Haben Sie schon einmal die schiere Kraft und Effizienz eines Düsentriebwerks bestaunt, das plötzlich zum Leben erwacht? Der unermüdliche Schub, der Flugzeuge über Kontinente hinweg treibt, oder die unglaubliche Energieerzeugung industrieller Gasturbinen – all das ist einer Symphonie sorgfältig konstruierter Komponenten zu verdanken. Doch in diesen Wunderwerken der Technik verbirgt sich eine geheime Zutat: Pulver für die Gasturbinentechnik. Diese feinen Metallpartikel spielen bei der Herstellung des Herzstücks dieser Motoren – den Turbinenscheiben und -schaufeln – eine entscheidende Rolle.
Stellen Sie sich ein winziges, metallisches Universum vor. Jedes Pulverteilchen in der Gasturbinentechnik ist ein mikroskopischer Krieger, der speziell dafür entwickelt wurde, der brutalen Umgebung in einer Gasturbine standzuhalten. Hier vereinen sich glühende Temperaturen, enormer Druck und unerbittliche Zentrifugalkräfte und schaffen ein Schlachtfeld für Materialien. Und hier kommen diese speziell formulierten Pulver ins Spiel, die eine einzigartige Kombination aus Festigkeit, Hitzebeständigkeit und Ermüdungsbeständigkeit bieten – die heilige Dreifaltigkeit für Gasturbinenkomponenten.
Pulver für die Gasturbinentechnik sind jedoch keine Universallösung. So wie ein Meisterkoch nicht für jedes Gericht dasselbe Gewürz verwenden würde, haben Ingenieure eine Vielzahl von Pulvertypen entwickelt, jeder mit seinen eigenen, auf bestimmte Anwendungen zugeschnittenen Eigenschaften. Lassen Sie uns tiefer eintauchen und dieses faszinierende Reich metallischer Wunder erkunden.
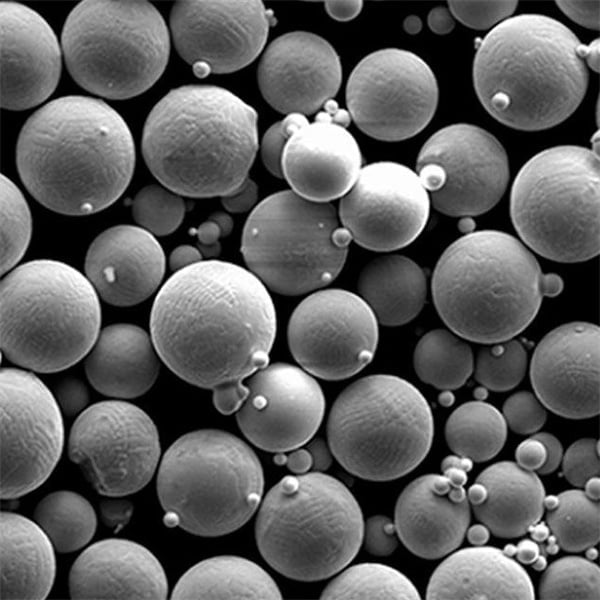
Merkmale von Pulver für die Gasturbinentechnik
Charakteristisch | Beschreibung |
---|---|
Materialzusammensetzung | Hauptsächlich Superlegierungen auf Nickelbasis, können aber auch Kobalt- und Eisenlegierungen enthalten |
Partikelgröße und -verteilung | Sorgfältig kontrolliert, um Packungsdichte und mechanische Eigenschaften zu optimieren. Typischerweise im Bereich von 10 bis 150 Mikrometer |
Form | Sphärisch für optimale Strömung und Packung während der Konsolidierung |
Fließfähigkeit | Spielt eine entscheidende Rolle bei additiven Fertigungsprozessen. Pulver sind für einen gleichmäßigen, konstanten Fluss ausgelegt |
Reinheit | Eine strikte Kontrolle von Verunreinigungen wie Sauerstoff, Kohlenstoff und Schwefel ist für eine optimale Leistung unerlässlich |
Eine Galerie kraftvoller Pulver
Lernen wir nun einige der wichtigsten Akteure im Bereich der Pulver für die Gasturbinentechnik kennen:
- IN718: Ein Hochleistungsmaterial, das für sein ausgezeichnetes Gleichgewicht aus Festigkeit, Zähigkeit und Verarbeitbarkeit bekannt ist. Es ist ein Allrounder, der sich für eine Vielzahl von Gasturbinenanwendungen eignet.
- Rene 41: Diese Hochleistungslegierung zeichnet sich durch eine überragende Kriechfestigkeit bei erhöhten Temperaturen aus und ist daher ideal für heiße Turbinenteile. Stellen Sie sie sich als feuerfesten Kämpfer vor, der der sengenden Hitze standhält.
- CMS 247LC: Diese Superlegierung auf Nickelbasis bietet eine außergewöhnliche Beständigkeit gegen Oxidation und Heißkorrosion. Stellen Sie es sich als Schildträger vor, der den unerbittlichen Angriff heißer Gase abwehrt.
