Helium plasma, a state of matter often referred to as the fourth state (alongside solid, liquid, and gas), might sound like something straight out of science fiction. But believe it or not, it has a surprising number of real-world applications, from medical procedures to advanced manufacturing.
This article will be your one-stop shop for understanding helium plasma. We’ll delve into its essence, explore its unique properties, and uncover the exciting ways it’s being used to shape our world. So, buckle up and get ready for a fascinating journey into the heart of this energetic realm!
Prozess Prinzip der Helium Plasma
Imagine a gas, like helium, being pumped with so much energy that its atoms become ionized – stripped of their electrons. This energetic soup of charged particles and free electrons is what we call plasma. In the case of helium plasma, the energy comes from an electric current passed through the helium gas.
Think of it like this: normally, helium atoms are like happy little couples, holding hands (electrons) tightly. But when we introduce an electric current, it’s like a wild party – the electrons get ripped away, leaving the helium atoms all charged up and jittery. This creates a highly conductive and reactive environment.
Process Characteristics of Helium Plasma
Helium plasma boasts some pretty impressive characteristics:
- High Temperature: The energetic nature of plasma translates to scorching temperatures, often reaching tens of thousands of degrees Celsius. That’s hot enough to melt even the most stubborn metals!
- Elektrische Leitfähigkeit: With all those charged particles buzzing around, helium plasma conducts electricity exceptionally well. It’s like a superhighway for electrons.
- Chemische Reaktivität: The free electrons and ions in plasma make it highly reactive. It can break down complex molecules and even initiate new chemical reactions.
- Unique Flow Properties: Due to its charged nature, helium plasma can be manipulated using magnetic fields. This allows for precise control over its movement and direction.
These characteristics make helium plasma a powerful tool with a wide range of potential applications.
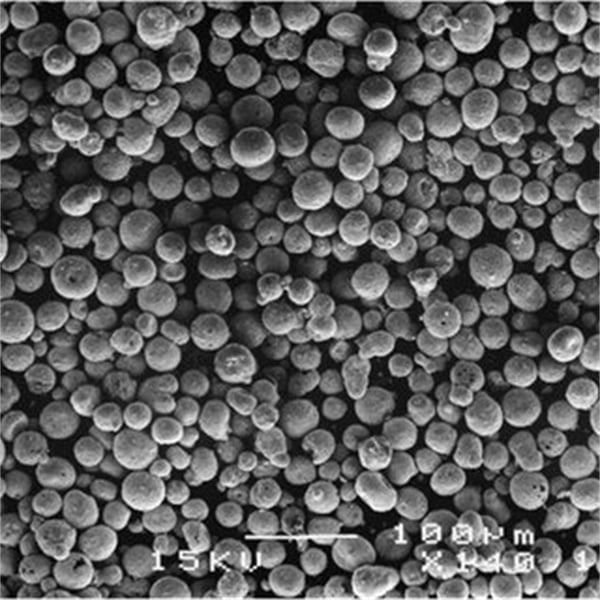
Application Areas of Helium Plasma
Helium plasma isn’t just some laboratory curiosity. It’s finding its way into various fields, including:
- Metal Additive Manufacturing: Helium plasma can be used in a process called Gerichtete Energieabscheidung (DED) for 3D printing metals. Here, the plasma stream melts metal powder, depositing it layer by layer to create complex 3D structures. This technology offers significant advantages over traditional methods, such as faster printing speeds, higher material strength, and the ability to print with a wider variety of metals.
- Metal Surface Treatment: Helium plasma can be used to clean, activate, and modify the surface of metals. This is particularly useful for processes like welding and brazing, where a clean and reactive surface is essential for strong bonds. Additionally, plasma treatment can improve the adhesion properties of coatings and paints applied to metal surfaces.
- Waste Treatment: Helium plasma can be a powerful tool for breaking down hazardous materials like organic pollutants and toxic gases. The high temperatures and reactive nature of plasma can effectively decompose these materials into harmless byproducts.
- Semiconductor Manufacturing: In the ever-shrinking world of microchips, helium plasma plays a crucial role in etching and cleaning the intricate patterns on silicon wafers. The precise control offered by plasma allows for the creation of highly miniaturized features essential for modern electronics.
