Übersicht
Eisenpulver für hohe Temperaturen sind spezielle Metallpulver aus Eisenbasislegierungen, die für den Betrieb bei hohen Temperaturen von über 850 °C ausgelegt sind, ohne schnell an Festigkeit zu verlieren. Herkömmliche Eisen- und Stahlpulver oxidieren und verschlechtern sich jenseits dieser Schwelle schneller.
Durch eine sorgfältige Anpassung der Pulverchemie und der Verarbeitungsprozesse werden die Festigkeit bei hohen Temperaturen und die Umweltbeständigkeit verbessert. Zu den wichtigsten Anwendungsbereichen, die solche extremen thermischen Strukturwerkstoffe erfordern, gehören die Automobilindustrie, die Luft- und Raumfahrt, Energieerzeugungsanlagen und die chemische Verarbeitungsindustrie.
Arten von Hochtemperatur-Eisenpulver
Typ | Produktionsverfahren | Wesentliche Merkmale | Anwendungen (aufgrund der Hochtemperaturleistung) |
---|---|---|---|
Carbonyl-Eisen-Pulver | Zersetzung von Eisenpentacarbonyl-Dampf bei hohen Temperaturen | - Hohe Reinheit (>99% Fe) - Sphärische Partikelmorphologie - Glatte Oberfläche - Enge Größenkontrolle - Weichmagnetische Eigenschaften | - Magnetische Hochleistungskomponenten (z. B. Induktoren für Hochfrequenzanwendungen) - Weichmagnetkerne für Transformatoren und Motoren - Mikrowellenabsorber - Katalysatoranwendungen aufgrund der großen Oberfläche |
Elektrolytisches Eisenpulver | Elektrolyse von Eisenchloridlösungen | - Sehr hohe Reinheit (oft über 99,5% Fe) - Dichte, kugelförmige Partikel - Ausgezeichnete Fließfähigkeit - Hohe Kompressibilität | - Weichmagnetische Kerne für Hochfrequenzanwendungen wie Transformatoren und Drosseln - Elektronische Bauteile, die eine hohe Reinheit erfordern (z. B. elektromagnetische Abschirmung) - Additive Fertigung komplexer, nahezu netzförmiger Metallteile - Anwendungen, die eine gute elektrische Leitfähigkeit bei hohen Temperaturen nutzen |
Wasserverdüstes Eisenpulver | Geschmolzenes Eisen wird mit Hochdruckwasserstrahlen in feine Partikel gebrochen | - Hohe Produktionsrate - Niedrigste Kosten unter den Hochtemperatur-Eisenpulvern - Relativ hoher Sauerstoffgehalt - Unregelmäßige Partikelformen - Breite Partikelgrößenverteilung | - Anwendungen, bei denen die Kosten im Vordergrund stehen (z. B. einige Metallspritzgussverfahren) - Teile, die nach dem Sintern eine gute Bearbeitbarkeit erfordern - Hochtemperaturlöten aufgrund des Vorhandenseins von Sauerstoff - Anwendungen, die von einer unregelmäßigen Partikelpackung profitieren (z. B. einige Filtermedien) |
Vakuumgeglühtes Eisenpulver | Weiterverarbeitung von anderen Eisenpulvern (oft wasserverdüst) durch Glühen in einer Wasserstoffatmosphäre | - Verbessert die Eigenschaften des Ausgangspulvers (z. B. Reduzierung des Sauerstoffgehalts, Verbesserung der Partikelform) - Maßgeschneiderte Eigenschaften auf der Grundlage des Ausgangspulvers | - Anwendungen, die ein ausgewogenes Verhältnis zwischen Kosten und Hochtemperaturleistung erfordern (z. B. einige weichmagnetische Komponenten) - Additive Fertigungsverfahren, bei denen spezifische Pulvereigenschaften erforderlich sind - Lötanwendungen, die eine gute Leistung bei erhöhten Temperaturen erfordern |
Produktionsmethoden für Hochtemperaturpulver
Methode | Beschreibung | Vorteile | Benachteiligungen | Typische produzierte Materialien |
---|---|---|---|---|