- Mar-M 247: Dieses leistungsstarke Material glänzt bei Anwendungen, die hohe Festigkeit und Kriechfestigkeit bei sehr hohen Temperaturen erfordern. Es ist der ultimative Gladiator, der auch in den härtesten Umgebungen gedeiht.
- AM 1624: Diese moderne Legierung ist relativ neu und wurde speziell für additive Fertigungsverfahren wie den 3D-Druck entwickelt. Stellen Sie sie sich als technisch versierten Krieger vor, der im Kampf um Leistung die neueste Technologie einsetzt.
- Astrologie: Diese Superlegierung auf Kobaltbasis bietet außergewöhnliche Hochtemperaturfestigkeit und Oxidationsbeständigkeit. Betrachten Sie sie als den Champion in extremen Umgebungen, der die Grenzen des Möglichen erweitert.
- DZ 125: Diese Superlegierung auf Eisenbasis stellt eine kostengünstige Alternative für Anwendungen dar, bei denen es nicht nur auf die ultimative Leistung ankommt. Sie ist ein strategischer General und bietet ein gutes Gleichgewicht zwischen Wert und Leistungsfähigkeit.
- SRene 10X: Diese nickelbasierte Superlegierung zeichnet sich durch eine außergewöhnliche Beständigkeit gegen Ermüdung bei niedriger Lastspielzahl aus und ist daher ideal für Komponenten, die wiederholten Belastungszyklen ausgesetzt sind. Stellen Sie sie sich als unermüdlichen Krieger vor, der die ständige Belastung des Betriebs aushält.
- PWA 1430: Diese moderne Legierung bietet überragende Kriechfestigkeit und Hochtemperaturfestigkeit. Stellen Sie sie sich als hochmodernen Soldaten vor, ausgestattet mit den neuesten Erkenntnissen der Materialwissenschaft.
- Rene N5: Diese Superlegierung auf Nickelbasis ist für ihre hervorragende Beständigkeit gegen thermische Ermüdung und Kriechen bekannt. Stellen Sie sie sich als anpassungsfähigen Krieger vor, der unter unterschiedlichen Temperaturbedingungen gute Leistungen erbringt.
Vorteile von Pulvern für die Gasturbinentechnik
Vorteil | Beschreibung | Nutzen Sie |
---|---|---|
Verbesserte Materialeigenschaften | Pulver für die Gasturbinentechnik werden durch sorgfältig kontrollierte Prozesse wie Gaszerstäubung hergestellt, wodurch Pulver mit außergewöhnlicher Reinheit, Korngrößenverteilung und sphärischer Morphologie entstehen. Diese präzise entwickelten Pulver können zur Herstellung von Komponenten mit überlegener Festigkeit, Kriechfestigkeit, Ermüdungsbeständigkeit und Hochtemperaturleistung im Vergleich zu konventionell gegossenen Komponenten verwendet werden. | Dies führt zu einer höheren Effizienz und Haltbarkeit von Gasturbinentriebwerken. Stärkere Komponenten können höheren Betriebstemperaturen und -drücken standhalten, was zu einer verbesserten Kraftstoffeffizienz und Leistungsabgabe führt. Darüber hinaus ermöglicht die verbesserte Kriechfestigkeit eine längere Lebensdauer, bevor Komponenten ausgetauscht werden müssen, was die Wartungskosten senkt. |
Flexibilität bei der Gestaltung | Pulverbasierte Fertigungsverfahren wie die additive Fertigung (AM), auch als 3D-Druck bekannt, eröffnen neue Möglichkeiten für das Design von Gasturbinen. Im Gegensatz zu herkömmlichen Gussverfahren, die durch die Formgeometrie eingeschränkt sind, ermöglicht die additive Fertigung die Erstellung komplexer Innenmerkmale und komplizierter Gitterstrukturen. Diese Designfreiheit ermöglicht es Ingenieuren, das Komponentengewicht für eine bessere Kraftstoffeffizienz zu optimieren und Komponenten mit überlegenen Kühlkanälen für ein verbessertes Wärmemanagement zu erstellen. | Diese Flexibilität fördert Innovationen im Gasturbinendesign und erweitert die Grenzen von Leistung und Effizienz. Optimierte Komponenten können zu leichteren Motoren für Flugzeuganwendungen oder kompakteren Designs für die industrielle Stromerzeugung führen. |
Materialnutzung | Pulverbasierte Fertigungsverfahren zeichnen sich im Vergleich zu herkömmlichen Gussverfahren durch minimalen Materialabfall aus. Beim Gießen geht beim Anguss und beim Entfernen der Angusskanäle viel Material verloren. Bei AM hingegen kann ungenutztes Pulver recycelt und wiederverwendet werden, wodurch Materialabfall und Produktionskosten minimiert werden. | Dieser Vorteil fördert die Nachhaltigkeit bei der Herstellung von Gasturbinen. Ein geringerer Materialverbrauch bedeutet eine geringere Umweltbelastung und entspricht den wachsenden Anforderungen an umweltfreundliche Industriepraktiken. |
