Überblick über Inconel 718-Pulver
Inconel 718 ist ein Superlegierungspulver auf Nickel-Chrom-Basis, das für hochfeste Anwendungen bei erhöhten Temperaturen verwendet wird. Zu den wichtigsten Eigenschaften gehören:
- Hervorragende Festigkeit bis 700 °C
- Hohe Korrosions- und Oxidationsbeständigkeit
- Gute Ermüdungs- und Kriechfestigkeit
- Fähigkeit, kryogenen Temperaturen standzuhalten
- Kompatibilität mit Nachbearbeitung wie heißisostatischem Pressen
Inconel 718-Pulver wird häufig zur Herstellung von Komponenten für die Luft- und Raumfahrt-, Öl- und Gas-, Nuklear- und andere anspruchsvolle Industriezweige mittels additiver Metallfertigung oder Pulvermetallurgie verwendet.
Arten von Inconel 718-Pulver
Inconel 718-Pulver ist in verschiedenen Partikelgrößenverteilungen, Formen und Produktionsmethoden erhältlich:
Typ | Beschreibung | Partikelgröße | Form | Produktionsverfahren |
---|---|---|---|---|
Zerstäubtes Gas | Unregelmäßiges kugelförmiges Pulver | 15–75 μm | Meist kugelförmig | Gaszerstäubung |
Plasma zerstäubt | Hochgradig kugelförmiges Pulver | 15-45 μm | Hochgradig kugelförmig | Plasma-Zerstäubung |
Vermischt | Mischung aus gaszerstäubten und zerkleinerten Pulvern | 15-150 μm | Gemischte Morphologie | Mechanisches Mischen |
Legiert | Vorlegiertes Pulver mit einheitlicher Zusammensetzung | 15–105 μm | Kugelförmig oder unregelmäßig | Gas-/Plasmazerstäubung vorlegierter Schmelze |
Sphärische und vorlegierte Pulver bieten eine höhere Qualität, kosten aber mehr als gemischte oder gaszerstäubte Optionen. Die Wahl hängt von den Anwendungsanforderungen ab.
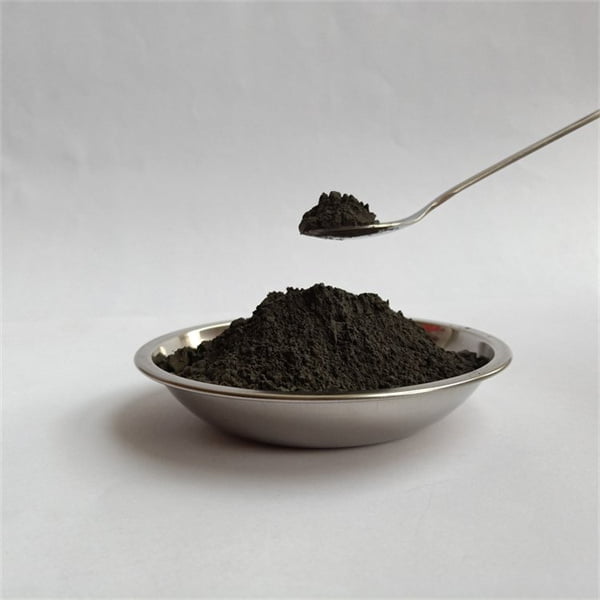
Eigenschaften und Zusammensetzung von Inconel 718
Inconel 718 verfügt über eine außergewöhnliche Kombination aus mechanischen Eigenschaften und Korrosionsbeständigkeit:
Eigentum | Wert |
---|---|
Dichte | 8,19 g/cm3 |
Schmelzpunkt | 1260-1336°C |
Endgültige Zugfestigkeit | 1.103 – 1.551 MPa |
Streckgrenze | 758 – 1.379 MPa |
Dehnung | Mindestens 12% |
Elastizitätsmodul | 205 GPa |
Querkontraktionszahl | 0.29 |
Schermodus | 79 GPa |
Ermüdungsfestigkeit | 517 – 1.034 MPa |
Die nominelle Zusammensetzung von Inconel 718 ist:
- Nickel: 50-55%
- Chrom: 17-21%
- Eisen: Gleichgewicht
- Niob: 4,75-5,5%
- Molybdän: 2,8-3,3%
- Titan: 0,65-1,15%
- Aluminium: 0,2-0,8%
Diese Kombination aus Nickel-, Chrom- und Niobzusätzen verleiht Inconel 718 seine hervorragenden mechanischen Eigenschaften bei hohen Temperaturen.