Gaszerstäubung | Geschmolzenes Metall wird mit Hilfe eines Hochgeschwindigkeits-Inertgasstroms in feine Tröpfchen zerlegt | - Hochreine Pulver - Sphärische Partikelmorphologie - Enge Größenverteilung - Gute Fließfähigkeit - Geeignet für eine breite Palette von Materialien | - Hoher Energieverbrauch - Relativ teuer im Vergleich zu einigen anderen Methoden - Potenzielle Oxidbildung bei einigen Materialien | - Hochtemperaturlegierungen (z. B. Nickelsuperlegierungen, Titanaluminide) - Refraktärmetalle (z. B. Wolfram, Molybdän) - Werkzeugstähle |
Wasserzerstäubung | Das geschmolzene Metall wird mit Hochdruck-Wasserstrahlen in Tröpfchen zerlegt. | - Hohe Produktionsrate - Niedrige Kosten - Anwendbar auf eine breite Palette von Materialien | - Unregelmäßige Partikelformen - Breite Partikelgrößenverteilung - Höherer Sauerstoffgehalt im Vergleich zur Gaszerstäubung | - Niedriglegierte Stähle und Eisen - Rostfreie Stähle (für einige Anwendungen) - Metallpulverspritzguss (MIM) |
Plasma-Zerstäubung | Geschmolzenes Metall wird in einen Hochtemperatur- und Hochgeschwindigkeitsplasmastrom eingespritzt, was zu einer schnellen Erstarrung führt. | - Ultrafeine Pulver (<10 Mikrometer) - Sphärische Partikel - Enge Größenverteilung - Möglichkeit der Bildung metastabiler Phasen | - Sehr hoher Energieverbrauch - Begrenzte Produktionskapazität - Komplizierter und teurer Prozess | - Amorphe Metallpulver - Hochleistungslegierungen für Luft- und Raumfahrt und Turbinenanwendungen |
Carbonyl-Zersetzung | Thermische Zersetzung von Metallcarbonylen (kohlenmonoxidhaltige Metallverbindungen) bei hohen Temperaturen | - Hochreine Pulver - Sphärische Partikelmorphologie - Strenge Kontrolle über Partikelgröße und Morphologie | - Begrenzt auf einige wenige Metalle, die stabile Carbonylgruppen bilden (z. B. Eisen, Nickel) - Komplexer und relativ langsamer Prozess | - Hochreine Eisenpulver für magnetische Anwendungen - Katalysatormaterialien |
Elektrolyse | Abscheidung von Metall aus einem geschmolzenen Salz oder einer wässrigen Lösung unter Verwendung von elektrischem Strom | - Sehr hochreine Pulver - Dichte, kugelförmige Partikel - Ausgezeichnete Fließfähigkeit | - Begrenzte Produktionsrate - Hohe Kosten - Anwendbar auf eine begrenzte Anzahl von Materialien | - Elektrolytisches Eisenpulver für magnetische Hochleistungsbauteile - Kupferpulver für elektrische Anwendungen |
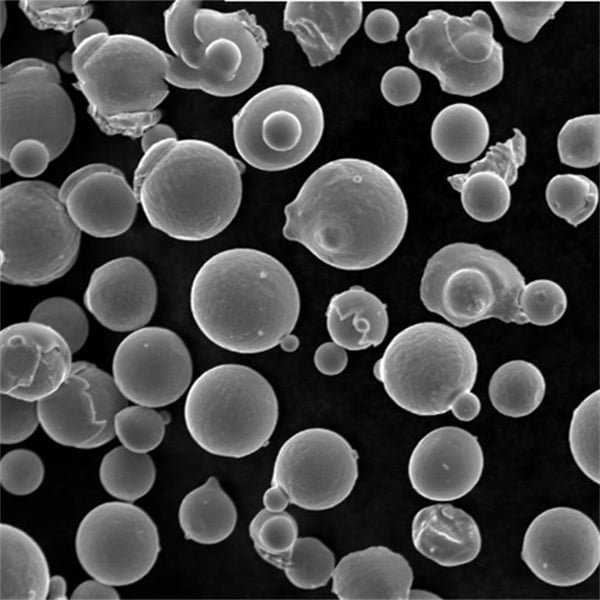
Legierungstypen und -zusammensetzungen
Es gibt vier Hauptkategorien von Spezialeisenlegierungspulvern, die für den dauerhaften Einsatz bei Temperaturen von über 850 °C ausgelegt sind:
Austenitische Edelstahl-Pulver
Legierungen wie 316L, 304L und 301L enthalten Nickel, um eine austenitische FCC-Kristallstruktur bis zu 1100°C aufrechtzuerhalten, und Chrom für die Oxidationsbeständigkeit durch schützende Chromoxid (Cr2O3)-Oberflächenfilme bei hohen Temperaturen.
Legierungselement | Rolle | Gewicht % Bereich |
---|---|---|
Nickel (Ni) | Austenit-Stabilisator | 8 – 12% |
Chrom (Cr) | Oxidationsbeständigkeit | 16 – 18% |
Mangan (Mn) | Festigkeit und Kornverfeinerung | Bis zu 2% |
Stickstoff (N) | Stärkung | 0.1 – 0.25% |
Vorteile: Ausgezeichnete "Warmfestigkeit", leichte Verdichtung und Sinterung, geringere Kosten als Superlegierungen.
Beschränkungen: Neigt bei Temperaturen über 1000°C zum Kriechen, nicht geeignet für dynamische Anwendungen mit hoher Belastung.
Eisenlegierungen mit hohem Nickelgehalt
Nickel-Eisen-Legierungen mit einem Nickelgehalt von 25 - 60 Gew.-%TP3T bieten die optimale Kombination aus Hochtemperaturfestigkeit, Zähigkeit und Korrosionsbeständigkeit. Nickelzusätze verlangsamen die Diffusionsraten drastisch und reduzieren schädliche Gefügeveränderungen bis zu 1150°C.
