spritzen, Fläschchen) |
Sterilisierbare Materialien für Hygiene und Sicherheit. Biokompatible Materialien zur Verwendung im menschlichen Körper (bestimmte Polymere und Metalllegierungen). Komplexe Geometrien für präzise Funktionalität in medizinischen Anwendungen. |
Luft- und Raumfahrt & Verteidigung | Flugzeugkomponenten (Kanäle, Fahrwerksteile) Satellitenkomponenten (Halterungen, Gehäuse) Verteidigungsausrüstung (Helme, Waffenteile) |
Leichte und hochfeste Materialien zur Gewichtsreduzierung in der Luft- und Raumfahrt. Flammhemmende oder hitzebeständige Materialien für besondere Anforderungen. Langlebige Teile für raue Umgebungen und anspruchsvolle Betriebsbedingungen. |
Konsumgüter | Spielzeug und Spiele Geräte (Gehäuse, Knöpfe, Zifferblätter) Sportartikel (Helme, Fahrradteile) |
Kosteneffiziente Produktion für hochvolumige Verbraucherprodukte. Große Auswahl an Farben und Oberflächen für eine ansprechende Optik. Langlebige und funktionelle Teile für den täglichen Gebrauch. |
Vorteile des Spritzgießens für die Teileherstellung
Vorteil | Beschreibung | Nutzen Sie |
---|---|---|
Großserienproduktion: Das Spritzgießen eignet sich hervorragend für die effiziente Herstellung großer Mengen identischer Teile. Die Automatisierungsmöglichkeiten und schnellen Zykluszeiten ermöglichen eine kostengünstige Massenproduktion. | Dies ist besonders vorteilhaft für Produkte, die Millionen von Einheiten erfordern, wie z. B. Unterhaltungselektronik oder Automobilkomponenten. Gleichbleibende Qualität und Wiederholbarkeit sind während des gesamten Produktionslaufs gewährleistet. | |
Flexibilität bei der Gestaltung: Das Spritzgießen ermöglicht eine Vielzahl komplexer Geometrien, einschließlich komplizierter Formen, dünner Wände und innerer Merkmale. Diese Gestaltungsfreiheit ermöglicht die Herstellung funktioneller und innovativer Teile. | Im Gegensatz zu einigen subtraktiven Fertigungsverfahren ist das Spritzgießen nicht durch die Werkzeuggeometrie begrenzt. Hinterschneidungen, Kanäle und andere komplexe Merkmale können direkt in das Teil gegossen werden. | |
Maßgenauigkeit und Wiederholbarkeit: Die präzise Steuerung der Werkzeugkonstruktion und der Einspritzparameter ermöglicht gleichbleibende und genaue Teileabmessungen bei hohen Produktionsmengen. | Dies minimiert die Notwendigkeit von Nachbearbeitungsschritten zur Maßkorrektur und gewährleistet austauschbare Teile für die Montage. Die Reproduzierbarkeit ist entscheidend für die Aufrechterhaltung einer gleichbleibenden Produktqualität und Funktionalität. | |
Große Materialauswahl: Beim Spritzgießen kann eine breite Palette von Materialien verwendet werden, darunter Thermoplaste, Duroplaste, Elastomere und sogar einige Metalllegierungen (durch Metal Injection Molding - MIM). | Diese Vielseitigkeit ermöglicht die Auswahl des optimalen Materials auf der Grundlage der gewünschten Eigenschaften wie Festigkeit, Hitzebeständigkeit, chemische Beständigkeit oder Flexibilität. | |
Oberflächengüte und Ästhetik: Im Spritzgussverfahren können Teile mit glatten und hochwertigen Oberflächen hergestellt werden, so dass umfangreiche Nachbearbeitungsschritte wie Polieren oft überflüssig sind. Außerdem können während des Spritzgießens verschiedene Farbstoffe und Texturen eingearbeitet werden. | Dies trägt zur optischen Attraktivität und Funktionalität des Endprodukts bei. Glatte Oberflächen können für die Hygiene bei medizinischen Geräten oder für die leichte Reinigung bei Konsumgütern wichtig sein. | |
Materialeffizienz: Das Spritzgießen ermöglicht eine endkonturnahe Fertigung und minimiert den Materialabfall im Vergleich zu subtraktiven Verfahren wie der spanenden Bearbeitung. Überschüssiges Material, Anguss und Angusskanäle genannt, kann oft recycelt und in späteren Produktionsläufen wiederverwendet werden. | Dies ist unter dem Gesichtspunkt der Kosten und der Nachhaltigkeit von Vorteil. Die Minimierung des Abfalls verringert auch die Umweltauswirkungen des Herstellungsprozesses. | |
Automatisierungspotenzial: Der Spritzgießprozess kann in hohem Maße automatisiert werden, wobei nur ein minimaler menschlicher Eingriff erforderlich ist. Dies ermöglicht eine gleichbleibende Produktionsqualität und senkt die Arbeitskosten. | Die Automatisierung ist besonders vorteilhaft für die Produktion hoher Stückzahlen und gewährleistet eine gleichbleibende Produktqualität unabhängig von der Qualifikation des Bedieners. |
Beschränkungen des Herstellungsprozesses
Es gibt aber auch einige Einschränkungen:
- Teilegewicht begrenzt auf < 400 g
- Wandstärke > 0,4 mm
- Für komplexe Geometrien benötigte Baugruppen
- Teurer Werkzeugbau für Formen
- Dimensionsänderungen während des Sinterns
Globale Lieferanten von Ausgangsmaterial
Viele internationale Unternehmen liefern fertiges Ausgangsmaterial für das Spritzgießen:
Unternehmen | Standort | Materialien |
---|---|---|
BASF | Deutschland | Edelstahl 316L, Titan-Legierungen |
Sandvik | Schweden | Nichtrostende Stähle, Werkzeugstähle |
GKN | UK | Aluminium- und Magnesium-Legierungen |
Rio Tinto | Australien | Spritzgussmassen aus Metall und Keramik |
Vorläufige Preisgestaltung
Material | Preisspanne |
---|---|
Rostfreier Stahl | $50-70 pro kg |
Werkzeugstahl | $45-65 pro kg |
Wolfram Schwere Legierung | $130-170 pro kg |
Die Preisgestaltung hängt vom Auftragsvolumen, dem Bedarf an individuellen Anpassungen und wirtschaftlichen Faktoren ab.
