Überblick über das selektive Laserschmelzen
Selektives Laserschmelzen (SLM) ist ein 3D-Druckverfahren für Pulverbettschmelzmetalle, bei dem mithilfe eines Lasers Metallpulverpartikel Schicht für Schicht selektiv geschmolzen und verschmolzen werden, um vollständig dichte Teile aufzubauen.
Hauptmerkmale der SLM-Technologie:
Charakteristisch | Beschreibung |
---|---|
Materialien | Metalle wie Edelstahl, Titan, Aluminium, Nickellegierungen |
Lasertyp | Faser-, CO2- oder Direktdiodenlaser |
Atmosphäre | Inerte Argon- oder Stickstoffatmosphäre |
Auflösung | Ermöglicht feine Strukturen bis zu 150 μm |
Genauigkeit | Teile innerhalb von ±0,2%-Abmessungen oder besser |
SLM ermöglicht komplexe, anpassbare Metallteile für Luft- und Raumfahrt-, Medizin-, Automobil- und Industrieanwendungen.
Wie selektives Laserschmelzen funktioniert
Das SLM-Druckverfahren funktioniert wie folgt:
- 3D-Modell, aufgeteilt in 2D-Querschnittsschichten
- Pulver in dünner Schicht auf der Bauplatte verteilen
- Der Laser scannt selektiv die Schicht und schmilzt das Pulver
- Geschmolzenes Pulver verfestigt sich und verschmilzt miteinander
- Bauplatte absenken und neue Schicht darauf verteilen
- Der Vorgang wird wiederholt, bis das gesamte Teil aufgebaut ist
Das ungeschmolzene Pulver unterstützt beim Aufbau des Bauteils. Dies ermöglicht komplexe Geometrien ohne dedizierte Stützstrukturen.
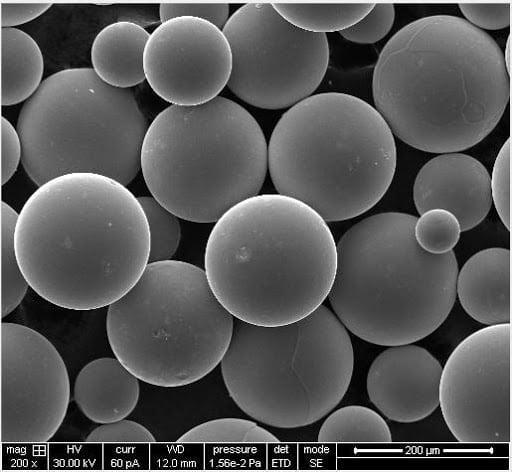
Arten von selektiven Laserschmelzsystemen
Es gibt einige SLM Systemkonfigurationen:
System | Einzelheiten |
---|---|
Einzellaser | Ein Hochleistungslaser zum Schmelzen |
Multilaser | Mehrere Laser zur Erhöhung der Baugeschwindigkeit |
Scansystem | Galvo-Spiegel oder feste Optik |
Handhabung von Metallpulver | Offene Systeme oder geschlossenes Pulverrecycling |
Atmosphärenkontrolle | Versiegelte Baukammer, gefüllt mit Argon oder Stickstoff |
Multi-Laser-Systeme ermöglichen schnellere Aufbauten, während die Pulverhandhabung im geschlossenen Kreislauf die Effizienz und Recyclingfähigkeit verbessert.
Materialien für das selektive Laserschmelzen
Zu den gängigen Metallmaterialien, die für SLM verwendet werden, gehören:
Material | Vorteile |
---|---|
Aluminium-Legierungen | Leicht mit guter Festigkeit |
Titan-Legierungen | Hohes Verhältnis von Festigkeit zu Gewicht |
Rostfreie Stähle | Korrosionsbeständigkeit, hohe Zähigkeit |
Werkzeugstähle | Hohe Härte und Verschleißfestigkeit |
Nickel-Legierungen | Hohe Temperaturbeständigkeit |
Kobalt-Chrom | Biokompatibel mit gutem Tragekomfort |
Eine Reihe von Legierungspulvern ermöglicht Eigenschaften wie Festigkeit, Härte, Temperaturbeständigkeit und Biokompatibilität, die für alle Anwendungen erforderlich sind.
Anwendungen des selektiven Laserschmelzens
Zu den typischen Anwendungen des SLM-Metalldrucks gehören:
Industrie | Anwendungen |
---|---|
Luft- und Raumfahrt | Motorkomponenten, Leichtbaustrukturen |
Medizinische | Individuelle Implantate, Prothetik, Instrumente |
Automobilindustrie | Leichte Teile, kundenspezifische Werkzeuge |
Industriell | Leichtbaukomponenten, Endproduktion |
Öl und Gas | Korrosionsbeständige Ventile, Bohrlochkopfteile |
SLM ermöglicht die Konsolidierung komplexer, kundenspezifischer Metallteile in einem Stück und die Optimierung von Gewicht und Leistung.
