Einführung
Haken: Stellen Sie sich vor, Sie könnten komplexe Metallobjekte Schicht für Schicht herstellen, wobei geschmolzenes Metall sorgfältig aufgetragen wird, um alles zu bauen, von hoch aufragenden Windturbinenkomponenten bis hin zu komplizierten medizinischen Implantaten. Diese faszinierende Welt gehört der gerichteten Energieabscheidung (Directed Energy Deposition, DED) und der additiven Fertigung mit Drahtbögen (WAAM), zwei revolutionäre Verfahren zur additiven Fertigung von Metallen (AM).
Problem: Die Entscheidung zwischen DED und WAAM kann eine schwierige Aufgabe sein. Beide verfügen über beeindruckende Fähigkeiten, aber ihre Nuancen können die Projektergebnisse erheblich beeinflussen.
Lösung: In dieser eingehenden Untersuchung werden DED und WAAM analysiert und ihre Kernaspekte, Anwendungen und Eignung für verschiedene Szenarien verglichen.
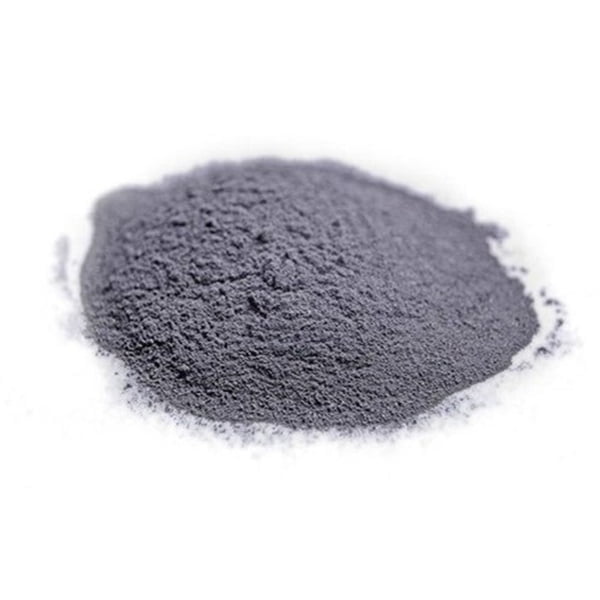
Verstehen der DED-Technologie
Definition: DED ist eine breite Kategorie von AM-Prozessen, bei denen eine konzentrierte Energiequelle (Laser, Elektronenstrahl, Plasmalichtbogen) verwendet wird, um Material (in der Regel Metallpulver) zu schmelzen und auf einer Bauplattform zu verschmelzen, wodurch ein 3D-Objekt Schicht für Schicht entsteht.
Wärmequellen:
Laser DED: Hochleistungslaser bieten eine präzise Steuerung und eine hervorragende Auflösung, ideal für komplizierte Geometrien. Zu den beliebten Materialien gehören Edelstahl, Titanlegierungen und Inconel.
Elektronenstrahl-DED: Erzeugt hoch fokussierte Energiestrahlen in einer Vakuumkammer, die eine hervorragende Schmelztiefe und Kompatibilität mit reaktiven Metallen wie Titan ermöglichen.
Plasma-Bogen-DED: Die Verwendung eines Plasmabrenners zum Schmelzen des Ausgangsmaterials bietet schnellere Abscheidungsraten und Kosteneffizienz für größere Strukturen, wobei häufig herkömmliche Schweißdrähte verwendet werden.