Andere wichtige Legierungselemente sind:
Legierungselement | Rolle | Gewicht % Bereich |
---|---|---|
Nickel (Ni) | Stärkung der festen Lösung | 25 – 60% |
Chrom (Cr) | Oxidationsbeständigkeit | 10 – 25% |
Kobalt (Co) | Verbessert die mechanischen Eigenschaften bei hohen Temperaturen | 10 – 25% |
Molybdän (Mo) | Kriechstromfestigkeit | 2 – 6% |
Vorteile: Unübertroffene mechanische Leistung bei 1100°C+, langsamere Abbaukinetik. Thermisch stabiles Mikrogefüge.
Beschränkungen: Sehr hohe Legierungspreise, Schwierigkeiten bei der Kontrolle der Porosität, erfordert HIP-Verdichtung.
Durch Oxiddispersion verstärkte Eisenlegierungen
In oxiddispersionsgehärteten Legierungen sind sehr feine (50-100 nm) inerte Yttriumoxidpartikel in die Materialmatrix eingebettet. Diese nanoskaligen Oxide behindern die Versetzungsbewegung und erhalten so die Festigkeit über 1000°C.
Legierungselement | Rolle | Gewicht % Bereich |
---|---|---|
Yttriumoxid (Y2O3) | Nano-Oxid-Teilchen für thermische Stabilität | 0.25% – 1% |
Chrom (Cr) | Umweltverträglichkeit | Bis zu 20% |
Aluminium (Al) | Verbessert die Oxiddispersion | Bis zu 4% |
Vorteile: Außergewöhnliche Gefügestabilität und Kriechfestigkeit bei Betriebsbedingungen über 1100°C.
Beschränkungen: Sehr hohe Kosten, schwierige Verarbeitung - traditionell durch mechanisches Legieren und Verfestigung hergestellt.
Eisenaluminid (FeAl)-Legierungen
Eisenaluminid-Legierungen mit einem Aluminiumgehalt von 10-40% bieten eine ausgezeichnete Oxidations- und Sulfidierungsbeständigkeit bis zu 900°C durch die Bildung einer dauerhaften Aluminiumoxid (Al2O3)-Schutzschicht. Chrom unterstützt den Oberflächenschutz.
Legierungselement | Rolle | Gewicht % Bereich |
---|---|---|
Aluminium (Al) | Oxidationsbeständigkeit | 10 – 40% |
Chrom (Cr) | Verbessert die Umweltresistenz | 5 – 10% |
Kohlenstoff, Zr (C, Zr) | Hartmetall-Verstärker | Bis zu 0,5% |
Vorteile: Hervorragende Umweltstabilität, geringere Dichte als Stähle, einfachere Verarbeitung als bei Superlegierungen.
Beschränkungen: Festigkeitsverlust oberhalb von 750°C, schlechte Kriechbeständigkeit, angewandte Spannungen verstärken Pesterscheinungen.
Produktionsmethoden
Es werden spezielle Verfahren eingesetzt, um maßgeschneiderte Pulver aus Hochtemperatur-Eisenlegierungen mit geeigneten Eigenschaften herzustellen:
Gaszerstäubung
- Die kontrollierte schnelle Abkühlung des geschmolzenen Metallstroms ermöglicht es, die Legierungselemente in Lösung zu halten, anstatt Ausscheidungen zu bilden
Plasma-Sphäroidisierung
- Unregelmäßige Pulver aus Wasserzerstäubungsprozessen werden mit einem Plasmabrenner wieder aufgeschmolzen und zu kugelförmigen Pulvern verfestigt, die sich ideal für AM-Verfahren eignen
Mehrere Zyklen Sinter-Crush
- Die Pulver werden wiederholt bei hohen Temperaturen verdichtet, zerkleinert und gesiebt, um die Pulververteilung zu verfeinern - ideal für die MIM-Verarbeitung
Mechanisches Legieren
- Kugelmahlen von elementaren Metallpulvern erzeugt nanodisperse Partikel- und Clusterverteilungen in ODS-Legierungen
Carbonyl-Raffination
- Herstellung von Metallpulvern mit extrem hohem Reinheitsgrad, wenn kostengünstigere Produktionsmethoden zu Verunreinigungen führen
Vergleich der Produktionsmethoden
Methode | Reinheitsgrade | Sauerstoffgehalt | Morphologie-Optionen | Durchsatz (Tonnen/Jahr) |
---|---|---|---|---|
Gaszerstäubung | Mäßig | <1000 ppm | Meist kugelförmig | Hoch >20.000 |
Wasserzerstäubung | Niedrig | 2000-4000 ppm | Unregelmäßig | Sehr hoch >50.000 |
Plasma-Sphäroidisierung | Mittel | 500-2000 ppm | Sphärisch | Niedrig <5.000 |
Mechanisches Legieren | Hoch | <1500 ppm | Variable Partikelformen | Niedrige Hunderte |
Carbonyl-Verfahren | Extrem hoch | <200 ppm | Kugelförmig/knotig | Hoch >25.000 |
Methoden zur Charakterisierung
Für die Qualifizierung von Hochtemperatur-Pulverlegierungen sind mehrere Analysemethoden unerlässlich:
Chemische Zusammensetzung
- Spektrografische und nasschemische Verfahren identifizieren Elementbestandteile und -mengen, die für die Überprüfung des Legierungsdesigns erforderlich sind.