Reduzierte Vorlaufzeit | Die additive Fertigung bietet erhebliche Vorteile hinsichtlich der Vorlaufzeit bei der Herstellung komplexer Gasturbinenkomponenten. Da bei der additiven Fertigung keine komplexen Formen mehr hergestellt werden müssen, sind im Vergleich zu herkömmlichen Gussverfahren schnellere Durchlaufzeiten möglich. Diese Fähigkeit zum Rapid Prototyping ist für die effiziente Entwicklung und Erprobung neuer Gasturbinendesigns von entscheidender Bedeutung. | Dies führt zu schnelleren Entwicklungszyklen und einer schnelleren Markteinführung neuer und verbesserter Gasturbinentechnologien. Diese Agilität ist insbesondere für die Luft- und Raumfahrtindustrie von Vorteil, in der schnelle Innovationen von entscheidender Bedeutung sind. |
Maßgeschneiderte Materialeigenschaften | Pulvermetallurgieverfahren ermöglichen die Herstellung neuartiger Werkstoffe mit Eigenschaften, die speziell auf Gasturbinenanwendungen zugeschnitten sind. Durch die genaue Kontrolle der Zusammensetzung und Verteilung der Elemente in den Pulverpartikeln können Ingenieure Werkstoffe mit optimierten Kombinationen aus Festigkeit, Duktilität und Oxidationsbeständigkeit herstellen. | Dieser gezielte Ansatz bei der Werkstoffkonstruktion ermöglicht die Entwicklung von Gasturbinenkomponenten, die den immer höheren Anforderungen bei Betriebstemperaturen und -drücken standhalten. Darüber hinaus eröffnet er Möglichkeiten zur Erforschung neuer Werkstoffkombinationen, die mit herkömmlichen Gussverfahren möglicherweise nicht realisierbar sind. |
Konforme Kühlung | Die additive Fertigung ermöglicht die Erstellung komplexer interner Kühlkanäle in Gasturbinenkomponenten. Diese Kanäle können so gestaltet werden, dass sie der exakten Geometrie der Komponente entsprechen, wodurch eine optimale Wärmeübertragung gewährleistet und thermische Gradienten reduziert werden. Diese präzise Kühlstrategie minimiert das Risiko von Hot Spots und thermischer Verformung und führt zu einer verbesserten Leistung und Lebensdauer der Komponente. | Dies führt zu einem effizienteren Betrieb und einer zuverlässigeren Leistung der Gasturbinen. Durch die Aufrechterhaltung niedrigerer Komponententemperaturen wird das Risiko einer Materialverschlechterung und eines Komponentenausfalls minimiert. |
Gewichtsreduzierung | Die durch AM gebotene Designfreiheit ermöglicht die Herstellung leichterer Gasturbinenkomponenten mit internen Gitterstrukturen. Diese komplexen Strukturen sorgen für die nötige Festigkeit bei minimalem Gewicht, ein entscheidender Faktor für Flugzeuggasturbinen. Leichtere Komponenten führen zu einer verbesserten Kraftstoffeffizienz und einer größeren Reichweite des Flugzeugs. | Dieser Vorteil ist besonders für die Luft- und Raumfahrtindustrie von Bedeutung, wo jedes eingesparte Kilogramm erhebliche Treibstoffeinsparungen und eine höhere Nutzlastkapazität bedeutet. Die Fähigkeit, leichte Hochleistungskomponenten herzustellen, ist ein großer Vorteil von Pulvern für die Gasturbinentechnik. |
Nachteile von Pulver für die Gasturbinentechnik
Nachteil | Beschreibung | Auswirkungen |
---|---|---|
Hohe Pulverkosten | Pulver für die Gasturbinentechnik werden häufig in komplexen und energieintensiven Verfahren wie der Gaszerstäubung hergestellt. Dies führt zu höheren Kosten pro Kilogramm im Vergleich zu konventionell hergestellten Materialien wie Knetlegierungen. Darüber hinaus tragen die strengen Qualitätskontrollanforderungen für diese Pulver weiter zu ihrem Premiumpreis bei. | Die hohen Pulverkosten können die Gesamtherstellungskosten von Gasturbinenkomponenten erheblich erhöhen. Dies kann ein großes Hindernis für eine breite Einführung darstellen, insbesondere bei kostensensiblen Anwendungen in der Stromerzeugungsindustrie. |
Komplexität der Prozesse | Additive Fertigung, die primäre Verarbeitungstechnik für Gasturbinen-Pulver, ist im Vergleich zu traditionellen Gussverfahren eine relativ neue Technologie. Obwohl AM-Prozesse Gestaltungsfreiheit bieten, können sie komplex sein und erfordern spezielles Fachwissen, um effektiv zu funktionieren. Faktoren wie Pulverauswahl, Optimierung der Laserparameter und Nachbearbeitungstechniken spielen allesamt eine entscheidende Rolle für den Erfolg des Baus. | Die Komplexität von AM-Prozessen kann Hersteller vor Herausforderungen stellen, insbesondere solche, die keine Erfahrung mit dieser Technologie haben. Eine unsachgemäße Prozesssteuerung kann zu Defekten wie Porosität, schlechten mechanischen Eigenschaften und Maßungenauigkeiten im Endprodukt führen. |