- Medizinische Anwendungen: Helium plasma is being explored for various medical procedures, including minimally invasive surgery and wound healing. The high temperatures and reactivity of plasma can be used for precise cutting and tissue ablation (removal), while also promoting faster healing.
These are just a few examples, and as research progresses, we can expect to see even more innovative applications for helium plasma emerge.
Metal Powders for Directed Energy Deposition with Helium Plasma
When it comes to DED with helium plasma, the metal powder used plays a critical role in the final product’s properties. Here’s a closer look at some popular metal powder options:
Metallpulver | Beschreibung | Vorteile | Beschränkungen |
---|---|---|---|
Rostfreier Stahl 316L | Ein vielseitiger austenitischer rostfreier Stahl, der für seine hervorragende Korrosionsbeständigkeit bekannt ist. | Widely used, good mechanical properties, resists a variety of corrosive environments. | Can be more expensive compared to some other options. |
Inconel 625 | A high-performance nickel-chromium superalloy offering exceptional strength and high-temperature resistance. | Ideal for demanding applications requiring strength and heat tolerance in harsh environments. | More expensive than stainless steel, can be difficult to machine. |
Titan 6Al-4V | A lightweight and strong titanium alloy commonly used in aerospace and medical applications. | Excellent strength-to-weight ratio, good biocompatibility. | Can be susceptible to oxidation |
Aluminium Si7Mg0.3 | A high-strength aluminum alloy containing silicon and magnesium for improved casting properties. | Offers a good balance of strength and weight, often used in automotive and aerospace applications. | More prone to corrosion compared to pure aluminum. |
Kupfer | Pure copper powder used for applications requiring high electrical conductivity and thermal conductivity. | Excellent heat and electricity conductor, readily available. | Susceptible to oxidation, requires careful handling to prevent surface contamination. |
Nickel | Pure nickel powder for applications requiring high corrosion resistance and good mechanical properties. | Ductile and formable, resists a variety of corrosive environments. | Can be more expensive compared to some other options. |
Hastelloy C-276 | A nickel-chromium-molybdenum superalloy known for its exceptional corrosion resistance in harsh chemical environments. | Ideal for chemical processing equipment and applications exposed to aggressive chemicals. | Very expensive compared to other metal powders. |
Kobalt-Chrom (CoCr) | A biocompatible cobalt-chromium alloy commonly used for medical implants and prosthetics. | Excellent wear resistance, good biocompatibility for long-term implantation. | Can be brittle, requires careful process control during DED. |
Werkzeugstahl (H13) | A high-alloy tool steel known for its excellent wear resistance and hot hardness. | Ideal for creating wear-resistant tools and molds through DED. | Difficult to machine after printing, requires post-processing for final shape. |
Wolfram | Pure tungsten powder offering the highest melting point of all common metals. | Ideal for applications requiring extreme high-temperature resistance, such as rocket engine components. | Brittle and difficult to process, requires specialized DED techniques. |
Die Wahl des richtigen Metallpulvers
Selecting the right metal powder for your DED application depends on several factors:
Faktor | Beschreibung | Impact on Choice |
---|---|---|
Gewünschte Eigenschaften | This refers to the key characteristics you need in the final 3D-printed part. Common considerations include: * Stärke: How much force can the part withstand before breaking? * Korrosionsbeständigkeit: How well will the part resist rust and degradation in its operating environment? * Gewicht: Is a lightweight component crucial for the application (e.g., aerospace)? * Leistung bei hohen Temperaturen: Does the part need to withstand extreme heat? * Biokompatibilität: Is the part intended for medical implants requiring compatibility with the human body? | Selecting a metal powder with properties that align with your desired outcome is critical. For instance, if strength is paramount, stainless steel 316L or Inconel 625 might be excellent choices due to their robust mechanical properties. Conversely, if weight is a major concern, aluminum Si7Mg0.3 or even pure titanium powder could be better suited for their lightweight nature. |
Anforderungen an die Bewerbung | The specific use case for the 3D-printed part will dictate the necessary properties. Here are some examples: * Luft- und Raumfahrt: Parts for airplanes or spacecraft often require a combination of high strength, light weight, and good corrosion resistance. * Medizinische Implantate: Biocompatibility and corrosion resistance are essential for implants that will reside inside the body. * Ausrüstung für die chemische Verarbeitung: Resistance to harsh chemicals is crucial for equipment used in chemical plants. * Wärmetauscher: High thermal conductivity is a key factor for efficient heat transfer. | Understanding the application’s demands helps narrow down the suitable metal powder options. For example, an aircraft component might benefit from aluminum Si7Mg0.3 due to its strength-to-weight ratio, while a medical implant would prioritize the biocompatible nature of CoCr powder. |