- Kohlenstoff-, Schwefel-, Sauerstoff- und Stickstoffgehalte zeigen prozessbedingte Verunreinigungen, die die Materialleistung beeinträchtigen
Partikelgröße und Morphologie
- Laserbeugungs-Partikelgrößenanalysatoren bestimmen die vollständige Granulometrie von 10 nm bis 3 mm Größe
- Die REM-Bildgebung visualisiert Form, Oberflächenmerkmale, Satellitenpartikel und Porosität, was für die Beurteilung der Eignung des Herstellungsprozesses und die Fehleranalyse nützlich ist.
Krystallographie
- XRD zeigt vorhandene Phasen, Ausscheidungszustände, quantitative Analyse der kristallinen Eigenschaften
- Bewertet die Auswirkungen der thermischen Exposition auf die Phasenanteile anhand der mikrostrukturellen Entwicklung
Prüfung der Pulvereigenschaften
- Hall-Flowmetrie, Schüttdichte und Kompressibilität quantifizieren das Verhalten des Pulvers für eine einfache Handhabung und Konsolidierung
Anwendungen und Einsatzmöglichkeiten von Hochtemperaturpulvern
Anwendungsbereich | Pulvertyp (Beispiele) | Verwendete Schlüsseleigenschaften | Vorteile |
---|---|---|---|
Additive Fertigung von Metall (AM) | Gasverdüste Nickelsuperlegierungen, wasserverdüste nichtrostende Stähle | - Sphärische Morphologie für gute Fließfähigkeit - Enge Größenverteilung für gleichmäßige Ablagerung - Hochtemperaturleistung für den Bau von Funktionsteilen | - Ermöglicht die Herstellung komplexer, endkonturnaher Bauteile - Maßgeschneiderte Materialeigenschaften für spezifische Anwendungen - Weniger Abfall im Vergleich zur traditionellen subtraktiven Fertigung |
Magnetische Hochleistungskomponenten | Carbonyl-Eisenpulver, elektrolytisches Eisenpulver | - Hohe Reinheit für geringe Energieverluste - Sphärische Morphologie für gute Kerndichte - Weichmagnetische Eigenschaften für effiziente Energieübertragung | - Verbesserter Wirkungsgrad in Transformatoren, Drosseln und Motoren - Geringere Betriebstemperaturen und Geräuschpegel - Miniaturisierung von Geräten aufgrund besserer magnetischer Leistung |
Hochtemperatur-Löten | Wasserverdampftes Eisenpulver, gasverdampfte Nickellegierungen | - Kontrollierter Schmelzpunkt für das Löten verschiedener Materialien - Vorhandensein von Oxiden (in einigen Pulvern) für eine bessere Benetzung und Bindung - Hohe Temperaturfestigkeit für robuste Verbindungen | - Verbinden unterschiedlicher Metalle und Legierungen - Erstellen starker, lecksicherer Dichtungen in rauen Umgebungen - Anwendungen in der Luft- und Raumfahrt, der Automobilindustrie und der Energieerzeugung |
Thermisch gespritzte Beschichtungen | Wasserverdüste Aluminiumlegierungen, gasverdüste Nickelsuperlegierungen | - Breites Spektrum an Schmelzpunkten für vielfältige Beschichtungsanwendungen - Unregelmäßige Partikelformen für mechanische Verzahnung - Hohe Temperaturbeständigkeit zum Schutz von Substraten | - Verbesserte Verschleiß- und Korrosionsbeständigkeit - Wärmedämmung - Wiederherstellung verschlissener Komponenten - Anwendungen in Motoren, Turbinen und Wärmetauschern |
Metall-Spritzgießen (MIM) | Wasserverdüste Stähle, vorlegierte Pulver | - Feine Partikelgröße für komplizierte Teilegeometrien - Gute Fließfähigkeit für gleichmäßige Formfüllung - Kontrollierte Pulvereigenschaften für Maßhaltigkeit | - Kostengünstige Herstellung komplexer, endkonturnaher Metallteile - Hohe Festigkeit und Dichte erreichbar - Anwendungen in der Automobil-, Medizin- und Elektronikindustrie |
Katalytische Anwendungen | Carbonyl-Eisenpulver, gas-atomisierte Übergangsmetalle | - Hohe Oberfläche für effiziente katalytische Reaktionen - Kontrollierte Porenstruktur für selektive Katalyse - Maßgeschneiderte Partikelmorphologie für verbesserte Katalysatoraktivität | - Emissionskontrolle in Kfz-Abgassystemen - Chemische Verarbeitungsreaktionen - Herstellung sauberer Kraftstoffe und erneuerbarer Energien |
Spezifikationen und Qualitäten
