Beim 3D-Druck, auch bekannt als additive Fertigung (AM), werden spezielle Pulver verwendet, um dreidimensionale Komponenten in aufeinanderfolgenden Schichten herzustellen. Dieser Leitfaden dient als ausführliche Referenz zu Pulvern für den 3D-Druck - er untersucht Typen, Eigenschaften, Spezifikationen, Herstellungsverfahren, wichtige Lieferanten und Preise, Anwendungen in verschiedenen Branchen, Vergleiche mit Alternativen, FAQs und mehr.
Überblick über 3D-Druck-Pulver
3D-Druckpulver sind Rohmaterialien, die die additive Herstellung von Teilen aus Kunststoff, Metall und Keramik ermöglichen. Wichtigste Merkmale:
- Zustand: Ultrafeine partikelförmige Pulver
- Größenbereich: In der Regel 10-150 Mikrometer
- Morphologie: Meist kugelförmige Partikelform
- Zusammensetzung: Polymer, Metalllegierung, Keramik, Sandsteinmischungen
- Wichtige Eigenschaften: Entwickelte Partikelgrößenverteilung, Fließfähigkeit, Packungsdichte und Mikrostruktur
Durch die genaue Steuerung der physikalischen Eigenschaften des Pulvers und der Wechselwirkungen mit thermischen/kinetischen Druckverfahren ermöglichen 3D-Druckpulver komplizierte Teilegeometrien und Materialzusammensetzungsgradienten, die auf andere Weise nicht zu erreichen sind.
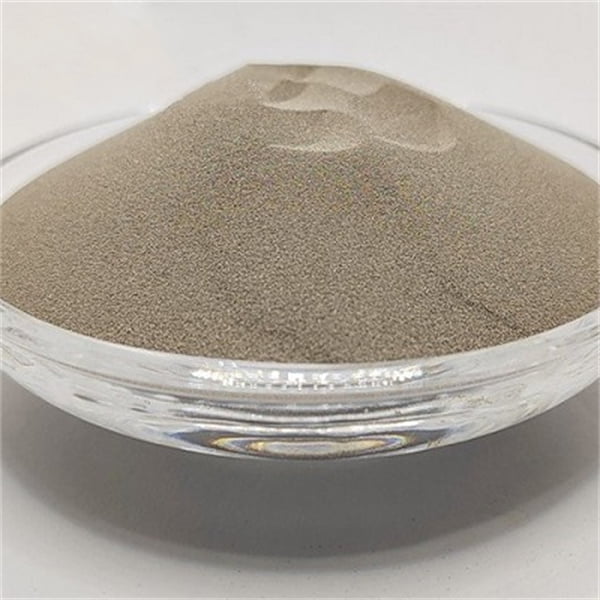
Arten von 3D-Druckpulvern
Kategorie | Materialien | Druckverfahren |
---|---|---|
Kunststoffe | Nylons, ABS, TPU, PEKK, PEEK... | Selektives Laser-Sintern (SLS) |
Metalle | Rostfreie Stähle, Werkzeugstähle, Titan und Legierungen, Superlegierungen... | Direktes Metall-Laser-Sintern (DMLS) |
Keramik | Aluminiumoxid, Zirkoniumdioxid, Siliziumkarbid | Binder Jetting, Fused Deposition Modeling |
Verbundwerkstoffe | Metall/Kunststoff-Mischungen, Sandsteinmischungen | Multi Jet Fusion (MJF), gebundene Metallabscheidung |
Biokompatibel | PEEK, PLGA, TCP... | Selektives Laserschmelzen (SLM) |
Tabelle 1: Wichtige Kategorien, Materialien und zugehörige Druckplattformen für kommerzielle 3D-Druckpulver
Polymer-, Metall-, Keramik- und Verbundwerkstoffpulver unterstützen die Produktion von Endverbrauchsteilen in der Luft- und Raumfahrt, im Automobilbau, in der Medizin, der Zahnmedizin und der Industrie.
