Imagine a world where complex metal parts are crafted not by subtractive processes like machining, but by building them layer by layer. This is the magic of additive manufacturing, also known as 3D printing. But at the heart of this revolution lies a crucial ingredient: kugelförmiges, gaszerstäubtes Legierungspulver.
In this comprehensive guide, we’ll delve into the fascinating world of these tiny metallic spheres, exploring their creation, properties, applications, and the specific characteristics of various metal powder models. Buckle up, as we embark on a journey through the science and wonder of spherical gas atomized alloy powders!
Von geschmolzenem Metall zu mikroskopischen Wundern
Spherical gas atomized alloy powders are precisely engineered metallic particles, typically ranging from 10 to 150 micrometers in diameter (that’s about the width of a human hair!). These near-perfect spheres are created through a process called gas atomization. Here’s a simplified breakdown:
- Melting the Alloy: The raw material, an alloy of various metals, is melted inside a high-temperature furnace. Imagine a giant pot of molten metal, ready to be transformed.
- Zerstäubungskammer: The molten metal is then fed into an atomization chamber. Picture a high-pressure cauldron, where the magic happens.
- High-Pressure Gas Injection: Injected streams of inert gas, typically argon or nitrogen, break the molten metal stream into tiny droplets. Imagine a garden hose spraying water, but instead of water, it’s a stream of molten metal disintegrating into a metallic mist.
- Solidification in Flight: As the droplets travel through the chamber, they rapidly cool and solidify into perfect spheres. Think of tiny metal rain droplets, freezing mid-air and forming flawless spheres.
- Puder-Kollektion: The cooled spheres, now our precious gas atomized alloy powder, are collected and sieved to achieve the desired size distribution.
This process ensures consistent particle size and shape, crucial for several reasons:
- Fließfähigkeit: Spherical particles flow freely, making them ideal for automated additive manufacturing processes. Imagine tiny ball bearings rolling smoothly, compared to irregularly shaped pebbles getting stuck.
- Packungsdichte: Spherical particles pack tightly together, maximizing the amount of powder used in a build and minimizing voids or weaknesses in the final product.
- Laser Melting Efficiency: In additive manufacturing, a laser beam selectively melts the powder layer by layer. Spherical particles offer a more uniform melting profile compared to irregular shapes.
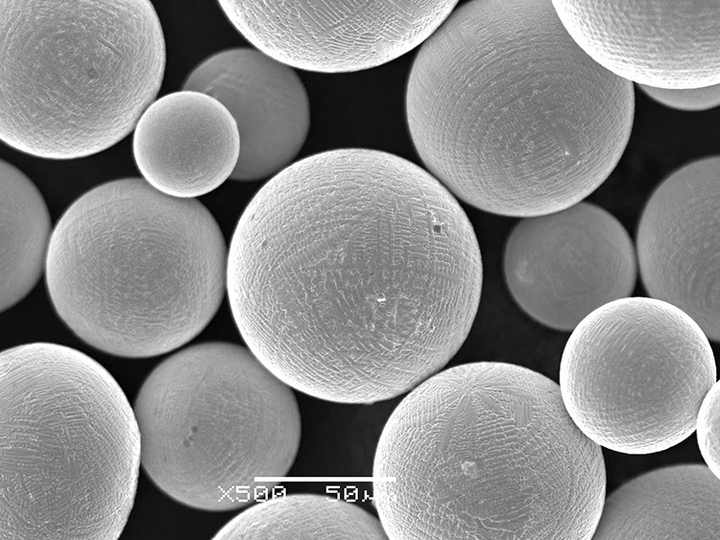
die Eigenschaften von Sphärische gaszerstäubte Legierungspulver
These remarkable powders boast a range of properties that make them invaluable in various applications. Let’s delve deeper into some key characteristics:
- Hohe Fließfähigkeit: As mentioned earlier, the spherical shape ensures smooth powder flow, crucial for consistent material deposition in additive manufacturing processes.