Hochtemperatur-Pulverlegierungen müssen Mindestanforderungen in Bezug auf Chemie, Sauberkeit, Partikelmerkmale und Eigenschaften erfüllen:
Merkmal | Beschreibung | Wichtige Überlegungen |
---|---|---|
Materialzusammensetzung | Hochtemperaturpulver gibt es in einer Vielzahl von Materialien, die jeweils unterschiedliche Eigenschaften für bestimmte Anwendungen aufweisen. Zu den gängigen Materialien gehören: Nickel-Basis-Legierungen: Sie bieten eine außergewöhnliche Oxidationsbeständigkeit und Hochtemperaturfestigkeit und sind ideal für Triebwerkskomponenten, Wärmetauscher und Gasturbinenteile. Legierungen auf Kobaltbasis: Sie sind für ihre Verschleißfestigkeit und Hitzestabilität bekannt und werden häufig für Schneidwerkzeuge, Turbinenschaufeln und biomedizinische Implantate verwendet. Nichtrostende Stähle: Sie bieten ein ausgewogenes Verhältnis von Korrosionsbeständigkeit und Hochtemperaturleistung und eignen sich für Abgaskrümmer, Kessel und Lebensmittelverarbeitungsanlagen. Werkzeugstähle: Sie bieten eine außergewöhnliche Härte und Verschleißfestigkeit bei hohen Temperaturen und eignen sich perfekt für Formen, Matrizen und Stanzen. Feuerfeste Keramiken: Bietet hervorragende Wärmedämmungseigenschaften und wird häufig in Ofenauskleidungen, Tiegeln und Raketendüsen verwendet. |
Die Auswahl des Materials hängt vom geplanten Anwendungsfall ab. Berücksichtigen Sie Faktoren wie Spitzenbetriebstemperatur, gewünschte mechanische Eigenschaften (Festigkeit, Verschleißfestigkeit), Oxidationsbeständigkeit und Kompatibilität mit der Umgebung. |
Partikelgröße und -verteilung | Die Größe und Verteilung der Pulverpartikel haben einen erheblichen Einfluss auf den Anwendungsprozess und die Eigenschaften des Endprodukts. Feinere Pulver (10-45 Mikrometer): Verbessert die Oberflächengüte und erzeugt dünne, glatte Beschichtungen. Gut geeignet für die elektrostatische Sprühabscheidung und Wirbelschichtanwendungen. Gröbere Pulver (45-150 Mikrometer): Bieten eine bessere Fließfähigkeit und können dickere Beschichtungen erzeugen. Besser geeignet für Press- und Sintertechniken. |
Die Partikelgröße ist entscheidend für das Erreichen der gewünschten Schichtdicke und Ästhetik. Eine ausgewogene Verteilung gewährleistet eine effiziente Anwendung und minimiert den Abfall. |
Fließfähigkeit | Die Fließfähigkeit des Pulvers ist entscheidend für eine gleichmäßige Anwendung und einen effizienten Einsatz. Pulver mit guter Fließfähigkeit ermöglichen eine reibungslose Zuführung in Sprühpistolen und Trichter, wodurch Verklumpungen und Verstopfungen minimiert werden. | Eine unzureichende Fließfähigkeit kann zu Unregelmäßigkeiten in der Anwendung, ungleichmäßigen Beschichtungen und Produktionsverzögerungen führen. Hersteller verwenden oft Zusatzstoffe oder passen die Partikelgrößenverteilung an, um die Fließfähigkeit zu optimieren. |
Scheinbare Dichte | Dies bezieht sich auf das Gewicht des Pulvers pro Volumeneinheit und wirkt sich auf Faktoren wie Lagerbedarf, Trichterkapazität und Beschichtungsstärke aus. * Pulver mit hoher Schüttdichte: Sie bieten Vorteile in Bezug auf eine effiziente Lagerung und benötigen möglicherweise weniger Material, um eine bestimmte Schichtdicke zu erreichen. * Pulver mit geringer Schüttdichte: Benötigen zwar größere Lagerräume, sind aber einfacher zu handhaben und erzeugen dickere Beschichtungen mit einem einzigen Auftrag. | Die scheinbare Dichte beeinflusst die Materialhandhabung, den Lagerbedarf und die Effizienz der Beschichtung. Die Auswahl der richtigen Dichte hängt von den Anwendungsanforderungen und der verfügbaren Ausrüstung ab. |