Metallpulver für DED:
Metallpulver | Beschreibung | Vorteile | Beschränkungen |
---|---|---|---|
Rostfreier Stahl 316L | Vielseitiger austenitischer Stahl, bekannt für seine hervorragende Korrosionsbeständigkeit, Biokompatibilität und hohe Festigkeit. | Weit verbreitet in der Luft- und Raumfahrt, bei medizinischen Implantaten und in der chemischen Verarbeitung. | Für eine optimale Oberflächenbeschaffenheit kann eine Nachbearbeitung erforderlich sein. |
Inconel 625 | Nickel-Chrom-Superlegierung, bekannt für ihre Hochtemperaturfestigkeit, Oxidationsbeständigkeit und Kriechfestigkeit. | Eingesetzt in anspruchsvollen Anwendungen in der Luft- und Raumfahrt, bei Gasturbinen und in der Kerntechnik. | Teurer als herkömmliche Stähle. |
Titan Ti-6Al-4V | Die Titanlegierung bietet ein ausgewogenes Verhältnis von Festigkeit, Gewicht und Korrosionsbeständigkeit. | Beliebt in der Luft- und Raumfahrt, in der Biomedizin und bei Sportartikeln aufgrund seiner Biokompatibilität. | Anfällig für Sauerstoffverunreinigungen während des Drucks, was eine sorgfältige Handhabung erfordert. |
Aluminium AlSi10Mg | Legierung, die eine gute Festigkeit mit leichten Eigenschaften und verbesserter Gießbarkeit kombiniert. | Wird in der Automobil-, Luft- und Raumfahrtindustrie sowie in der Schifffahrt zur Gewichtsreduzierung eingesetzt. | Hoch reaktiv, erfordert zum Drucken eine Inertgasumgebung. |
Werkzeugstahl H13 | Warmarbeitsstahl, bekannt für seine hervorragende Verschleißfestigkeit und Warmfestigkeit. | Wird für Formen, Gesenke und Stempel bei der Metallumformung und beim Schmieden verwendet. | Kann aufgrund seines hohen Kohlenstoffgehalts schwierig zu bedrucken sein. |
Nickellegierung 718 | Hochfeste, ausscheidungshärtende Nickellegierung mit hervorragenden mechanischen Eigenschaften bei hohen Temperaturen. | Wird wegen seiner Festigkeit und Kriechbeständigkeit für Bauteile in der Luft- und Raumfahrt verwendet. | Teurer als andere Optionen. |
Kupfer | Hochleitfähiges Metall mit thermischen und elektrischen Anwendungen. | Wird in elektrischen Leitern, Wärmetauschern und elektronischen Bauteilen verwendet. | Neigt zur Oxidation während des Drucks, was Kontrollmaßnahmen erfordert. |
Kobalt-Chrom (CoCr) | Biokompatible Legierung, die für verschleißfeste medizinische Implantate verwendet wird. | Wird aufgrund seiner hervorragenden Verschleißfestigkeit für Hüft- und Knieprothesen verwendet. | Kann eine besondere Handhabung und Nachbearbeitung zur Optimierung der Biokompatibilität erfordern. |
Inconel 718C | Variation von Inconel 625 mit verbesserten Gießeigenschaften und Schweißbarkeit. | Wird in Turbinenschaufeln und anderen Hochtemperaturanwendungen eingesetzt. | Ähnlich wie Inconel 625 in Bezug auf Eigenschaften und Einschränkungen. |
Anwendungen des DED: Komponenten für die Luft- und Raumfahrt, medizinische Implantate, Reparatur verschlissener Teile, Werkzeuge und große Metallstrukturen.
Entmystifizierung WAAM Technologie
Definition: WAAM (Wire Arc Additive Manufacturing) ist eine DED-Variante, bei der ein Endlosdraht und ein elektrischer Lichtbogen (in der Regel das Metallschutzgasschweißen) zum Schmelzen und Auftragen des Materials verwendet werden.
Vorteile:
Kosten-Nutzen-Verhältnis: WAAM nutzt die vorhandene Lichtbogenschweißtechnik und den leicht verfügbaren Draht und ist damit eine kostengünstigere Option im Vergleich zu pulverbasierten DED-Verfahren.
Hohe Ablagerungsraten: WAAM bietet aufgrund des kontinuierlichen Drahtvorschubs und der höheren Energiedichte des Lichtbogens schnellere Abscheidungsraten und eignet sich daher für Großprojekte.