Begrenzte Baugröße | Aktuelle AM-Maschinen sind hinsichtlich der Größe der Komponenten, die sie produzieren können, begrenzt. Während großformatige AM-Maschinen in der Entwicklung sind, sind sie noch nicht weit verbreitet. Dies beschränkt die Anwendung von Gasturbinen-Pulvern auf kleinere Komponenten innerhalb eines Gasturbinentriebwerks. | Diese Einschränkung kann ein Hindernis für den Einsatz von AM bei der Herstellung großer Gasturbinenkomponenten wie Turbinenscheiben oder Brennkammerauskleidungen darstellen. Sie macht für diese größeren, kritischen Komponenten den Einsatz konventioneller Gussverfahren erforderlich. |
Handhabung von Pulver | Pulver für die Gasturbinentechnik sind häufig anfällig für Feuchtigkeit und Sauerstoffverunreinigungen. Diese Verunreinigungen können die Fließfähigkeit des Pulvers während des AM-Prozesses beeinträchtigen und zur Bildung von Defekten wie Oxiden im Endprodukt führen. Um die Pulverqualität aufrechtzuerhalten und Verunreinigungen zu vermeiden, sind strenge Handhabungsverfahren und kontrollierte Umgebungen erforderlich. | Die sorgfältigen Handhabungsanforderungen können den gesamten Herstellungsprozess komplexer und teurer machen. Um eine ordnungsgemäße Lagerung und Handhabung des Pulvers zu gewährleisten, sind möglicherweise spezielle Geräte wie Schutzgasbehälter und Luftentfeuchter erforderlich. |
Teilequalifizierung | Gasturbinenkomponenten unterliegen strengen Sicherheits- und Leistungsvorschriften. Da AM eine relativ neue Technologie ist, kann die Qualifizierung von AM-gefertigten Komponenten für den Einsatz in Gasturbinen ein anspruchsvoller und zeitaufwändiger Prozess sein. Um nachzuweisen, dass die AM-gefertigte Komponente die strengen Leistungs- und Sicherheitsstandards der Aufsichtsbehörden erfüllt, sind häufig umfangreiche Tests und Charakterisierungen erforderlich. | Der langwierige Qualifizierungsprozess kann die Einführung von AM für Gasturbinenanwendungen behindern. Hersteller könnten aufgrund der Unsicherheit und der potenziellen Verzögerungen, die mit der Komponentenqualifizierung verbunden sind, zögern, in diese Technologie zu investieren. |
Oberflächenrauhigkeit | Komponenten, die durch additive Fertigung hergestellt werden, können im Vergleich zu konventionell gegossenen Komponenten eine charakteristische Oberflächenrauheit aufweisen. Diese Oberflächenrauheit kann die aerodynamische Leistung beeinträchtigen und das Risiko der Entstehung von Ermüdungsrissen in stark beanspruchten Bereichen erhöhen. Nachbearbeitungstechniken wie Zerspanen und Polieren können zur Verbesserung der Oberflächenbeschaffenheit eingesetzt werden, jedoch fügen diese dem Herstellungsprozess zusätzliche Schritte und Kosten hinzu. | Die inhärente Oberflächenrauheit von AM-Komponenten kann für bestimmte Gasturbinenanwendungen ein Nachteil sein, insbesondere für solche mit hohen aerodynamischen Anforderungen wie Kompressorschaufeln. Die sorgfältige Berücksichtigung der Auswirkungen der Oberflächenrauheit auf die Komponentenleistung ist während der Entwurfsphase von entscheidender Bedeutung. |
Eingeschränkte Materialverfügbarkeit | Die Palette der Materialien, die derzeit als Pulver für die Gasturbinentechnik erhältlich sind, befindet sich im Vergleich zu der großen Auswahl an Knetlegierungen, die in der konventionellen Fertigung verwendet werden, noch in der Entwicklung. Diese begrenzte Materialauswahl kann die Designoptionen für Ingenieure einschränken, die die Komponentenleistung für bestimmte Anwendungen optimieren möchten. | Die eingeschränkte Materialauswahl kann eine Herausforderung darstellen, wenn es darum geht, die Grenzen der Leistung von Gasturbinen zu erweitern. Die Entwicklung neuer Pulverzusammensetzungen mit auf extreme Betriebsbedingungen zugeschnittenen Eigenschaften ist ein fortlaufender Forschungsbereich. |
Anwendungen von Pulvern für die Gasturbinentechnik
Anmeldung | Beschreibung | Nutzen Sie |