Schmelzpunkt und Wärmeausdehnung | Der Schmelzpunkt bestimmt die maximal nutzbare Temperatur des Pulvers, während die thermische Ausdehnung die Maßänderungen beim Erhitzen bestimmt. * Pulver mit hohem Schmelzpunkt: Sie können extremen Temperaturen standhalten und eignen sich daher für anspruchsvolle Anwendungen wie Komponenten von Raketentriebwerken. * Pulver mit geringer Wärmeausdehnung: Minimierung von Maßänderungen während der Heizzyklen, was für die Einhaltung präziser Toleranzen in Hochtemperaturumgebungen entscheidend ist. | Die Kenntnis dieser Eigenschaften ist von entscheidender Bedeutung, um sicherzustellen, dass das Pulver die vorgesehene Betriebstemperatur ohne Beeinträchtigung der Funktionalität oder der Formstabilität übersteht. |
Korrosionsbeständigkeit | Die Fähigkeit des Pulvermaterials, dem Abbau durch Umwelteinflüsse wie Oxidation oder chemische Angriffe zu widerstehen, ist entscheidend für die langfristige Leistungsfähigkeit. Hoch korrosionsbeständige Pulver: Behalten ihre Integrität in rauen Umgebungen, ideal für Anwendungen, die Chemikalien, hoher Luftfeuchtigkeit oder Salznebel ausgesetzt sind. Niedrigere korrosionsbeständige Pulver: Möglicherweise sind zusätzliche Oberflächenbehandlungen oder Schutzbeschichtungen für eine längere Lebensdauer erforderlich. |
Die Wahl der Korrosionsbeständigkeit hängt von den voraussichtlichen Expositionsbedingungen ab. Die Wahl eines hoch korrosionsbeständigen Pulvers kann die Lebensdauer des Endprodukts verlängern. |
Kostenanalyse von Hochtemperaturpulvern
Faktor | Beschreibung | Auswirkungen auf die Kosten |
---|---|---|
Material Typ | Wie bereits erwähnt, gibt es Hochtemperaturpulver aus verschiedenen Materialien, die jeweils unterschiedliche Preise haben. Nickel-Basis-Legierungen: Aufgrund ihrer außergewöhnlichen Hochtemperaturleistung und der komplexen Herstellungsverfahren sind sie in der Regel am teuersten. Legierungen auf Kobaltbasis: Sie liegen oft in einer ähnlichen Preisspanne wie Nickelbasislegierungen, können aber je nach spezifischem Kobaltgehalt und gewünschten Eigenschaften variieren. Nichtrostende Stähle: Sie sind in der Regel preiswerter als Nickel- oder Kobaltlegierungen und bieten ein ausgewogenes Verhältnis zwischen Kosten und Leistung. Werkzeugstähle: Die Kosten können je nach den spezifischen Legierungselementen und den gewünschten Eigenschaften variieren. Im Allgemeinen weniger teuer als Optionen auf Nickel- oder Kobaltbasis. Feuerfeste Keramiken: Einige feuerfeste Keramiken weisen zwar eine ausgezeichnete Hitzebeständigkeit auf, sind aber relativ preiswert, insbesondere gängige Materialien wie Tonerde. Spezialisierte oder hochreine Keramiken können jedoch erheblich teurer sein. |
Die Materialauswahl hat einen erheblichen Einfluss auf die Gesamtkosten des Projekts. Bewerten Sie sorgfältig die Leistungsanforderungen im Vergleich zu den Budgeteinschränkungen. |
Pulverreinheit | Der Reinheitsgrad eines Hochtemperaturpulvers wirkt sich direkt auf seine Eigenschaften und seinen Preis aus. Hochreine Pulver: Sie bieten überlegene Leistungsmerkmale wie erhöhte Festigkeit, verbesserte Oxidationsbeständigkeit und besseres Sinterverhalten. Aufgrund der komplexen Reinigungsprozesse sind sie jedoch mit hohen Kosten verbunden. Pulver mit geringerem Reinheitsgrad: Kann für einige Anwendungen ausreichen, bei denen die Maximierung der Leistung nicht entscheidend ist. Diese Pulver sind in der Regel kostengünstiger. |
Berücksichtigen Sie die Abwägung zwischen der gewünschten Leistung und der Kosteneffizienz. In einigen Fällen kann eine geringfügige Verringerung der Reinheit akzeptabel sein, wenn sie zu erheblichen Kosteneinsparungen führt. |
Partikelgröße und -verteilung | Die Größe und Verteilung der Pulverpartikel kann sowohl die Materialkosten als auch die Verarbeitungskosten beeinflussen. Feinere Pulver: Sie erfordern in der Regel komplexere und energieintensivere Herstellungsverfahren, was zu höheren Kosten pro Gewichtseinheit führt. Grobkörnigere Pulver: Sie sind zwar potenziell kostengünstiger in der Herstellung, erfordern aber möglicherweise zusätzliche Verarbeitungsschritte (z. B. Mahlen), um die gewünschte Partikelgrößenverteilung für bestimmte Anwendungen zu erreichen, was einen Teil des anfänglichen Kostenvorteils zunichte machen könnte. |