Anwendungen von Inconel 718-Pulver
Inconel 718-Pulver wird häufig verwendet in:
- Luft- und Raumfahrt – Triebwerkskomponenten wie Turbinenschaufeln, Scheiben, Befestigungselemente
- Öl und Gas – Bohrlochwerkzeuge, Ventile, Bohrlochkopfkomponenten
- Stromerzeugung – Teile des heißen Abschnitts von Gasturbinen, Befestigungselemente
- Automobil – Turboladerräder, Ventile, Motorkomponenten
- Chemische Verarbeitung – Reaktorbehälter, Wärmetauscher, Rohrleitungen
- Werkzeuge – Spritzgussformen, Matrizen, Werkzeugvorrichtungen
- Medizin – Orthopädische Implantate aufgrund der Biokompatibilität
Seine hohe Festigkeit bei erhöhten Temperaturen, Korrosionsbeständigkeit und Stabilität machen Inconel 718 zu einem idealen Material für kritische Komponenten in allen Branchen.
Vorteile von Inconel 718 Pulver
Zu den wichtigsten Vorteilen der Verwendung von Inconel 718-Pulver gehören:
- Die Teile behalten ihre hohe Festigkeit und Zähigkeit bis zu 700 °C
- Widersteht oxidierenden, korrosiven und kryogenen Umgebungen
- Doppelte Zugfestigkeit im Vergleich zu Edelstahl 316L
- Hervorragende Ermüdungs- und Kriechbrucheigenschaften
- Kann durch Alterungsbehandlung ausfällungsverstärkt werden
- Leicht schweißbar für Reparaturen und Verbindungen
- Beständig gegen Rissbildung beim heißisostatischen Pressen
- Kann bei minimaler Verschlechterung bis zu 10 Mal wiederverwendet werden
- Ermöglicht komplexe Geometrien, die durch maschinelle Bearbeitung nicht möglich sind
- Reduziert das Bauteilgewicht im Vergleich zu festen Formen
- Verringert das Buy-to-Fly-Verhältnis im Vergleich zu Knüppeln oder Schmiedeteilen
Diese Eigenschaften ermöglichen erhebliche Leistungssteigerungen und Gewichtseinsparungen bei Bauteilen.
Einschränkungen von Inconel 718-Pulver
Zu den Einschränkungen bei der Arbeit mit Inconel 718-Pulver gehören:
- Hohe Materialkosten im Vergleich zu Stahl- und Titanlegierungen
- Die Teilegröße ist basierend auf dem Bauvolumen der additiven Maschine eingeschränkt
- Anfällig für Oxidation und Korrosion über 700 °C
- Erfordert heißisostatisches Pressen nach der additiven Fertigung, um Spannungen abzubauen
- Beim Laser-Pulverbettschmelzen ist eine vollständige Verdichtung schwierig
- Nachbearbeitungen wie maschinelle Bearbeitung können aufgrund der Kaltverfestigung eine Herausforderung darstellen
- Um die gewünschte Rauheit zu erreichen, ist eine Oberflächenbearbeitung erforderlich
- Erfordert die Handhabung und Lagerung des trockenen Pulvers, um eine Kontamination zu verhindern
- Begrenzte Anzahl qualifizierter Lieferanten im Vergleich zu gängigeren Legierungen
Designprinzipien für Inconel 718-Teile
Wichtige Designrichtlinien für aus Pulver hergestellte Inconel 718-Komponenten:
- Für ausreichende Festigkeit wird eine Mindestwandstärke von 2 mm empfohlen
- Fügen Sie Fasen und Verrundungen ein, um Spannungskonzentrationen zu minimieren
- Interne Kanäle sollten zur Pulverentfernung einen Durchmesser von ≥ 2 mm haben
- Überstände ohne Stützen auf maximal 10 mm begrenzen
- Optimieren Sie die Bauausrichtung, um Stützen und Gesamthöhe zu minimieren
- Berücksichtigen Sie beim Sintern eine isotrope Schrumpfung von ~20%
- Berücksichtigen Sie eine geringere Genauigkeit und eine höhere Oberflächenrauheit als bearbeitete Teile
- Design zur einfacheren Pulverentfernung durch Einbeziehung von Öffnungen
- Planen Sie zusätzliches Bearbeitungsmaterial ein, wenn eine hohe Maßgenauigkeit oder Oberflächengüte erforderlich ist
Die Simulation von Builds zu Beginn des Designprozesses hilft dabei, etwaige Probleme vor der Herstellung zu erkennen.