---|---|---|
Turbinenschaufeln | Die komplexen Geometrien von Turbinenschaufeln, insbesondere im Hochdruckbereich, lassen sich mithilfe von additiver Fertigung und Gasturbinen-Pulvern problemlos herstellen. Diese komplexen internen Kühlkanäle optimieren die Wärmeübertragung und verbessern die Schaufeleffizienz. Darüber hinaus ermöglicht die additive Fertigung die Erstellung von Blisk-Designs, bei denen Schaufel und Scheibe als eine Einheit hergestellt werden, was das Gewicht reduziert und die Montage vereinfacht. | Dies führt zu einer verbesserten Effizienz und Leistung des Gasturbinentriebwerks. Optimierte Kühlkanäle minimieren thermische Gradienten innerhalb der Schaufel und verringern so das Risiko von Hot Spots und thermischen Verformungen. Darüber hinaus bieten Blisk-Designs Vorteile bei der Gewichtsreduzierung, was insbesondere bei Flugzeuggasturbinen von entscheidender Bedeutung ist. |
Brennkammerauskleidungen | Die Fähigkeit, mit additiver Fertigung komplexe Innenstrukturen zu erzeugen, macht Pulver für die Gasturbinentechnik gut geeignet für Brennkammerauskleidungen. Diese Auskleidungen spielen eine entscheidende Rolle bei der Brennstoffmischung und Flammenstabilisierung in der Brennkammer. Die additive Fertigung ermöglicht die Konstruktion komplexer Verwirbelungselemente und Flammenhalter, die eine effiziente Brennstoff-Luft-Mischung fördern und Schadstoffemissionen minimieren. | Dies trägt zu einer saubereren und effizienteren Verbrennung in der Gasturbine bei. Eine präzise Steuerung der Verwirbelungs- und Flammenhaltergeometrie ermöglicht eine optimierte Brennstoff-Luft-Vermischung, was zu einer verbesserten Verbrennungseffizienz und geringeren Schadstoffemissionen wie NOx führt. |
Wärmetauscher | Aufgrund ihrer hohen Temperaturbeständigkeit und Designflexibilität eignen sich technische Pulver für Gasturbinen ideal für Wärmetauscheranwendungen in Gasturbinen. AM ermöglicht die Herstellung hocheffizienter Wärmetauscher mit komplexen Innengeometrien, die die Wärmeübertragungsfläche maximieren. Diese fortschrittlichen Wärmetauscher können den Gesamtwärmewirkungsgrad des Gasturbinenzyklus verbessern. | Dies führt zu einer höheren Leistungsabgabe und Kraftstoffeinsparungen für die Gasturbine. Die Fähigkeit, komplexe interne Strömungswege im Wärmetauscher zu schaffen, optimiert die Wärmeübertragung, was zu einer verbesserten Zykluseffizienz und einem geringeren Kraftstoffverbrauch führt. |
Leichtbauteile | Die durch AM gebotene Designfreiheit in Kombination mit dem hohen Verhältnis von Festigkeit zu Gewicht einiger Gasturbinen-Pulver ermöglicht die Herstellung von Leichtbauteilen für Gasturbinen. Dies ist insbesondere für Flugzeug-Gasturbinenmotoren von Vorteil, bei denen sich Gewichtsreduzierung direkt in verbesserter Kraftstoffeffizienz und größerer Reichweite niederschlägt. Komponenten wie Kompressorgehäuse und Strukturhalterungen können durch AM sowohl hinsichtlich Festigkeit als auch Gewicht optimiert werden. | Dies trägt zu erheblichen Treibstoffeinsparungen und einer größeren Reichweite von Flugzeugen mit Gasturbinentriebwerken bei. Die Fähigkeit, leichte Hochleistungskomponenten herzustellen, ist ein großer Vorteil für Flugzeuganwendungen. |
Fortschrittliche Kühlkonzepte | Technische Pulver für Gasturbinen ermöglichen die Herstellung moderner Kühlkanäle in Gasturbinenkomponenten. Diese Kanäle können der exakten Geometrie der Komponente entsprechen, wodurch eine optimale Wärmeübertragung gewährleistet und thermische Gradienten reduziert werden. Dies ermöglicht den Betrieb von Gasturbinen bei höheren Temperaturen und Drücken und verbessert so die Gesamteffizienz und Leistungsabgabe. | Dies erweitert die Leistungsgrenzen von Gasturbinen. Durch die Entwicklung effizienter Kühlstrategien ermöglicht AM den Einsatz moderner Materialien, die höheren Betriebstemperaturen standhalten, was zu höherer Effizienz und Leistungsabgabe führt. |