Die Optimierung der Partikelgröße für die gewählte Anwendung kann dazu beitragen, ein Gleichgewicht zwischen Material- und Verarbeitungskosten herzustellen. |
Mindestbestellmenge (MOQ) | Viele Lieferanten legen Mindestbestellmengen (MOQ) für Hochtemperatur-Pulver fest. Große MOQs: Kann zu erheblichen Vorlaufkosten führen, insbesondere bei weniger häufig verwendeten oder speziellen Pulvern. Kleinere MOQs: Aufgrund des höheren Verwaltungs- und Bearbeitungsaufwands für kleinere Chargen kann es zu einem höheren Preis erhältlich sein. |
Berücksichtigen Sie die Projektanforderungen und das Potenzial für Verschwendung. Wenn eine große Mindestbestellmenge nicht voll ausgeschöpft wird, sollten Sie nach alternativen Lieferanten suchen, die kleinere Mengen anbieten, oder mit anderen Nutzern zusammenarbeiten, um eine größere Bestellung zu teilen. |
Reputation und Standort des Lieferanten | Der Ruf des Pulverlieferanten wirkt sich erheblich auf die Kosten und den Gesamterfolg des Projekts aus. Seriöse Anbieter: Führen Sie strenge Qualitätskontrollmaßnahmen ein, um gleichbleibende Materialeigenschaften zu gewährleisten und das Risiko zu minimieren, unbrauchbare Pulver zu erhalten. Diese Zuverlässigkeit kann einen hohen Preis haben. Weniger etablierte Anbieter: Sie bieten zwar niedrigere Preise an, verfügen aber möglicherweise nicht über strenge Qualitätskontrollverfahren, was zu höheren Ablehnungsquoten oder uneinheitlichen Leistungen führen kann. |
Bewerten Sie sorgfältig die Qualifikationen der Lieferanten und geben Sie gleichbleibender Qualität den Vorzug vor möglicherweise niedrigeren Anschaffungskosten. |
Vorlaufzeit der Lieferung | Die Zeit, die für die Lieferung des Pulvers benötigt wird, kann den Zeitplan des Projekts beeinflussen und sich möglicherweise auf die Kosten auswirken. Kürzere Vorlaufzeiten: Möglicherweise ist ein beschleunigter Versand erforderlich, der teurer sein kann. Längere Vorlaufzeiten: Sie können kostengünstiger sein, erfordern aber eine sorgfältige Planung und Bestandsverwaltung, um Produktionsverzögerungen zu vermeiden. |
Bewerten Sie den Kompromiss zwischen Kosten und Projektzeitplan. Wenn die Vorlaufzeiten kritisch sind, prüfen Sie die Möglichkeiten eines beschleunigten Versands oder eines Pufferlagers, um mögliche Verzögerungen zu vermeiden. |
Vor- und Nachteile von Hochtemperatur-Eisenlegierungen
Merkmal | Vorteil | Nachteil |
---|---|---|
Kosten-Wirksamkeit | Im Vergleich zu anderen Hochtemperaturwerkstoffen wie Superlegierungen auf Nickel- oder Kobaltbasis bieten Eisenbasislegierungen einen erheblichen Kostenvorteil. Eisen ist ein leicht verfügbares Element, so dass diese Legierungen in der Regel kostengünstiger herzustellen sind. | Obwohl sie kostengünstig sind, erreichen Hochtemperatur-Eisenlegierungen nicht immer das gleiche Leistungsniveau wie einige Optionen auf Nickel- oder Kobaltbasis in Bezug auf die Spitzenbetriebstemperatur oder spezifische mechanische Eigenschaften. |
Oxidationsbeständigkeit | Bestimmte Eisenlegierungen können bei moderaten Temperaturen (bis etwa 700 °C) eine gute Oxidationsbeständigkeit aufweisen. Legierungselemente wie Chrom und Aluminium tragen zur Bildung einer schützenden Oxidschicht bei, die eine weitere Oxidation verhindert. | Die Oxidationsbeständigkeit von Eisenlegierungen ist im Allgemeinen geringer als die von Superlegierungen auf Nickel- oder Kobaltbasis, die ihre Integrität bei viel höheren Temperaturen aufrechterhalten können. Eisenlegierungen erfordern möglicherweise zusätzliche Oberflächenbehandlungen oder Beschichtungen, um die Lebensdauer in stark oxidierenden Umgebungen zu verlängern. |