- Near-Net-Shape Capabilities: Additive manufacturing allows for creating complex geometries with minimal material waste. Spherical powders further enhance this ability due to their efficient packing density.
- Excellent Densification: During the additive manufacturing process, the powder layers are fused together. Spherical particles create a strong inter-particle bond, resulting in a denser and more robust final product.
- Maßgeschneiderte Eigenschaften: The composition of the alloy used to create the powder can be carefully controlled to achieve specific mechanical properties like strength, corrosion resistance, and thermal conductivity. Imagine having a toolbox of different metal powders, each with unique properties to suit your needs.
- Verbesserte Oberflächengüte: Compared to traditional manufacturing methods, additive manufacturing using spherical powders can often produce parts with a smoother surface finish, reducing the need for post-processing steps.
These properties, combined with the freedom of design offered by additive manufacturing, unlock a universe of possibilities for creating complex, high-performance components across various industries.
the Applications of Spherical Gas Atomized Alloy Powders
Spherical gas atomized alloy powders are not just for fancy 3D printers. They find application in a surprisingly diverse range of industries:
Additive Fertigung: As the name suggests, this is a primary application. Spherical powders are used to create intricate metal parts in aerospace, automotive, medical, and consumer goods industries. Imagine printing everything from lightweight aircraft components to customized medical implants, all thanks to these tiny metallic wonders.
Metall-Spritzgießen (MIM): MIM is a process where powdered metal is molded into near-net-shape parts and then sintered (heated) to achieve final strength. Spherical powders offer superior flowability and packing density, making them ideal for MIM applications. Think of complex, mass-produced metal parts like gears or tiny electronic components being shaped using these versatile powders.
10 Popular Alloy Powders
Now that we’ve explored the wonders of spherical gas atomized alloy powders in general, let’s get down to specifics. Here’s a closer look at 10 popular metal powder models, highlighting their unique compositions and applications:
- Rostfreier Stahl 316L:
This versatile powder, composed of iron, chromium, nickel, molybdenum, and other elements, offers excellent corrosion resistance, making it ideal for applications exposed to harsh environments like chemical processing plants, marine environments, and biomedical implants.
Anwendungen: Chemical processing equipment, marine hardware, medical implants, jewelry
- Inconel 625:
This nickel-chromium-based superalloy boasts exceptional high-temperature strength and oxidation resistance. It’s the go-to powder for components that operate under extreme heat, such as jet engine parts, rocket components, and heat exchangers in power plants.
Anwendungen: Aerospace components, turbine blades, heat exchangers, chemical processing equipment
- Titanium 6Al-4V (Ti-6Al-4V):
This lightweight and high-strength titanium alloy powder is prized for its excellent biocompatibility, making it a popular choice for medical implants like hip replacements and dental prosthetics. It also finds use in aerospace applications due to its impressive strength-to-weight ratio.
Anwendungen: Medical implants, aerospace components, sporting goods, high-performance automotive parts
- Aluminum Alloy 7075:
Known for its good strength-to-weight ratio and machinability, Aluminum 7075 powder is widely used in aerospace, automotive, and sporting goods industries. Think of lightweight aircraft components, high-performance bicycle frames, and even some golf clubs being built using this versatile powder.
Anwendungen: Aerospace components, automotive parts, sporting goods, electronics enclosures
- Kobalt-Chrom (CoCr):
This biocompatible alloy powder offers a unique combination of strength, wear resistance, and corrosion resistance. It’s a popular choice for demanding medical applications like joint replacements and dental implants.
Anwendungen: Medical implants, dental prosthetics, wear parts, cutting tools
- Nickel Superalloys:
This broad category encompasses various nickel-based alloys with exceptional high-temperature capabilities. These powders are used in demanding applications like turbine blades, combustor liners, and other hot-section components in gas turbine engines.