Vorteile des selektiven Laserschmelzens
Hauptvorteile der SLM-Technologie:
Nutzen Sie | Beschreibung |
---|---|
Komplexe Geometrien | Unbegrenzte Gestaltungsfreiheit für organische Formen |
Teilweise Konsolidierung | Baugruppen werden als eine einzelne Komponente gedruckt |
Personalisierung | Einfache Anpassung zur Herstellung kundenspezifischer Teile |
Gewichtsreduzierung | Gitterstrukturen und Topologieoptimierung |
Materialeinsparungen | Weniger Abfall im Vergleich zu subtraktiven Methoden |
Nachbearbeitung | Eventuell ist die Entfernung der Stütze und die Oberflächenbearbeitung erforderlich |
Diese Vorteile ermöglichen leistungsfähigere Metallteile für den Endverbrauch bei wettbewerbsfähigen Vorlaufzeiten und Kosten bei geringeren Produktionsmengen.
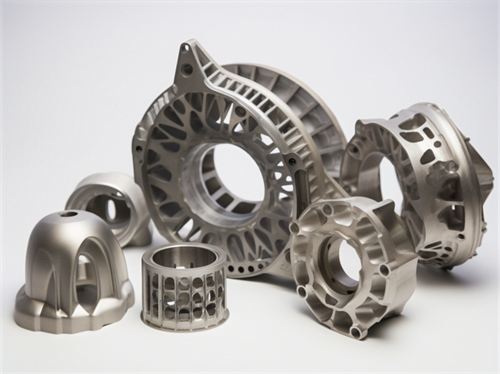
Einschränkungen des selektiven Laserschmelzens
Zu den Einschränkungen von SLM gehören:
Begrenzung | Beschreibung |
---|---|
Teilegröße | Beschränkt auf das Bauvolumen des Druckers, typischerweise unter 1 m3 |
Produktivität | Relativ langsame Produktionsraten begrenzen hohe Volumina |
Nachbearbeitung | Eventuell ist das Entfernen, Bearbeiten und Nachbearbeiten der Stütze erforderlich |
Anisotropie | Die mechanischen Eigenschaften variieren je nach Bauausrichtung |
Oberflächengüte | Die bedruckte Oberfläche ist relativ rau |
Betreiberkompetenz | Erfordert umfassende Druckererfahrung |
Die Technologie eignet sich am besten für geringe bis mittlere Produktionsmengen komplexer Metallteile.
Lieferanten von SLM-Druckern
Führende SLM-Systemhersteller:
Unternehmen | Bemerkenswerte Systeme |
---|---|
EOS | EOS M-Serie |
3D-Systeme | DMP-Serie |
GE-Zusatzstoff | X-Linie 2000R |
Trumpf | TruPrint 1000, 3000 |
SLM-Lösungen | SLM 500, SLM 800 |
Renishaw | AM500, AM400 |
Die Maschinen reichen von kleineren Bauvolumen um 250 x 250 x 300 mm bis hin zu großen 800 x 400 x 500 mm-Systemen für hohe Produktivität.
Auswahl eines SLM 3D-Druckers
Wichtige Überlegungen bei der Auswahl eines SLM-Systems:
Faktor | Priorität |
---|---|
Volumen aufbauen | Passend zu den erforderlichen Teilegrößen |
Unterstützte Materialien | Benötigte Legierungen wie Ti, Al, Edelstahl, Werkzeugstähle |
Inertgassystem | Versiegelte, automatisierte Handhabung von Argon oder Stickstoff |
Lasertechnologie | Faser-, CO2- oder Direktdiodenlaser |
Scanmethode | Galvo- oder Festspiegel-Scanning |
Handhabung des Pulvers | Kreislaufrecycling bevorzugt |
Das optimale SLM-System bietet die für die Anwendungen erforderlichen Materialien, Bauvolumen, Geschwindigkeit und Pulverhandhabungsfunktionen.