Prozessparameter für Inconel 718 AM
Zu den kritischen Parametern für die additive Fertigung von Inconel 718 gehören:
- Laserleistung: 100-500 W
- Scangeschwindigkeit: Bis zu 10 m/s
- Strahldurchmesser: 50-100 μm
- Schichtdicke: 20-50 μm
- Schraffur-Abstand: 50-200 μm
- Scan-Strategie: Wechsel zwischen den Ebenen
- Schutzgas: Argon oder Stickstoff
- Gasdurchfluss: 2–8 l/min
- Temperatur der Bauplatte: 60–100 °C
- Nachbearbeitung: Heißisostatisches Pressen, Wärmebehandlung
Diese Parameter müssen präzise optimiert werden, um dichte Bauteile mit der gewünschten Mikrostruktur und den gewünschten mechanischen Eigenschaften zu erhalten.
Nachbearbeitung von Inconel 718-Teilen
Zu den typischen Nachbearbeitungsschritten für Inconel 718 AM-Komponenten gehören:
- Entfernung von losem Pulver durch Strahlen mit Kunststoffperlen
- Spannungsabbauende Wärmebehandlung bei 1080 °C für 1 Stunde, gefolgt von Luftkühlung
- Heißisostatisches Pressen bei 1120 °C für 4 Stunden unter einem Druck von 100 MPa
- Drahterodiermaschine zum Entfernen von Teilen von der Bauplatte
- CNC-Bearbeitung – Fräsen, Bohren, Drehen zur Verbesserung von Finish und Präzision
- Oberflächenveredelung – Schleifen, Schleifen, Polieren
- Kugelstrahlen zur Erzeugung von Druckspannungen auf Oberflächen
- Qualitätsprüfung – Zugfestigkeit, Härte, Mikrostruktur, Fraktographie
Um die für die Anwendung erforderlichen Materialeigenschaften zu erreichen, ist eine ordnungsgemäße Nachbearbeitung von entscheidender Bedeutung.
Qualitätskontrolltests für Inconel 718
Umfassende Qualitätskontrolltests stellen die Qualität des Pulvers und der gedruckten Teile sicher:
- Chemische Analyse – ICP-OES bestätigt, dass die Pulverzusammensetzung der AMS-Spezifikation entspricht
- Pulverpartikelgrößenverteilung – Laserbeugungs-Partikelgrößenanalysator
- Pulvermorphologie – REM-Bildgebung verifiziert die sphärische Pulverform
- Pulvermikrostruktur – EBSD-Kartierung der Kornstruktur
- Pulverfließfähigkeit – Gemessen durch Hall- und Carney-Trichtertests
- Dichteanalyse – Heliumpyknometrie und Archimedes-Methode bestätigen eine Dichte von >99,5%
- Mechanische Prüfung – Zug-, Ermüdungs-, Bruchzähigkeits- und Härteprüfung
- Mikrostruktur – Korngröße und Phasenverteilung mittels optischer und REM-Mikroskopie
- Fehleranalyse – Röntgen- und CT-Scans prüfen auf interne Fehler
- Oberflächenrauheit – Gemessen mit einem Stift oder einem optischen Profilometer
Umfangreiche Tests stellen sicher, dass Inconel 718-Teile strenge Luft- und Raumfahrt- und Industriestandards erfüllen.