Herstellungsmethoden
Methode | Beschreibung | Materialeignung | Vorteile | Benachteiligungen |
---|---|---|---|---|
Zerstäubung | Dieser Oberbegriff umfasst verschiedene Techniken, mit denen geschmolzenes Metall in feine Partikel zerlegt wird. Das geschmolzene Metall wird durch eine Düse in einen Hochdruck-Gas- oder Wasserstrom gepresst, wodurch die Tröpfchen schnell zu kugelförmigen Partikeln erstarren. | Metalle (Eisen, Aluminium, Titanlegierungen) | - Hohe Produktionsrate - Konstante Partikelgröße und -form - Gute Fließfähigkeit des Pulvers | - Erfordert hohen Energieeinsatz - Potenzielle Oxidbildung auf den Partikeln - Begrenzt auf bestimmte Materialien |
Gaszerstäubung | Die gängigste Zerstäubungsmethode, bei der ein Inertgas (in der Regel Stickstoff) verwendet wird, um das geschmolzene Metall aufzubrechen. | Ähnlich wie die Zerstäubung, aber im Allgemeinen bessere Oberflächenqualität und genauere Kontrolle der Partikelgröße. | - Überlegene Pulverqualität im Vergleich zu anderen Zerstäubungsmethoden - Geeignet für reaktive Metalle | Ähnlich wie bei der Zerstäubung, aber höhere Gerätekosten |
Wasserzerstäubung | Verwendet einen Hochdruckwasserstrahl, um das geschmolzene Metall zu fragmentieren. Kostengünstiger als Gaszerstäubung, erzeugt aber weniger kugelförmige Partikel. | Einige Metalle (Eisen, Kupfer) und einige Polymere | - Geringere Kosten als Gaszerstäubung - Gut geeignet für feuchtigkeitsunempfindliche Materialien | - Geringere Pulverqualität (unregelmäßige Formen) - möglicherweise nicht ideal für Hochleistungsanwendungen |
Plasma-Zerstäubung | Ein elektrischer Lichtbogen erhitzt das Ausgangsmaterial (Metalldraht oder -pulver) bis zum Schmelzzustand. Das geschmolzene Metall wird dann durch eine Düse ausgestoßen und mit einem Plasmabrenner zerstäubt. | Breite Palette von Materialien (Metalle, Legierungen, Keramik) | - Kann Materialien mit hohem Schmelzpunkt verarbeiten - Geeignet für die Herstellung von Verbundpulvern | - Komplexer und kostenintensiver Prozess - Erfordert strenge Sicherheitsmaßnahmen |
Mechanische Pulverisierung | Ein physikalisches Verfahren, bei dem Schüttgut zu feinem Pulver gemahlen oder gemahlen wird. | Spröde Materialien (Keramik, einige Polymere) | - Einfachere und kostengünstigere Einrichtung im Vergleich zu anderen Methoden | - Begrenzte Kontrolle über Partikelgröße und -morphologie - Kann beim Mahlen Verunreinigungen einbringen |
Chemische Gasphasenabscheidung (CVD) | Ein chemischer Prozess, bei dem gasförmige Vorläufer reagieren, um eine feste Ablagerung auf einem Keimpartikel zu bilden. | Metalle, Keramik und einige hochentwickelte Materialien | - Hohe Reinheit und präzise Kontrolle über die Partikelzusammensetzung - Kann komplexe Geometrien erzeugen | - Langsamer Prozess mit begrenzter Produktionsrate - Hohe Kapitalinvestitionen |
Elektrolytische Zerstäubung | In einer Elektrolysezelle wird eine Metallanode in Ionen zerlegt. Die Ionen verbinden sich dann mit den Elektronen an der Kathode und bilden Metallteilchen. | Metalle | - Umweltfreundliches Verfahren (vermeidet hohe Temperaturen) - Geeignet für feuchtigkeitsempfindliche Materialien | - Geringere Produktionsrate als bei Zerstäubungsmethoden - Beschränkung auf bestimmte Elektrolyte und Anodenmaterialien |