Festigkeit & Kriechwiderstand | Einige Eisenlegierungen können zwar nicht mit den Spitzenreitern mithalten, bieten aber eine ausreichende Festigkeit und Kriechbeständigkeit bei erhöhten Temperaturen. Bestimmte Legierungselemente wie Molybdän und Vanadium können diese Eigenschaften verbessern, wodurch sie sich für verschiedene industrielle Anwendungen eignen. | Die Hochtemperaturfestigkeit und Kriechbeständigkeit von Eisenlegierungen ist in der Regel geringer als die von Superlegierungen auf Nickel- oder Kobaltbasis. Für Anwendungen, die eine außergewöhnliche Leistung bei extremen Temperaturen erfordern, können andere Materialoptionen erforderlich sein. |
Schweißbarkeit & Bearbeitbarkeit | Eisenbasislegierungen lassen sich im Vergleich zu einigen anderen Hochtemperaturwerkstoffen im Allgemeinen gut schweißen und bearbeiten. Dies führt zu einer einfacheren Herstellung und niedrigeren Gesamtbearbeitungskosten. | Obwohl Eisenlegierungen schweißbar und bearbeitbar sind, erfordern sie unter Umständen spezielle Schweißtechniken oder Bearbeitungsverfahren, um eine Beeinträchtigung ihrer Eigenschaften an der Schweißnaht oder das Einbringen von Bearbeitungsspannungen zu vermeiden. |
Wiederverwertbarkeit | Eisen ist eines der am häufigsten recycelten Metalle weltweit. Hochwarmfeste Eisenlegierungen können am Ende ihrer Lebensdauer recycelt werden, was die Umweltauswirkungen minimiert und ein gewisses Maß an materieller Nachhaltigkeit bietet. | Das Recyclingverfahren für komplexe Eisenlegierungen kann im Vergleich zu reinem Eisen aufwendiger sein, und Faktoren wie Legierungselemente und Oberflächenverunreinigungen können die Recyclingfähigkeit beeinflussen. |
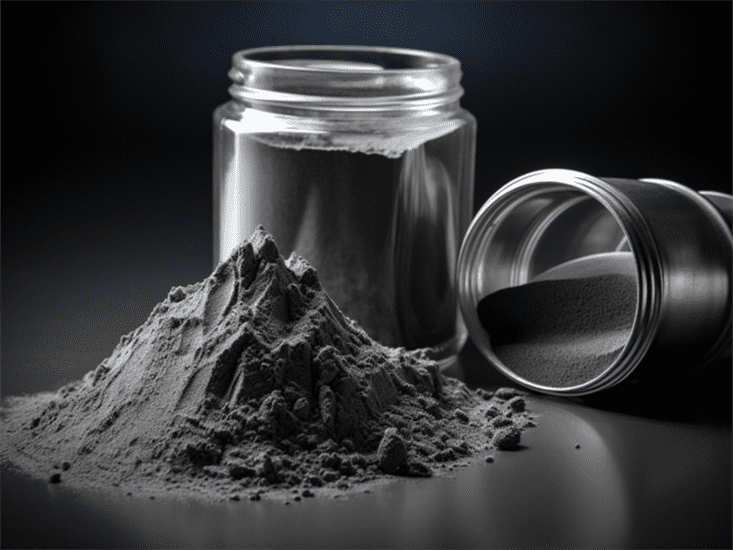
FAQs
F: Wie sieht die typische Partikelgrößenverteilung für Hochtemperatur-Edelstahlpulver in der Metall-AM aus?
A: Bei Pulverbettschmelzverfahren wie dem selektiven Laserschmelzen (SLM) und dem Elektronenstrahlschmelzen (EBM) liegt der übliche Bereich bei Größenfraktionen von 15 μm bis 45 μm. Feinere Verteilungen können die Auflösung verbessern, beeinträchtigen aber die Ausbreitung des Pulvers während der Schichtabscheidung und verringern die Fließeigenschaften.
F: Welche Kühlraten bei der Gaszerstäubung erhalten die optimale Zusammensetzung des Legierungspulvers?
A: Um die beste Kombination aus chemischer Retention und geeigneter Pulvermorphologie zu erreichen, werden für Hochtemperaturpulver aus rostfreiem Stahl und Superlegierungen häufig Erstarrungsgeschwindigkeiten zwischen 1000 und 3000°C pro Sekunde verwendet.
F: Warum ist ein hoher Gehalt an Oxidpartikeln in Hochtemperatur-Eisenlegierungen schädlich?
A: Während des Betriebs können vorhandene Oxide vergröbern und wandern und weniger schützende und weniger stabile Oxidpopulationen bilden, was zu einem beschleunigten Angriff durch oxidierende, sulfidierende, aufkohlende oder chlorierende Umgebungen führt und die Lebensdauer der Komponenten verkürzt. Bei der Entwicklung von Legierungen ist eine sorgfältige Bestimmung und Kontrolle des Sauerstoffgehalts auf der Grundlage der maximalen Expositionstemperaturen und Betriebsbedingungen erforderlich.
F: Welche Methoden können verwendet werden, um die Pulverdichte auf einen theoretischen Wert von >95% zu erhöhen?
A: Heißisostatisches Pressen wird üblicherweise bei Bauteilen aus Hochtemperatur-Edelstahl oder Superlegierungen nach der ersten AM- oder MIM-Fertigung angewandt, um Restporen zu beseitigen und eine Materialleistung zu erzielen, die der von Knetlegierungen in denselben verstärkten Wärmebehandlungszuständen nahe kommt. Nahezu theoretische Dichten sorgen für mechanische Robustheit.
F: Warum ist eine Stickstoffkontrolle unter 1000 ppm bei hochfesten Kupferlegierungen mit hoher Leitfähigkeit so wichtig?
A: Bei der Stickstoffaufnahme bilden sich sehr harte, spröde Nitridphasen, die die thermische und elektrische Leitfähigkeit drastisch herabsetzen und damit die Funktionalität von Wärmemanagementanwendungen verringern. Gleichzeitig wird die Formbarkeit und Duktilität bei der Herstellung verringert.