Schnelles Prototyping | Die Möglichkeit, Designs mithilfe von AM mit Gasturbinen-Pulvern schnell zu iterieren, macht es zu einem wertvollen Werkzeug für die schnelle Prototypisierung von Gasturbinenkomponenten. So können Ingenieure neue Designs schnell testen und verfeinern, bevor sie mit der Produktion im großen Maßstab beginnen. Dieser schnelle Entwicklungszyklus beschleunigt Innovationen in der Gasturbinentechnologie. | Dies verkürzt die Entwicklungszeiten und senkt die Kosten für die Markteinführung neuer Gasturbinentechnologien. Die Fähigkeit, schnell Prototypen zu erstellen und neue Designs zu testen, ist entscheidend, um in einer sich schnell entwickelnden Branche immer einen Schritt voraus zu sein. |
Reparatur kritischer Komponenten | Pulver aus der Gasturbinentechnik können zur Reparatur kritischer Gasturbinenkomponenten verwendet werden. AM ermöglicht die lokale Ablagerung von Material, um beschädigte Bereiche wiederherzustellen oder erodierte Oberflächen aufzufüllen. Dies minimiert die Notwendigkeit eines vollständigen Komponentenaustauschs und reduziert Ausfallzeiten und Wartungskosten. | Dies trägt zu längeren Betriebszeiten und geringeren Wartungskosten für Gasturbinenbetreiber bei. Die Möglichkeit, kritische Komponenten zu reparieren, verlängert deren Lebensdauer und vermeidet den Bedarf an teuren Ersatzteilen. |
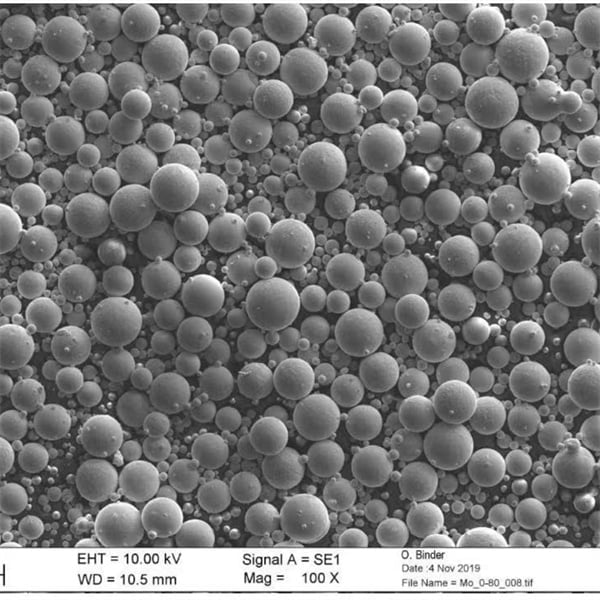
Typische Spezifikationen, Größen, Qualitäten und Standards:
Merkmal | Beschreibung |
---|---|
Materialzusammensetzung | Variiert je nach Pulvertyp. Die chemische Zusammensetzung wird normalerweise gemäß den strengen Spezifikationen der entsprechenden Normen kontrolliert. |
Partikelgröße und -verteilung | Der typische Bereich liegt zwischen 10 und 150 Mikrometer, wobei die spezifischen Bereiche von der Anwendung und den gewünschten Eigenschaften abhängen. Die Partikelgrößenverteilung wird sorgfältig kontrolliert, um eine optimale Packungsdichte zu erzielen. |
Form | Kugelförmig für optimale Strömung und Packung während Konsolidierungsprozessen. |
Fließfähigkeit | Gemessen mithilfe standardisierter Tests, um einen konsistenten und gleichmäßigen Pulverfluss während additiver Fertigungsprozesse sicherzustellen. |
Reinheit | Für eine optimale Leistung ist eine strikte Kontrolle von Verunreinigungen wie Sauerstoff, Kohlenstoff und Schwefel unerlässlich. Die Grenzwerte werden durch entsprechende Normen definiert. |
Klassen | Je nach Legierung und Hersteller können unterschiedliche Pulverqualitäten verfügbar sein. Diese Qualitäten können sich hinsichtlich der Zusammensetzung der Nebenelemente oder der Verarbeitungsparameter unterscheiden. |
Normen | Pulver für die Gasturbinentechnik entsprechen in der Regel den Industrienormen von Organisationen wie ASTM International (ASTM) oder AMS International (AMS). Diese Normen definieren Spezifikationen für Materialzusammensetzung, Partikelgröße und andere wichtige Parameter. |
Lieferanten und Preisangaben
Information | Beschreibung | Rücksichtnahme |
---|---|---|
Lieferantenlandschaft | Der Markt für technische Pulver für Gasturbinen ist relativ konzentriert und umfasst nur wenige große Akteure. Diese Unternehmen verfügen über das erforderliche Know-how und die Infrastruktur, um qualitativ hochwertige Pulver herzustellen, die den strengen Anforderungen der Gasturbinenindustrie gerecht werden. | Aufgrund der Komplexität des Produktionsprozesses und der Notwendigkeit einer strengen Qualitätskontrolle sind die Markteintrittsbarrieren für neue Lieferanten hoch. Dies kann den Wettbewerb einschränken und möglicherweise Auswirkungen auf die Preisgestaltung haben. |
Beispiele für wichtige Lieferanten | Zu den namhaften Lieferanten von Pulvern für die Gasturbinentechnik zählen: | * APEX Powder Company (USA) * Höganäs AB (Schweden) * AMETEK SMP (USA) |
Faktoren der Preisgestaltung | Die Preisgestaltung von Pulvern für die Gasturbinentechnik wird von mehreren Faktoren beeinflusst, darunter: | * Pulvermaterial: Exotische Hochleistungslegierungen sind im Vergleich zu gängigeren Superlegierungen auf Nickelbasis typischerweise teurer. * Reinheit des Pulvers: Pulver mit höherem Reinheitsgrad erzielen aufgrund der erforderlichen strengen Qualitätskontrollmaßnahmen einen höheren Preis. * Partikelgröße und Morphologie: Pulver mit feinerer Partikelgröße und sphärischer Morphologie sind in der Regel teurer in der Herstellung und können mehr kosten. * Bestellmenge: Bei größeren Bestellmengen gewähren einige Lieferanten möglicherweise Preisnachlässe. |