Sphäroisierung | Ein zusätzliches Verfahren zur Verbesserung der Form von unregelmäßig geformten Pulvern, die mit anderen Methoden hergestellt wurden. Beinhaltet eine Wärmebehandlung oder chemische Prozesse, um die Agglomeration der Partikel zu Kugeln zu fördern. | Die meisten Pulverarten (Metalle, Polymere, Keramiken) | - Verbessert die Fließfähigkeit und Packungsdichte des Pulvers - Verbessert die Druckfähigkeit | - Fügt einen zusätzlichen Verarbeitungsschritt hinzu - ist möglicherweise nicht für alle Anwendungen erforderlich |
Eigentum von 3D-Druck-Pulver
Eigentum | Beschreibung | Bedeutung für den 3D-Druck | Beispiele und Überlegungen |
---|---|---|---|
Partikelgröße und -verteilung | Bezieht sich auf die Größenvariationen der einzelnen Pulverpartikel und die Gesamtverteilung über verschiedene Größenbereiche. Gemessen in Mikrometern (µm). | Spielt eine entscheidende Rolle für die Druckbarkeit, die Auflösung und die Dichte des fertigen Teils. – Zu groß: Beeinträchtigung der Fließfähigkeit, ungleichmäßiges Verteilen und die Gefahr von Rechendefekten. – Zu klein: Eine vergrößerte Oberfläche kann zu Anbackungen und schlechter Packung führen, was die Festigkeit beeinträchtigt. |
– SLS (Selektives Laser-Sintern): Bevorzugt im Allgemeinen feinere Pulver (20-80 µm) für detaillierte Merkmale. – MJF (Multi Jet Fusion): Etwas größere Partikel (50-100 µm) können aufgrund der Fähigkeit der Inkjet-Technologie, Fließgrenzen zu überwinden, verwendet werden. – Metall-Pulver: Eine enge Verteilung (enger Bereich) ist ideal für eine gute Packungsdichte und minimale Porosität im fertigen Teil. |
Morphologie der Partikel | Die Form der einzelnen Pulverpartikel. | Beeinflusst den Zusammenhalt der Partikel, die Fließfähigkeit und die Oberflächenbeschaffenheit des Endprodukts. - Sphärisch: Bieten die beste Packungsdichte und Fließfähigkeit, was zu starken und gleichmäßigen Teilen führt. - Unregelmäßige Formen: Es können Lücken und Unregelmäßigkeiten entstehen, die die Festigkeit und Oberflächenqualität beeinträchtigen können. | – Kunststoff-Pulver: Im Allgemeinen kugelförmig oder nahezu kugelförmig für optimale Bedruckbarkeit. - Metall-Pulver: Kann je nach Metall und Herstellungsverfahren variieren. Sphärische Morphologien werden bevorzugt, können aber auch durch Nachbearbeitungstechniken wie Zerstäubung erreicht werden. |
Fließfähigkeit | Die Leichtigkeit, mit der Pulver unter seinem eigenen Gewicht oder mit minimaler Scherkraft fließt. | Entscheidend für einen gleichmäßigen Materialauftrag und eine gleichmäßige Schichtbildung beim Druck. - Gute Fließfähigkeit: Sorgt für ein gleichmäßiges Verteilen und minimiert das Risiko von Schichtfehlern. - Schlechte Fließfähigkeit: Kann zu ungleichmäßiger Ablagerung, Inkonsistenzen und möglichen Druckproblemen führen. | – Pulver mit enger Korngrößenverteilung neigen dazu, besser zu fließen, da die Partikelgröße weniger stört. - Zusatzstoffe und Oberflächenbehandlungen kann zur Verbesserung der Fließfähigkeit verwendet werden, indem die Reibung zwischen den Partikeln verringert wird. |