Materialkompatibilität: WAAM bietet eine breite Materialkompatibilität mit verschiedenen gängigen Schweißdrähten, darunter:
Stahl: Baustahl, rostfreie Stähle (304L, 316L), rostfreie Duplexstähle und Werkzeugstähle.
Aluminium: Aluminiumlegierungen wie AlSi10Mg und Al 6061.
Nickellegierungen: Inconel 625 und Nickellegierung 718.
Andere Metalle: Kupfer, Titanlegierungen (eingeschränkte Verwendung aufgrund von Oxidationsproblemen).
Anwendungen von WAAM: Schiffbau, Bauwesen (Brückenteile, Träger), große Druckbehälter, Reparatur von Schwermaschinen und Rapid Prototyping von großen Metallstrukturen.
Wichtige Überlegungen: DED vs. WAAM
Die Druckgeschwindigkeit der DED-Technologie und WAAM Technologie ist anders
- DED: Bietet ein breiteres Spektrum an Druckgeschwindigkeiten, abhängig von der Wärmequelle und der Pulverzufuhrrate. Laser-DED bietet langsamere Geschwindigkeiten für hochpräzise Arbeiten, während Plasma-Lichtbogen-DED schnellere Geschwindigkeiten für größere Drucke erreicht.
- WAAM: Dank des kontinuierlichen Drahtvorschubs und der höheren Energiedichte des Lichtbogens weist es im Allgemeinen die schnellsten Abscheidungsraten unter den DED-Verfahren auf.
Die Materialkosten der DED-Technologie und der WAAM-Technologie sind unterschiedlich
- DED: Kann teurer sein, insbesondere bei Verfahren mit speziellen Metallpulvern wie Inconel oder reaktiven Metallen wie Titan.
- WAAM: In der Regel kostengünstiger, da leicht verfügbare und oft billigere Schweißdrähte verwendet werden.
Die Oberflächenbeschaffenheit der DED-Technologie und der WAAM-Technologie ist unterschiedlich
- DED: Laser-DED bietet aufgrund der präzisen Steuerung des Laserstrahls die glattesten Oberflächengüten. Die Elektronenstrahl-DED erzeugt ebenfalls gute Oberflächengüten. Die Plasmabogenentladung ist zwar schneller, erfordert aber möglicherweise mehr Nachbearbeitung, um die gewünschte Oberflächenqualität zu erreichen.
- WAAM: Aufgrund der beim Lichtbogenschweißen entstehenden Spritzer entstehen im Allgemeinen rauere Oberflächen als bei der Laserentladung. Die WAAM-Oberflächen können jedoch bearbeitet oder geschliffen werden, um die gewünschte Oberfläche zu erzielen.
Die Anwendungsbereiche sind unterschiedlich
- DED: Gut geeignet für komplizierte, hochpräzise Komponenten, die eine hervorragende Oberflächengüte erfordern, wie z. B. Teile für die Luft- und Raumfahrt, medizinische Implantate und Formen.
- WAAM: Hervorragend geeignet für großflächige Metallstrukturen, Rapid Prototyping sperriger Teile, Schiffskomponenten und die Reparatur massiver Maschinen aufgrund der hohen Abscheideraten und Kosteneffizienz.
Ausrüstungskosten der DED-Technologie und der WAAM-Technologie
- DED: DED-Systeme, insbesondere solche, die mit Lasern oder Elektronenstrahlen arbeiten, sind aufgrund der komplexen Technik in der Regel teurer als WAAM-Geräte.
- WAAM: WAAM-Systeme nutzen häufig die vorhandene Lichtbogenschweißtechnik, was sie zu einer kostengünstigeren DED-Option macht.