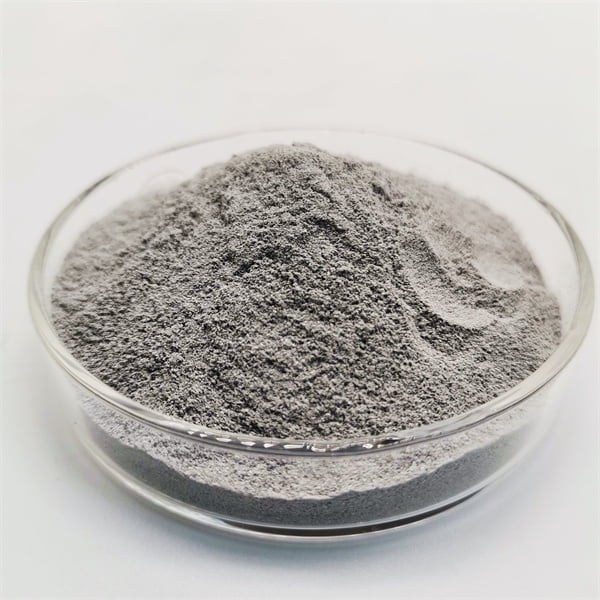
Kostenanalyse für Inconel 718 AM
Die mit der Produktion von Inconel 718 AM verbundenen Kosten umfassen:
- Maschinenkosten – $500.000 bis $1 Million für ein hochwertiges AM-System
- Materialkosten – $350-500/kg für reines Inconel 718-Pulver
- Arbeitskosten – Erfahrene Bediener für die Erstellung und Nachbearbeitung
- Energiekosten – Großer Stromverbrauch während des Aufbaus
- Nachbearbeitung – HIP-, Bearbeitungs- und andere Endbearbeitungskosten
- Qualitätskontrolle – Test- und Charakterisierungskosten
- Wiederverwendbarkeit – Nicht verwendetes Pulver kann recycelt werden, um die Materialkosten zu senken
- Auftragsvolumen – Höhere Bestellmengen bieten Skalenvorteile
- Buy-to-fly-Verhältnis – Es muss ungenutztes Pulver berücksichtigt werden, das recycelt werden muss
- Teilegeometrie – Gut gestaltete Teile maximieren die Materialausnutzung
Bei der Produktion geringer bis mittlerer Stückzahlen ist AM im Vergleich zur subtraktiven Bearbeitung aufgrund der Materialeinsparungen und der Reduzierung des Buy-to-Fly-Verhältnisses kostengünstiger.
Auswählen eines Inconel 718-Pulver Anbieter
Schlüsselfaktoren bei der Auswahl eines Inconel 718-Pulverlieferanten:
- Technische Expertise in der Gas- und Plasmazerstäubung von Nickel-Superlegierungen
- Verschiedene verfügbare Pulvergrößen und -morphologien – sphärisch, gemischt, legiert
- Qualitätssicherungsverfahren und Zertifizierungen – ISO 9001, AS9100 usw.
- Fähigkeit zur Durchführung chemischer Analysen und Tests der Partikelgrößenverteilung
- Kapazität zur Lieferung großer Pulvermengen mit kurzen Lieferzeiten
- Anpassungsmöglichkeiten wie das Sieben nach bestimmten Partikelgrößenverteilungen
- Wettbewerbsfähige und stabile Preise, insbesondere bei Bestellungen großer Mengen
- Fähigkeit, bei Bedarf die Einhaltung gesetzlicher Vorschriften einzuhalten – ITAR, REACH, RoHS
- Muster für die Qualifizierung und Prüfung von Kundenpulvern
- Technischer Support für Pulverhandhabung und -lagerung
- Geografische Nähe für schnellere Logistik und Support
Etablierte Lieferanten mit Nischenkompetenz bei Nickellegierungspulvern erfüllen in der Regel die Anforderungen der Benutzer in Bezug auf Qualität, Anpassung, Preisgestaltung und Support am besten.
Vor- und Nachteile von Inconel 718 im Vergleich zu Edelstahl
Vorteile von Inconel 718:
- Doppelt so zugfest wie Edelstahl 316L
- Deutlich höhere Kriech- und Ermüdungsfestigkeit
- Beständig gegen Oxidation und Korrosion bis 700 °C
- Höhere Ermüdungsbeständigkeit bei hohen Lastwechselzyklen als bei Stählen
- Gleichbleibende Eigenschaften aufgrund der Zusammensetzung der Nickellegierung
- Kann im Gegensatz zu Standard-Edelstählen aushärtbar sein
- Erzeugt stärkere Bindungen, wenn es als Grundbeschichtung aufgetragen wird
- Leichter zu recyceln und nicht verwendetes Pulver wiederzuverwenden
Nachteile von Inconel 718:
- Wesentlich höhere Materialkosten als bei rostfreiem Stahl
- Niedrigere maximale Betriebstemperatur als Edelstahl
- Beim AM-Druck ist es schwieriger, es vollständig zu verdichten
- Aufgrund der Kaltverfestigung schwierig zu bearbeiten
- Begrenzte Anzahl von qualifizierten Lieferanten
- Anfällig für Flüssigmetallversprödung während AM
- Höhere Nachbearbeitungsanforderungen – HIP, Wärmebehandlung
- Erfordert eine Verarbeitung in kontrollierter Inertatmosphäre
Für kritische Anwendungen, bei denen die Leistung die Kostenerwägungen übersteigt, bietet Inconel 718 im Vergleich zu rostfreien Stählen deutlich bessere Hochtemperatureigenschaften.