Packungsdichte | Das Maß dafür, wie dicht die Pulverpartikel zusammengepackt werden können. Ausgedrückt als Prozentsatz des vom Pulver eingenommenen Gesamtvolumens. | Beeinflusst die endgültige Dichte, Festigkeit und Maßhaltigkeit des gedruckten Teils. - Hohe Packungsdichte: Führt zu dichteren Teilen mit besseren mechanischen Eigenschaften und höherer Maßgenauigkeit. - Geringe Packungsdichte: Das Ergebnis sind Teile mit höherer Porosität, die möglicherweise schwächer und weniger maßhaltig sind. | – Partikelform spielt eine wichtige Rolle. Kugelförmige Partikel lassen sich besser verpacken als unregelmäßige Formen. - Verfahren wie Binder Jetting können von etwas geringeren Packungsdichten profitieren, um eine gute Infiltration des Bindemittels zu ermöglichen. |
Sinterbarkeit | Die Fähigkeit von Pulverpartikeln, während des 3D-Druckverfahrens miteinander zu verschmelzen oder sich zu verbinden, in der Regel durch Wärme oder Laserenergie. | Unverzichtbar für die Herstellung starker und funktioneller gedruckter Teile. - Gute Sinterfähigkeit: Ermöglicht eine starke Bindung zwischen den Partikeln, was zu robusten und funktionellen Teilen führt. - Schlechte Sinterfähigkeit: Kann zu schwachen Verbindungen und einem möglichen Versagen der Teile unter Belastung führen. | – Zusammensetzung des Materials: Metalle sind im Allgemeinen gut sinterbar, da sie bei hohen Temperaturen starke Bindungen eingehen können. - Polymer-Pulver erfordern oft spezielle Zusatzstoffe oder Nachbearbeitungsschritte (z. B. Sinteröfen), um die Bindung zu verbessern. |
Chemische Zusammensetzung | Die elementare Zusammensetzung des Pulvermaterials. | Bestimmt die endgültigen Eigenschaften des gedruckten Teils, wie Festigkeit, Hitzebeständigkeit und Biokompatibilität. - Auswahl des Materials auf der Grundlage der gewünschten Anwendung und der funktionalen Anforderungen entscheidend ist. - Pulver können gemischt werden um bestimmte Eigenschaften zu erzielen (z. B. Kombination von Metallen zur Verbesserung des Verhältnisses von Festigkeit zu Gewicht). | – Metall-Pulver können von reinen Metallen wie Titan bis zu komplexen Legierungen mit maßgeschneiderten Eigenschaften reichen. - Polymer-Pulver können Nylons, Polyamide und biokompatible Materialien für medizinische Anwendungen umfassen. |
Thermische Eigenschaften | Das Verhalten des Pulvermaterials bei unterschiedlichen Temperaturen, einschließlich Schmelzpunkt, Wärmeleitfähigkeit und Wärmeausdehnungskoeffizient. | Einflussfaktoren wie Maßhaltigkeit, Verformung und Wärmeverzug während des Drucks und der Nachbearbeitung. - Kontrollierte Heizung ist unerlässlich, um zu vermeiden, dass die thermischen Grenzen des Materials überschritten werden und Defekte an den Teilen entstehen. - Abstimmung der thermischen Eigenschaften von Pulver und Bauplattform minimiert den Verzug und gewährleistet die Maßhaltigkeit. | – Metall-Pulver haben oft hohe Schmelzpunkte und erfordern eine präzise Temperaturkontrolle bei laserbasierten Verfahren wie SLM (Selective Laser Melting). - Polymer-Pulver können bei niedrigeren Temperaturen erweichen oder schmelzen, |