Vergleichstabelle der Vorteile und Beschränkungen
Merkmal | DED | WAAM |
---|---|---|
Wärmequelle | Laser, Elektronenstrahl, Plasmabogen | Lichtbogenschweißen (Gas-Metall-Lichtbogenschweißen) |
Rohstoff | Metallpulver | Durchgehender Draht |
Ablagerungsrate | Unterschiedlich (Laser DED: Langsam, Plasma Arc DED: Schneller) | Hoch |
Materialkompatibilität | Größere Auswahl an Materialien, einschließlich reaktiver Metalle | Hauptsächlich gängige Schweißdrahtmaterialien |
Oberfläche | Kann sehr glatt sein (Laser DED) | Im Allgemeinen rauher |
Anwendungen | Filigrane Bauteile, medizinische Implantate, Gussformen | Großflächige Strukturen, Rapid Prototyping, Reparatur |
Ausstattung Kosten | Im Allgemeinen höher | Im Allgemeinen niedriger |
Materialkosten | Kann bei speziellen Pulvern höher sein | Niedriger für gängige Schweißdrähte |
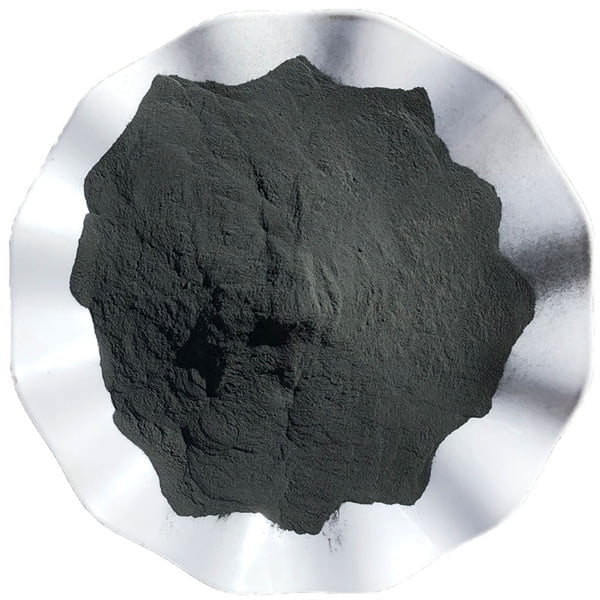
Die Wahl zwischen DED und WAAM
Die optimale Wahl zwischen DED und WAAM hängt von Ihren spezifischen Projektanforderungen ab:
Für komplizierte Teile mit kritischer Oberflächengüte und einer größeren Materialauswahl ist DED (insbesondere Laser DED) wahrscheinlich die bessere Wahl.
Bei groß angelegten, kostensensiblen Anwendungen, bei denen die Geschwindigkeit der Abscheidung und die Verfügbarkeit von Materialien im Vordergrund stehen, ist WAAM die ideale Lösung.
Zusätzliche Überlegungen:
- Komplexität des Projekts: DED eignet sich hervorragend für komplizierte Geometrien.
- Anforderungen an das Material: DED bietet breitere Materialoptionen, einschließlich reaktiver Metalle.
- Produktionsvolumen: Die Geschwindigkeit von WAAM ist vorteilhaft für großvolumige Projekte.
- Haushalt: WAAM ist im Allgemeinen kostengünstiger.
Zukunft von DED und WAAM
Sowohl die DED- als auch die WAAM-Technologie entwickeln sich rasch weiter. Wir können mit Fortschritten in folgenden Bereichen rechnen:
- Multi-Material-Fähigkeiten: DED und WAAM können Funktionen integrieren, um verschiedene Materialien innerhalb desselben Aufbaus für Verbundstrukturen aufzubringen.
- Hybride DED/WAAM-Systeme: Die Kombination von DED und WAAM in einer einzigen Maschine könnte mehr Flexibilität bei der Materialauswahl und den Abscheideraten bieten.
- Verbesserte Kontrolle und Automatisierung: Eine verbesserte Software- und Sensorintegration wird zu einer präziseren Steuerung des Druckprozesses führen.
FAQ
F: Welche Technologie ist schneller, DED oder WAAM?