Anwendungen: Gas turbine engines, aerospace components, chemical processing equipment
- Werkzeugstähle:
These specially formulated alloy powders offer superior hardness, wear resistance, and toughness. They’re used to create cutting tools, dies, molds, and other components that need to withstand high wear and tear.
Anwendungen: Cutting tools, dies, molds, wear parts
- Kupfer-Legierungen:
Copper-based alloy powders, like copper-tin or copper-chromium, offer excellent thermal and electrical conductivity. These properties make them ideal for applications in heat sinks, electrical connectors, and brazing materials.
Anwendungen: Heat sinks, electrical connectors, brazing materials, electromagnetic components
- Refractory Metal Alloys:
These exotic powders, often composed of elements like tungsten, molybdenum, and tantalum, can withstand incredibly high temperatures. They’re used in applications like furnace linings, rocket nozzles, and heat shields for re-entry vehicles.
Anwendungen: High-temperature furnaces, rocket nozzles, heat shields, crucibles
- Edelmetall-Legierungen:
Powders made of precious metals like gold, silver, and platinum can be used for various applications, including jewelry making, electronics, and even some biomedical devices.
Anwendungen: Jewelry, electronics, electrical contacts, biomedical devices (limited applications)
This list just scratches the surface of the vast array of metal powder options available. By carefully selecting the right powder material for the specific application, manufacturers can leverage the unique properties of spherical gas atomized powders to create high-performance, complex components.
Advantages and Considerations of Sphärische gaszerstäubte Legierungspulver
While spherical gas atomized alloy powders offer numerous advantages, it’s important to consider some key factors:
Vorteile:
- Hervorragende Fließfähigkeit: Enables smooth powder handling and consistent material deposition in additive manufacturing processes.
- Erhöhte Packungsdichte: Minimizes voids and weaknesses in the final product, leading to stronger parts.
- Excellent Densification: Creates strong inter-particle bonds during the additive manufacturing process, resulting in a denser final product.
- Maßgeschneiderte Eigenschaften: Alloy composition can be controlled to achieve specific mechanical properties for diverse applications.
- Potential for Near-Net-Shape Manufacturing: Reduces material waste and allows for complex geometries.
Legierungspulver | Preisspanne (USD pro Kilogramm) |
---|---|
Rostfreier Stahl 316L | $20 – $50 |
Inconel 625 | $50 – $100 |
Titan 6Al-4V (Ti-6Al-4V) | $40 – $80 |
Aluminium-Legierung 7075 | $10 – $25 |
Kobalt-Chrom (CoCr) | $30 – $60 |
It’s important to remember that these are just estimates, and the actual price you pay will depend on the specific factors mentioned earlier. For accurate pricing information, it’s always best to contact potential suppliers directly and request a quote.
FAQs
Here are some frequently asked questions (FAQs) about spherical gas atomized alloy powders:
What are the benefits of using spherical gas atomized alloy powders over traditional metal powders?
Spherical gas atomized powders offer several advantages, including superior flowability, enhanced packing density, excellent densification, and the potential for near-net-shape manufacturing. These factors can lead to stronger, more consistent parts with improved surface finishes.
What are some of the limitations of spherical gas atomized alloy powders?
Cost is a primary consideration, as these powders can be more expensive than traditional options. Additionally, careful handling and storage are crucial to maintain powder quality and prevent contamination. Some metal powders can also pose health hazards, requiring proper safety protocols.
What are some of the applications of spherical gas atomized alloy powders?
These powders are widely used in additive manufacturing (3D printing) to create complex metal parts for various industries like aerospace, automotive, and medical. They also find application in metal injection molding (MIM) and thermal spraying processes.
How are spherical gas atomized alloy powders produced?
The process involves melting the desired alloy, atomizing the molten metal into droplets using a high-pressure gas stream, and then allowing the droplets to solidify into perfectly round spheres as they fall.
Where can I buy spherical gas atomized alloy powders?
Several specialty manufacturers worldwide produce these powders. When choosing a supplier, consider factors like material availability, powder specifications, quality control, pricing, lead times, and customer service.