3D-Druck-Pulver Spezifikationen
Eigentum | Beschreibung | Auswirkungen auf Druckbarkeit und Teilequalität | Materielle Beispiele |
---|---|---|---|
Partikelgröße und -verteilung | Bezieht sich auf die einzelnen Partikeldurchmesser und die Schwankungen innerhalb des Pulvers. Gemessen in Mikron (µm). | Feine Pulver ( 100 µm) verbessern die Fließfähigkeit, können aber die Detailgenauigkeit einschränken und die Oberflächenrauhigkeit erhöhen. Eine enge Größenverteilung gewährleistet ein gleichmäßiges Packungs- und Druckverhalten. | Polymere: Nylon (15-75 µm), Polypropylen (40-100 µm) |
Morphologie der Partikel | Die Form der einzelnen Pulverpartikel. | Sphärische Partikel fließen frei und packen effizient, was zu einer guten Druckbarkeit führt. Unregelmäßige Formen können die Bindung zwischen den Partikeln verbessern, können aber Fließprobleme verursachen und erfordern spezielle Drucktechniken. | Polymere: Aufgrund des Herstellungsverfahrens typischerweise kugelförmig. |
Scheinbare Dichte & Packungsdichte | Die Schüttdichte ist das Gewicht des Pulvers pro Volumeneinheit in seinem losen, geschütteten Zustand. Die Packungsdichte ist die maximale Dichte, die nach dem Klopfen oder der Vibration erreicht wird. | Die scheinbare Dichte beeinflusst den Pulverfluss und die Handhabung. Die Packungsdichte beeinflusst die endgültige Dichte des gedruckten Teils und seine mechanischen Eigenschaften. Eine höhere Packungsdichte führt im Allgemeinen zu festeren Teilen. | Polymere: Schüttdichte (0,3-0,8 g/cm³), Packungsdichte (0,5-0,9 g/cm³) |
Fließfähigkeit | Die Leichtigkeit, mit der Pulver unter Schwerkraft oder mit minimaler Bewegung fließt. | Eine gute Fließfähigkeit ist entscheidend für eine gleichmäßige Verteilung des Pulvers beim Druck. Eine schlechte Fließfähigkeit kann zu Unregelmäßigkeiten in den Schichten und Druckfehlern führen. | Polymere: Aufgrund ihrer kugelförmigen Morphologie in der Regel frei fließend. Zur Verbesserung der Fließfähigkeit können Zusatzstoffe verwendet werden. |
Feuchtigkeitsgehalt | Die Menge des in den Pulverpartikeln eingeschlossenen Wasserdampfs. | Überschüssige Feuchtigkeit kann beim Drucken zu Problemen führen, z. B. zu Dampfexplosionen oder uneinheitlichem Schmelzverhalten. Bei den meisten Pulvern ist eine strenge Feuchtigkeitskontrolle erforderlich. | Polymere: In der Regel sehr niedriger Feuchtigkeitsgehalt (< 0,1 wt%), um Hydrolyse zu verhindern und ein gleichmäßiges Druckverhalten zu gewährleisten. |
Chemische Zusammensetzung & Reinheit | Die elementare Zusammensetzung des Pulvers und das Vorhandensein von Verunreinigungen. | Die chemische Zusammensetzung bestimmt die endgültigen Eigenschaften des gedruckten Teils. Verunreinigungen können die Druckbarkeit, die mechanische Leistung und die Oberflächenqualität beeinträchtigen. | Polymere: Es wird hochreines Material verwendet, um gleichbleibende Eigenschaften und Druckfähigkeit zu gewährleisten. |