Zusätzliche Überlegungen | Über den Grundpreis des Pulvers hinaus sind bei der Verwendung von Pulvern aus der Gasturbinentechnik für AM weitere Kosten zu berücksichtigen: | * Mindestbestellmenge: Einige Lieferanten haben möglicherweise Mindestbestellmengen, die bei kleineren Projekten oder Prototyping-Anwendungen ein Hindernis darstellen können. * Nachbearbeitungskosten: Bei der Herstellung von Gasturbinenkomponenten mittels additiver Fertigung sind möglicherweise Nachbearbeitungsschritte wie Wärmebehandlung, Entfernung von Stützstrukturen und Oberflächenbearbeitung erforderlich, die die Gesamtherstellungskosten erhöhen. |
Markttrends | Der Markt für technische Pulver für Gasturbinen dürfte in den kommenden Jahren wachsen. Ausschlaggebend hierfür sind unter anderem die folgenden Faktoren: | * Steigende Nachfrage nach effizienteren und leistungsstärkeren Gasturbinen zur Stromerzeugung und zum Antrieb von Flugzeugen. * Fortschritte in der additiven Fertigungstechnologie erweitern die Gestaltungsmöglichkeiten für Gasturbinenkomponenten. * Zunehmender Fokus auf die Gewichtsreduzierung von Flugzeugen zur Verbesserung der Treibstoffeffizienz und Reichweite. |
Ein Blick auf die Kosten:
Es ist wichtig zu beachten, dass spezifische Preisinformationen zu Gasturbinen-Pulvern aus geschäftlichen Gründen oft nicht öffentlich verfügbar sind. Allerdings gelten diese Pulver im Vergleich zu herkömmlichen Optionen im Allgemeinen als hochwertige Materialien. Die Kosten müssen jedoch gegen die potenziellen Vorteile abgewogen werden, die sie in Bezug auf Leistung, Designflexibilität und Materialnutzung bieten.
Vergleich pulverbasierter und traditioneller Herstellungsverfahren
Bei der Herstellung von Gasturbinenkomponenten haben sich jahrzehntelang traditionelle Verfahren wie das Gießen und die Bearbeitung von Vollblöcken bewährt. Pulverbasierte Verfahren gewinnen jedoch aufgrund mehrerer Vorteile deutlich an Bedeutung:
- Überlegene Materialeigenschaften: Wie bereits erwähnt, können mit Pulvermetallurgieverfahren im Vergleich zu herkömmlichen Gussverfahren höhere Festigkeit, Dauerfestigkeit und Kriechfestigkeit erreicht werden. Dies führt zu einer höheren Effizienz und längeren Lebensdauer von Gasturbinen.
- Flexibilität bei der Gestaltung: Die additive Fertigung auf Pulverbasis ermöglicht die Herstellung komplexer Geometrien, die mit konventioneller Bearbeitung nur schwer oder gar nicht zu erreichen sind. Dies öffnet Türen für innovative und effizientere Turbinendesigns, wie etwa Komponenten mit internen Kühlkanälen oder leichteren Strukturen.
- Verbesserte Materialausnutzung: Pulverbasierte Verfahren verursachen im Vergleich zu herkömmlichen Methoden wie der Bearbeitung aus massiven Blöcken nur minimalen Materialabfall. Dies führt zu Kosteneinsparungen und einer geringeren Umweltbelastung.
- Near-Net-Shape Manufacturing: Pulverbasierte additive Fertigungstechniken können Komponenten mit nahezu endkonturierten Formen erzeugen, die im Vergleich zu herkömmlichen Methoden nur eine minimale Nachbearbeitung erfordern. Dies führt zu schnelleren Produktionszeiten und geringeren Kosten.
Traditionelle Methoden haben jedoch auch ihre eigenen Vorteile:
- Geringere Vorlaufkosten: Die Einrichtung herkömmlicher Fertigungsprozesse erfordert im Vergleich zu pulverbasierten additiven Fertigungsanlagen typischerweise eine geringere Anfangsinvestition.
- Etablierte Prozesse: Traditionelle Methoden gibt es schon seit Jahrzehnten, und die Prozesse sind gut etabliert und verstanden. Dies kann zu höheren Produktionsmengen und potenziell niedrigeren Produktionskosten für Komponenten in großen Stückzahlen führen.
- Größere Auswahl an Materialien: Mit herkömmlichen Methoden lässt sich häufig ein breiteres Spektrum an Materialtypen bewältigen als mit pulverbasierten Methoden, die sich für einige Legierungen noch in der Entwicklung befinden.
Die Wahl zwischen pulverbasierten und herkömmlichen Herstellungsverfahren hängt von mehreren Faktoren ab, darunter:
- Das konkrete Bauteil, das hergestellt wird: Bei komplexen Geometrien oder Komponenten, die überragende Materialeigenschaften erfordern, sind pulverbasierte Methoden möglicherweise die bevorzugte Wahl.
- Produktionsvolumen: Bei der Produktion großer Stückzahlen können herkömmliche Methoden kostengünstiger sein.