Anforderungen an SLM-Einrichtungen
Um einen SLM-Drucker betreiben zu können, muss die Einrichtung Folgendes erfüllen:
- Elektrische Leistungsstufen typisch 20–60 kW
- Stabile Temperatur um 20-25°C
- Niedrige Luftfeuchtigkeit unter 70% RH
- Partikelkontrolle und Handhabung von Metallpulver
- Zufuhr und Entlüftung von Inertgas
- Abgasfiltration für freigesetzte Partikel
- Überwachungssysteme für die Atmosphäre
- Strenge Personalsicherheitsverfahren
SLM-Systeme erfordern eine umfangreiche Infrastruktur für Stromversorgung, Kühlung, Pulverhandhabung und Inertgaszufuhr.
SLM-Druckprozessparameter
Typische SLM-Druckparameter:
Parameter | Typischer Bereich |
---|---|
Laserleistung | 100-400 W |
Scangeschwindigkeit | 100-2000 mm/s |
Schichtdicke | 20-100 μm |
Abstand zwischen den Luken | 50-200 μm |
Punktgröße | 50-100 μm |
Scanmuster | Abwechselnd, für jede Ebene gedreht |
Um für jedes Legierungspulver vollständig dichte Teile zu erhalten, ist eine genaue Anpassung dieser Parameter erforderlich.
SLM Designrichtlinien und -beschränkungen
Zu den wichtigsten SLM-Designrichtlinien gehören:
Leitfaden | Grund |
---|---|
Mindestwandstärke | Vermeiden Sie Hitzestau und Verformungen |
Unterstützte Überhänge | Ohne Stützen Einsturz verhindern |
Vermeiden Sie dünne Gesichtszüge | Schmelzen oder Verdampfen verhindern |
Orientierung für Stärke | Für Lastrichtung optimieren |
Minimieren Sie den Support-Einsatz | Vereinfachen Sie die Nachbearbeitung |
Der SLM-Prozess stellt geometrische Anforderungen wie Überhangwinkel und Mindeststrukturgrößen, die berücksichtigt werden müssen.
SLM-Nachbearbeitungsanforderungen
Gängige Nachbearbeitungsschritte für SLM-Teile:
Prozess | Zweck |
---|---|
Entfernung der Stütze | Entfernen Sie automatisch generierte Unterstützungen aus der Software |
Pulverentfernung | Entfernen Sie restliches Pulver aus den inneren Durchgängen |
Oberflächenbehandlung | Verbessern Sie die Oberflächenbeschaffenheit und Rauheit durch maschinelle Bearbeitung |
Stressabbau | Reduzieren Sie Eigenspannungen durch Wärmebehandlung |
Heißisostatisches Pressen | Verbessern Sie die Dichte und reduzieren Sie innere Hohlräume |
Der Grad der Nachbearbeitung hängt von den Anwendungsanforderungen an Toleranzen, Oberflächenbeschaffenheit und Materialeigenschaften ab.
Qualifikationstests für SLM-Teile
Typische Qualifikationstests für SLM-Komponenten:
Testtyp | Beschreibung |
---|---|
Dichteanalyse | Messen Sie die Dichte im Vergleich zu bearbeiteten Materialien |
Mechanische Prüfung | Zug-, Ermüdungs- und Bruchzähigkeitsprüfungen |
Metallographie | Mikrostrukturbildgebung und Defektanalyse |
Chemische Analyse | Überprüfen Sie, ob die Zusammensetzung mit der Spezifikation übereinstimmt |
Zerstörungsfrei | CT-Scannen oder Röntgeninspektion auf Hohlräume |
Durch gründliche Tests wird sichergestellt, dass SLM-Teile die Anforderungen erfüllen, bevor sie in Produktionsanwendungen eingesetzt werden.
Vorteile von SLM Technologie
Das selektive Laserschmelzen bietet entscheidende Vorteile:
- Komplexe, organische Geometrien sind mit Guss oder CNC nicht möglich
- leichtere Strukturen durch Topologieoptimierung
- Teilekonsolidierung in einzelne gedruckte Komponenten
- Weniger Abfall im Vergleich zu subtraktiven Methoden
- Anpassung und schnelle Designiterationen
- Just-in-time-Produktion von Metallteilen
- Hohe Festigkeit und Härte, die an bearbeitete Materialien heranreichen
Aufgrund dieser Vorteile eignet sich SLM branchenübergreifend für die On-Demand-Produktion hochwertiger Kleinserienteile.
Herausforderungen bei der Einführung des SLM-Drucks
Zu den Hindernissen für die Einführung von SLM gehören:
Herausforderung | Minderungsstrategien |
---|---|
Hohe Druckerkosten | Nutzen Sie Servicebüros, validieren Sie den ROI |
Material-Optionen | Neue Legierungen in der Entwicklung, Speziallieferanten |
Prozesswissen | Trainingsprogramme, Lernkurve |
Normen | Teilequalifizierungsprotokolle werden entwickelt |
Nachbearbeitung | Automatisierte Prozesse in Entwicklung |
Mit zunehmender Reife der Technologie werden diese Hindernisse durch verbesserte Materialien, Geräte, Schulungen und Standardisierungsbemühungen in der gesamten Branche abgebaut.