Thermische Eigenschaften | Schmelzpunkt, Glasübergangstemperatur (Tg) für Polymere und Wärmeleitfähigkeit. | Die thermischen Eigenschaften beeinflussen die Druckprozessparameter und die endgültige Mikrostruktur des gedruckten Teils. | Polymere: Schmelzpunkt und Tg sind entscheidend für die Einstellung von Druckparametern wie Laserleistung oder Betttemperatur. |
3D-Druck-Pulver-Lieferanten
Material | Wichtige Anwendungen | Repräsentative Lieferanten | Überlegungen |
---|---|---|---|
Polymer-Pulver | - Prototyping - Funktionsteile - Medizinische Geräte - Konsumgüter | * Polyamid (Nylon): BASF, Evonik, Arkema * Polymilchsäure (PLA): NatureWorks, ExxonMobil Chemical, DuPont * Polypropylen (PP): Royal DSM, SABIC, Repsol |
* Partikelgröße und -verteilung wirken sich auf die Druckbarkeit und die endgültigen Teileigenschaften aus. * Materialeigenschaften wie Hitzebeständigkeit, Flexibilität und Biokompatibilität variieren. * Berücksichtigen Sie die chemische Verträglichkeit mit Nachbearbeitungstechniken. |
Metall-Pulver | - Komponenten für die Luft- und Raumfahrt - Automobilteile - Medizinische Implantate - Werkzeuge und Formen | * Titan-Legierungen: AP Powder Company, Höganäs, GE Additive * Rostfreier Stahl: Schreiner Additive Fertigung, SLM-Lösungen, EOS GmbH * Aluminium-Legierungen: Rio Tinto Alcan, DLP Manufacturing, Exone |
* Die Morphologie (Form) des Pulvers beeinflusst die Fließfähigkeit und die Packungsdichte. * Die Korngröße beeinflusst die mechanischen Eigenschaften des Endprodukts. * Beim Umgang mit reaktiven Metallpulvern sind Sicherheitsprotokolle von entscheidender Bedeutung. |
Verbundwerkstoff-Pulver | - Leichte Strukturen mit hoher Festigkeit - Leitfähige Komponenten - Biokompatible Implantate mit verbesserten Eigenschaften | * Polymer-Metall-Verbundwerkstoffe: LPW Technology, Markforged, Desktop Metal * Keramik-Metall-Verbundwerkstoffe: Sandvik Hyperion, Extrude Hone, Plasma Technik * Polymer-Kohlenstofffaser-Verbundwerkstoffe: Stratasys, Desktop Metal, Henkel |
* Die Auswahl hängt von der gewünschten Kombination von Eigenschaften (Festigkeit, Leitfähigkeit, Biokompatibilität) ab. * Die Schnittstellen zwischen verschiedenen Materialien müssen für eine optimale Leistung sorgfältig geprüft werden. * Die Druckparameter müssen möglicherweise im Vergleich zu Einstoffpulvern angepasst werden. |
Anwendungen von 3D-Druck-Pulver
Druckpulver ermöglichen in einzigartiger Weise komplexe, kundenspezifische Teilegeometrien in allen Branchen:
Industrie | Beispiel Komponenten | Vorteile |
---|---|---|
Luft- und Raumfahrt | Turbinenschaufeln, Raketendüsen, UAV-Fahrgestelle | Gewichtsreduzierung, Leistungssteigerung |
Medizinische | Auf den Patienten abgestimmte Implantate, Prothetik | Personalisierte Größenanpassung, Biokompatibilität |
Automobilindustrie | Wärmetauscher, leichte Fahrwerkselemente | Teilekonsolidierung, Effizienz |
Industriell | Kundenspezifische Produktionswerkzeuge, Vorrichtungen | Verkürzte Entwicklungszeiträume |
Tabelle 5: Wichtige Anwendungsbereiche, die von den Möglichkeiten des 3D-Drucks von Pulver profitieren
Die Möglichkeit, Entwürfe schnell zu iterieren und Kleinauflagen kostengünstig zu drucken, ermöglicht die Innovation von Teilen für die Endanwendung.