A: WAAM weist im Allgemeinen die schnellsten Abscheideraten unter den DED-Verfahren auf. Der kontinuierliche Drahtvorschub und die höhere Energiedichte des Lichtbogens bei WAAM ermöglichen eine schnellere Materialabscheidung im Vergleich zu DED, insbesondere zu pulverbasierten DED-Verfahren. Bei komplizierten Arbeiten, die eine hohe Präzision erfordern, können mit dem Laser-DES-Verfahren jedoch moderate Geschwindigkeiten erreicht werden.
F: Ist DED oder WAAM teurer?
A: WAAM ist in der Regel die kostengünstigere Option. Hier ist eine Aufschlüsselung:
- Ausrüstung: WAAM-Systeme nutzen die bestehende Lichtbogenschweißtechnologie und sind damit kostengünstiger als DED-Maschinen, insbesondere solche, die Laser oder Elektronenstrahlen verwenden.
- Material: DED kann teurer sein, wenn Sie spezielle Metallpulver wie Inconel oder reaktive Metalle wie Titan benötigen. WAAM verwendet leicht verfügbare und oft billigere Schweißdrähte.
F: Welche Technologie bietet eine bessere Oberflächenqualität?
A: Das DED, insbesondere das Laser-DED, eignet sich aufgrund der präzisen Steuerung des Laserstrahls hervorragend zur Herstellung glatter Oberflächen. Auch die Elektronenstrahl-DED liefert gute Ergebnisse. Die Plasmabogenentladung ist zwar schneller, erfordert aber möglicherweise mehr Nachbearbeitung, um die gewünschte Oberflächenqualität zu erreichen. Beim WAAM-Verfahren werden aufgrund der beim Lichtbogenschweißen entstehenden Spritzer im Allgemeinen rauere Oberflächen erzeugt als beim Laser-DED-Verfahren. WAAM-Oberflächen können jedoch bearbeitet oder geschliffen werden, um eine glattere Oberfläche zu erhalten.
F: Für welche Art von Teilen sind DED und WAAM geeignet?
A: DED und WAAM eignen sich für unterschiedliche Anwendungsbereiche:
-
DED: Ideal für komplizierte, hochpräzise Bauteile, die eine hervorragende Oberflächengüte erfordern, wie z. B.:
- Luft- und Raumfahrtteile (Turbinenschaufeln, Triebwerkskomponenten)
- Medizinische Implantate (Hüftprothesen, Zahnprothesen)
- Gussformen und Werkzeugeinsätze
-
WAAM: Hervorragend geeignet für großflächige Metallstrukturen und Anwendungen, bei denen:
- Hohe Abscheidungsraten sind entscheidend (Schiffskomponenten, Brückenbalken)
- Schnelles Prototyping von sperrigen Teilen ist erforderlich
- Kosteneffizienz ist ein wichtiges Kriterium (Reparatur von großen Maschinen)
F: Ist der DED oder WAAM umweltfreundlicher?
A: Sowohl DED als auch WAAM können im Vergleich zu traditionellen subtraktiven Fertigungsverfahren wie der spanenden Bearbeitung als umweltfreundlich angesehen werden. Hier ist der Grund dafür:
- Geringerer Materialabfall: DED und WAAM nutzen additive Verfahren, bei denen die Teile Schicht für Schicht aufgebaut werden, wobei der Materialverlust im Vergleich zur maschinellen Bearbeitung, bei der überschüssiges Material entfernt wird, minimal ist.
- Potenzial für Recycling: Die beim DED verwendeten Metallpulver können potenziell recycelt und bei künftigen Konstruktionen wiederverwendet werden, was die Umweltbelastung minimiert.
Zusammengefasst, DED und WAAM sind leistungsstarke Technologien für die additive Fertigung von Metallen mit unterschiedlichen Stärken und Anwendungen. Wenn Sie die Kernprinzipien, die Materialkompatibilität und die Eignung für verschiedene Projektanforderungen verstehen, können Sie eine fundierte Entscheidung darüber treffen, welche Technologie Ihren Anforderungen am besten gerecht wird. Mit der weiteren Entwicklung dieser Technologien können wir mit noch größeren Möglichkeiten und einer breiteren Akzeptanz in verschiedenen Branchen rechnen.