Kostenüberlegungen | Metal powders can vary significantly in price. Here’s a breakdown: * High-Cost Powders: * Inconel 625 * Hastelloy C-276 * Mid-Range Powders: * Stainless Steel 316L * Nickel * Titanium 6Al-4V * Lower-Cost Powders: * Aluminum Si7Mg0.3 * Copper | Striking a balance between cost and performance is essential. While high-performance alloys like Inconel 625 offer exceptional properties, their cost might be prohibitive for certain applications. Conversely, readily available and affordable options like aluminum Si7Mg0.3 might be suitable for less demanding uses. |
Verarbeitbarkeit | Not all metal powders behave the same way during DED. Some factors to consider include: * Fließfähigkeit des Pulvers: The powder needs to flow freely for proper feeding into the DED system. * Laser Absorption: The powder’s ability to absorb the laser energy efficiently is crucial for melting and bonding the particles. * Moisture Sensitivity: Some powders are more susceptible to moisture than others, which can affect their flowability and printability. | Choosing a metal powder that is compatible with DED is essential. For instance, aluminum powders tend to be more challenging to process due to their high reflectivity compared to steel powders. Consulting with DED equipment manufacturers or metal powder suppliers regarding their processability recommendations is vital. |
Beyond the Basics: Emerging Metal Powders
The world of DED metal powders is constantly evolving. Here are some exciting trends to keep an eye on:
Emerging Metal Powder Trend | Beschreibung | Potential Benefits | Überlegungen |
---|---|---|---|
Multi-Material Powders | These innovative powders combine multiple metals or even metal-ceramic blends within a single particle. Imagine a powder consisting of tiny spheres, where the core is a strong metal like nickel and the shell is a wear-resistant ceramic like zirconium oxide. | Multi-material powders offer the exciting possibility of creating parts with graded properties within a single print. For instance, a tool could have a core of high-strength steel for durability and an outer layer of wear-resistant ceramic for extended cutting life. This eliminates the need for complex post-processing steps like joining dissimilar materials. | Developing and controlling the properties of these intricate powders can be challenging. Ensuring proper mixing of the constituent materials and achieving uniform distribution within the particle is crucial. Additionally, the DED process itself might need adjustments to optimize melting and bonding of these multi-material powders. |
Nanopowders | These powders take the concept of fine particles to a whole new level. Nanopowders consist of metal particles with dimensions in the nanometer range (billionths of a meter). | Nanoparticles offer the potential for creating 3D-printed parts with exceptional properties. Due to their extremely small size, nanopowders can enable the production of features with unmatched detail and resolution. Additionally, the large surface area of nanoparticles can enhance certain material properties, like strength and electrical conductivity. | Working with nanopowders can be trickier compared to conventional DED powders. The small size and high surface area of nanoparticles can make them more prone to agglomeration (clumping) which can hinder flowability and printability. Specialized handling techniques and DED equipment with advanced powder feeding mechanisms might be necessary. |
Recycelte Pulver | Sustainability is a growing concern in the manufacturing industry, and DED is no exception. Recycled metal powders are gaining traction as a way to reduce environmental impact. | The concept is simple: take scrap metal or used metal powder from other processes and reprocess it into a usable DED powder feedstock. This reduces reliance on virgin metal resources and minimizes waste generation. | Recycled powders might require additional processing steps to ensure consistent quality and meet the stringent requirements for DED. Strict quality control measures are necessary to eliminate any contaminants or impurities that could affect the final part’s properties. Additionally, the cost-effectiveness of powder recycling needs to be carefully evaluated as reprocessing can add complexity to the overall production chain. |
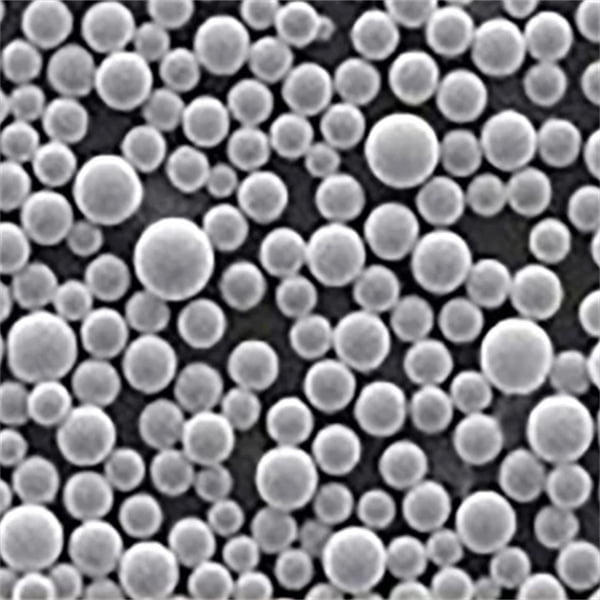
Vor- und Nachteile von Helium Plasma DED
Vorteile:
- Schnellere Druckgeschwindigkeiten: Compared to traditional methods like laser sintering, DED with helium plasma offers significantly faster printing speeds. This can translate to reduced production times and costs.