Vergleich von Inconel 718 mit Inconel 625
Inconel 718 und 625 weisen die folgenden charakteristischen Merkmale auf:
Legierung | Stärke | Korrosionsbeständigkeit | Schweißeignung | Kosten | Verwenden Sie Temperatur |
---|---|---|---|---|---|
Inconel 718 | Sehr hoch | Mäßig | Messe | Hoch | Bis zu 700°C |
Inconel 625 | Mittel | Ausgezeichnet | Ausgezeichnet | Sehr hoch | Bis zu 980°C |
- Inconel 718 bietet eine viel höhere Zug-, Kriech- und Ermüdungsfestigkeit.
- Inconel 625 bietet eine insgesamt bessere Korrosions- und Oxidationsbeständigkeit.
- Inconel 625 weist eine hervorragende Schweißbarkeit auf, während Inconel 718 eine größere Herausforderung darstellt.
- Inconel 625 ist aufgrund der umfangreichen Zusätze von Columbium-Legierungen teurer.
- Inconel 625 hat eine höhere maximale Betriebstemperatur.
Inconel 718 wird für die anspruchsvollsten hochfesten Anwendungen wie Luft- und Raumfahrtkomponenten bevorzugt, während Inconel 625 ausgewählt wird, wenn Korrosionsbeständigkeit die wichtigste Anforderung ist.
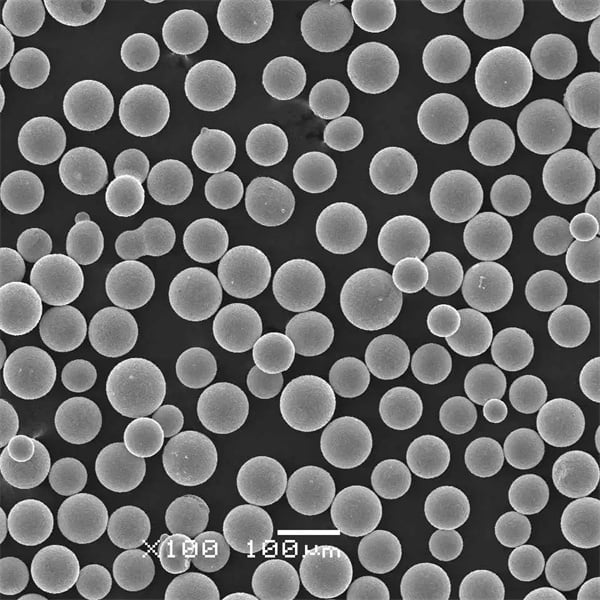
FAQ
Welche Partikelgrößenverteilung wird für AM mit Inconel 718-Pulver empfohlen?
Für die Laser-Pulverbettschmelzung mit Inconel 718 wird typischerweise ein Partikelgrößenbereich von 15–45 Mikrometern mit einem Großteil zwischen 20–35 Mikrometern empfohlen, um eine gute Fließfähigkeit und dichte Verdichtung zu ermöglichen.
Welche Nachbearbeitungswärmebehandlungen werden für Teile aus Inconel 718 AM verwendet?
Zu den üblichen Wärmebehandlungen gehören Lösungsglühen bei 1270 °C, Ausscheidungshärten bei 960 °C und Spannungsarmglühen bei 1080 °C. Mehrstufige Alterungsbehandlungen können die Festigkeit und Duktilität weiter verbessern.
Was sind einige typische Anwendungen für Inconel 718-Pulver in der Luft- und Raumfahrt?
Inconel 718 wird häufig zur Herstellung von Flugzeugtriebwerkskomponenten wie Rotorblättern, Scheiben, Befestigungselementen, Gehäusen und Fahrwerksteilen verwendet, die eine hohe Festigkeit bei erhöhten Temperaturen und in korrosiven Umgebungen erfordern.
Ist für Inconel 718 nach AM ein heißisostatisches Pressen erforderlich?
Ja, HIP wird nach der Laser- oder Elektronenstrahl-Pulverbettschmelzung mit Inconel 718 dringend empfohlen, um innere Hohlräume und Poren zu beseitigen und die Ermüdungslebensdauer durch Mikrostrukturhomogenisierung zu verbessern.
Wie ist mit unbenutztem Inconel 718-Pulver umzugehen?
Sämtliches unbenutztes Pulver muss in einer inerten Atmosphäre gehandhabt werden, um Oxidation und Kontamination zu verhindern. Das Pulver kann bis zu 10 Mal wiederverwendet werden, wenn es in einer kontrollierten Umgebung aufbewahrt wird. Bei mehr als 10 Recyclingvorgängen wird neues Pulver empfohlen.