Vor- und Nachteile der Verwendung Spritzgießbare Pulver
Vorteile | Benachteiligungen |
---|---|
Verschlungene und komplexe Formen | Begrenzte Größe und Gewicht |
Engere Toleranzen | Teure Werkzeuge und Ausrüstung |
Feines Oberflächenfinish | Dimensionsänderungen während des Sinterns |
Auswahl an Materialien | Nachbearbeitung oft erforderlich |
Hohe Produktion, niedrige Kosten pro Teil | Spröde Materialien neigen zur Rissbildung |
Weniger Abfall | Schränkt die Materialauswahl ein |
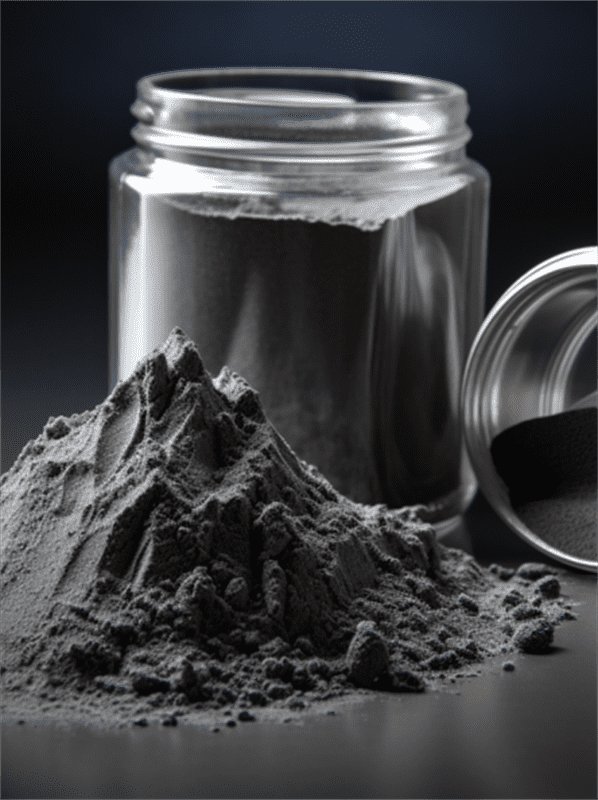
FAQ
F: Wie ist die typische Zusammensetzung von spritzgießbaren Pulvern?
A: Sie enthalten 80-90% Metallpulver, 8-20% Bindemittel und 1-2% Schmiermittel nach Gewicht. Übliche Bindemittel sind Wachs, PP, PE und PEG.
F: Welcher Größenbereich von Pulvern wird verwendet?
A: Es werden Pulver zwischen 1-20 Mikron verwendet. Feineres Pulver verbessert die Dichte, kann aber zur Agglomeration neigen.
F: Wie stark ist die Schrumpfung während des Sinterns?
A: Bis zu 20% tritt beim Sintern in der Flüssigphase eine lineare Schrumpfung der Teile auf. Bei der Werkzeugkonstruktion müssen entsprechende Vorkehrungen getroffen werden.
F: Was verursacht Risse in Spritzgussteilen aus Sintermetall?
A: Ungleichmäßige Erwärmung in den Öfen, schnelle Abkühlung nach dem Sintern, schlechte Pulvermischung und Auswahl spröder Legierungen.
F: Welche Materialoptionen gibt es für spritzgussfähige Pulver?
A: Rostfreie Stähle, Werkzeugstähle, schwere Wolframlegierungen, Kupferlegierungen, Titan und Titanlegierungen und andere.