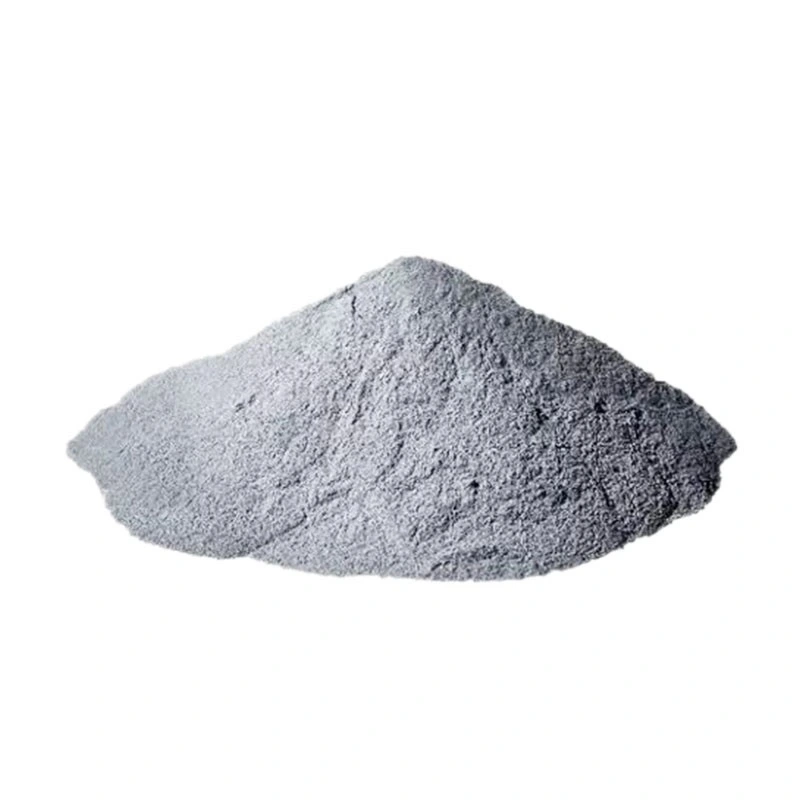
Vor- und Nachteile des pulverbasierten 3D-Drucks
Profis | Nachteile |
---|---|
Hohe Genauigkeit und Auflösung | Handhabung und Sicherheit von Pulvern |
Breite Palette von Materialien | Begrenzte Baugröße |
Minimale Unterstützungsstrukturen | Nachbearbeitungsanforderungen |
Fast Production Rates | Hohe Anfangsinvestition |
FAQs
F: Welcher Partikelgrößenbereich eignet sich am besten für 3D-Druckpulver aus Metall?
A: 10-45 Mikrometer erleichtern eine gute Packung und Verteilung und vermeiden Probleme mit ultrafeinen Pulvern bei der Handhabung des Pulvers. Die meisten Legierungen schneiden bei einer Verteilung von 30±15μm gut ab.
F: Welches 3D-Druckverfahren für Polymerpulver bietet die beste mechanische Leistung?
A: Das selektive Lasersintern (SLS) ermöglicht eine hervorragende Verschmelzung und die Herstellung feiner Merkmale - so entstehen hochleistungsfähige Kunststoffteile, die mit Spritzgussverfahren konkurrieren oder diese sogar übertreffen.
F: Wie lange kann unbenutztes 3D-Druckpulver aufbewahrt werden?
A: Mit Trockenmittel vor Feuchtigkeit geschützt in einer kühlen, trockenen Umgebung aufbewahrt, behalten die Pulver ihre Fließeigenschaften mindestens 12 Monate lang bei. Selbst geöffnete Pulver halten sich über 6 Monate, bevor sie sich merklich abbauen.
F: Hat die Qualität des Ausgangspulvers einen wesentlichen Einfluss auf die Eigenschaften der gedruckten Teile?
A: Ja, die Reinheit der Pulverchemie und eine angemessene Kontrolle der Pulvereigenschaften bestimmen in hohem Maße die mechanischen Eigenschaften des Endprodukts, die Ästhetik, die Maßhaltigkeit und die Zuverlässigkeit der Leistung.