Die Zukunft des selektiven Laserschmelzens
Neue Trends in der SLM-Technologie:
- Größere Bauvolumina über 500 x 500 x 500 mm
- Multi-Laser-Systeme für schnellere Bauraten
- Strecklegierungen einschließlich Hochtemperatur-Superlegierungen
- Verbesserte Recyclingfähigkeit und Handhabung des Pulvers
- Automatisierte Support-Entfernung und Nachbearbeitung
- Hybridfertigung mit Kombination von AM und CNC
- Spezialisierte Software zur Designoptimierung
- Standardisierung von Prozessparametern und Teilequalifizierung
SLM-Systeme werden hinsichtlich Baugröße, Geschwindigkeit, Materialien und Zuverlässigkeit weiter weiterentwickelt, um den Produktionsanforderungen in immer mehr industriellen Anwendungen gerecht zu werden.
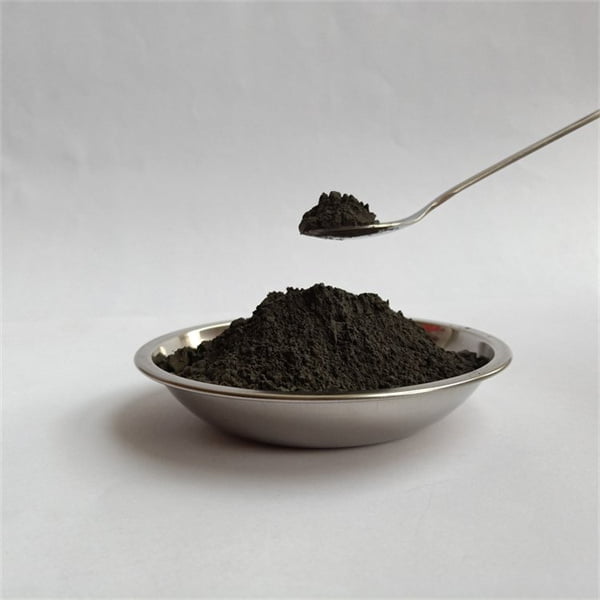
Zusammenfassung der wichtigsten Punkte
- SLM verschmilzt selektiv Metallpulver mit einem Laser für den 3D-Druck mit voller Dichte
- Pulverbettschmelzverfahren für feine Details und komplexe Geometrien
- Geeignet für Luft- und Raumfahrt-, Medizin-, Automobil- und Industrieanwendungen
- Verwendet Metalle wie Edelstahl, Titan, Aluminium und Nickellegierungen
- Bietet Vorteile der Teilekonsolidierung, Individualisierung und Gewichtsreduzierung
- Erfordert eine kontrollierte Atmosphäre und robuste Pulverhandhabungssysteme
- Bei gedruckten Teilen kann eine erhebliche Nachbearbeitung erforderlich sein
- Führende Technologie für Produktionsanwendungen mit kleinen bis mittleren Stückzahlen
- Laufende Verbesserungen bei Materialien, Baugröße, Geschwindigkeit und Qualität
- Ermöglicht hochleistungsfähige gedruckte Metallkomponenten
Das selektive Laserschmelzen wird als industrielle Fertigungslösung für kundenspezifische Metallteile nach Bedarf weiter wachsen.
FAQ
Frage | Antwort |
---|---|
Welche Materialien sind mit SLM kompatibel? | Die meisten schweißbaren Legierungen wie Edelstahl, Titan, Aluminium, Werkzeugstahl, Nickellegierungen und Kobalt-Chrom. |
Was ist die typische Genauigkeit von SLM-Teilen? | Für die meisten Geometrien ist eine Maßgenauigkeit von etwa ±0,2% erreichbar. |
Welche Nachbearbeitung ist erforderlich? | Üblich sind die Entfernung von Stützstrukturen, die Entfernung von Pulver, die Oberflächenveredelung, das Spannungsarmglühen und das heißisostatische Pressen. |
Was sind häufige SLM-Defekte? | Porosität, Rissbildung, Schichtablösung, Verzug, schlechte Oberflächenbeschaffenheit, nicht geschmolzene Partikel. |
Welche Lasertypen werden beim SLM verwendet? | Üblicherweise kommen Faserlaser, CO2-Laser oder Hochleistungsdioden zum Einsatz. |