- Higher Material Strength: The high temperatures achieved by helium plasma can lead to better bonding between metal particles, resulting in stronger and more durable final parts.
- Größere Materialkompatibilität: DED with helium plasma can work with a broader range of metals compared to other additive manufacturing techniques. This opens up possibilities for using exotic materials with unique properties.
- Near-Net-Shape Manufacturing: DED allows for the creation of parts with near-final shapes, minimizing the need for extensive post-processing.
Benachteiligungen:
- Hoher Energieverbrauch: The process requires a significant amount of energy to maintain the high temperatures of the helium plasma.
- Oberflächenrauhigkeit: Due to the nature of the process, DED parts can have a rougher surface finish compared to other techniques. This may require additional post-processing steps.
- Begrenzte Auflösung: While improving, the resolution of DED features is generally not as fine as what can be achieved with techniques like stereolithography (SLA).
- Health and Safety Concerns: Working with high-temperature plasma and metal powders requires careful handling and appropriate safety equipment to minimize risks of burns, inhalation of fumes, and fire hazards.
FAQ
What is the difference between helium plasma and other types of plasma?
There are many types of plasma, each with its characteristics depending on the gas used and the way it’s ionized. Helium plasma is known for:
- High Electron Temperatures: Compared to other commonly used plasmas like argon, helium plasma features a higher electron temperature. This translates to a more energetic environment with unique properties.
- Lower Electron Density: Helium plasma typically has a lower electron density compared to some other plasmas. This can influence factors like electrical conductivity and reactivity.
Is helium plasma safe?
Helium plasma itself isn’t inherently dangerous. However, the high temperatures and energetic nature of the process require proper safety precautions. Here are some key points to remember:
- Hohe Temperaturen: The plasma stream and surrounding equipment can reach extremely high temperatures, posing a risk of burns.
- Electrical Hazards: Working with plasma involves electricity, so proper grounding and safety protocols are essential to prevent electrical shock.
- Metal Fumes: The process can generate metal fumes, which can be harmful if inhaled. Proper ventilation and respiratory protection are crucial.
- Ultraviolet (UV) Radiation: Plasma can emit UV radiation, which can damage eyes and skin. Protective eyewear and clothing are necessary.
Following recommended safety protocols and using appropriate personal protective equipment (PPE) minimizes risks when working with helium plasma.
What are the future prospects for helium plasma applications?
The future of helium plasma is bright! Here are some exciting possibilities:
- Advancements in DED: Research continues to improve DED technology using helium plasma. This could lead to faster printing speeds, even finer features, and the ability to work with an even wider range of materials.
- Plasma Medicine: The potential applications of helium plasma in medical treatments are being actively explored. This could lead to new minimally invasive surgical techniques and improved wound healing processes.
- Erforschung des Weltraums: Helium plasma shows promise for applications in space propulsion and even in the development of miniature fusion reactors for future space missions.
- Environmental Remediation: The ability of helium plasma to break down pollutants could be harnessed for more efficient and environmentally friendly waste treatment solutions.