- Verfügbarkeit des Materials: Wenn eine bestimmte Legierung nicht ohne weiteres in Pulverform erhältlich ist, sind herkömmliche Methoden möglicherweise die einzige Option.
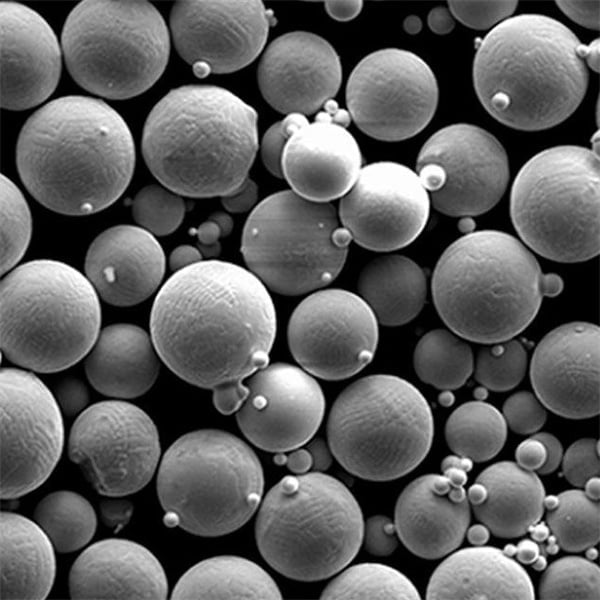
Die Zukunft von Pulvern für die Gasturbinentechnik
Die Zukunft von Pulvern für die Gasturbinentechnik ist vielversprechend. Da die additive Fertigungstechnologie immer weiter fortschreitet, wird die Nachfrage nach diesen Spezialpulvern voraussichtlich steigen. Hier sind einige spannende Trends, die Sie im Auge behalten sollten:
- Entwicklung neuer Pulverlegierungen: Forscher entwickeln ständig neue Pulverlegierungen mit noch besseren Leistungseigenschaften für noch höhere Effizienz und höhere Betriebstemperaturen in Gasturbinen.
- Verbesserte Methoden der Pulverherstellung: Fortschritte bei den Pulverproduktionstechniken führen zu kostengünstigeren und effizienteren Methoden zur Herstellung hochwertiger Pulver für die Gasturbinentechnik.
- Standardisierung der Pulverspezifikationen: Da sich die Verwendung von Pulvern für die Gasturbinentechnik immer weiter verbreitet, wird eine zunehmende Standardisierung der Pulverspezifikationen und -zertifizierungen eine gleichbleibende Qualität und Leistung sicherstellen.
FAQ
Frage | Antwort |
---|---|
Was sind die Hauptvorteile der Verwendung von Pulvern für die Gasturbinentechnik? | Pulver für die Gasturbinentechnik bieten mehrere Vorteile, darunter verbesserte Materialeigenschaften, Designflexibilität, verbesserte Materialausnutzung und Kontrolle der Mikrostruktur. |
Welche Nachteile bringt die Verwendung von Pulvern für die Gasturbinentechnik mit sich? | Zu den Nachteilen zählen die höheren Kosten im Vergleich zu herkömmlichen Materialien, die Prozesskomplexität und die Notwendigkeit strenger Qualitätskontrollmaßnahmen. |
Was sind die typischen Anwendungsgebiete von Pulvern für die Gasturbinentechnik? | Diese Pulver werden vorwiegend bei der Herstellung von Turbinenscheiben und -schaufeln, Brennkammerauskleidungen, Leitschaufeln und Hitzeschilden verwendet und kommen im additiven Fertigungsverfahren zunehmend auch in verschiedenen Anwendungen in der Luft- und Raumfahrt, Automobilindustrie und Medizin zum Einsatz. |
Welche Faktoren beeinflussen die Preisgestaltung von Pulvern für die Gasturbinentechnik? | Materialzusammensetzung, Partikelgrößenverteilung, Menge und die Einhaltung bestimmter Standards können sich auf die Preisgestaltung auswirken. |
Wie schneiden pulverbasierte Herstellungsverfahren im Vergleich zu herkömmlichen Methoden für Gasturbinenkomponenten ab? | Pulverbasierte Verfahren bieten bessere Materialeigenschaften, Designflexibilität und eine bessere Materialausnutzung, sind jedoch mit höheren Vorlaufkosten und einer höheren Prozesskomplexität verbunden. Traditionelle Verfahren sind etablierter und bieten eine größere Auswahl an Materialien, sind jedoch möglicherweise in der Designkomplexität eingeschränkt und erzeugen mehr Abfall. |
Zusammenfassend lässt sich sagen, dass technische Pulver für Gasturbinen eine transformierende Rolle in der Welt der Gasturbinen spielen. Diese mikroskopischen Wunderwerke bieten eine einzigartige Kombination von Eigenschaften, die die Grenzen von Leistung und Effizienz verschieben. Da sich die Technologie weiterentwickelt, können wir noch spannendere Entwicklungen im Bereich dieser Spezialpulver erwarten, die den Weg für eine Zukunft mit saubereren, leistungsstärkeren und effizienteren Gasturbinen ebnen.