Haben Sie schon einmal davon geträumt, komplexe Metallobjekte aus dem Nichts zu zaubern? Nun, mit dem Direkten Metall-Laser-Sintern (DMLS) Technologie wird dieser Traum Wirklichkeit. DMLS, auch bekannt als Selective Laser Melting (SLM), ist ein revolutionäres 3D-Druckverfahren, bei dem ein Hochleistungslaser Metallpulverpartikel Schicht für Schicht akribisch miteinander verschmilzt, um komplizierte und funktionale Metallteile herzustellen.
Stellen Sie sich vor, Sie bauen ein kompliziertes Getriebe oder ein leichtes Bauteil für die Luft- und Raumfahrt mit internen Kanälen, und das alles aus einer digitalen Datei - das ist die Leistung von DMLS. Aber wie genau geschieht diese Magie? Schnallen Sie sich an, denn wir werden Schritt für Schritt in die faszinierende Welt des DMLS eintauchen.
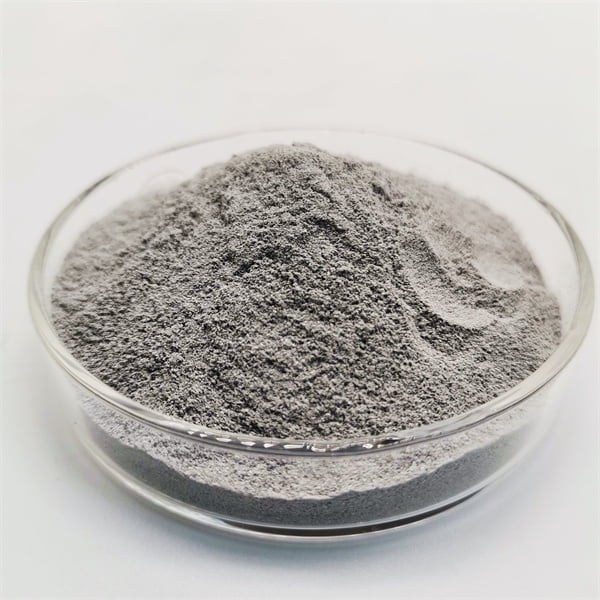
Die Bausteine: Ein Blick auf DMLS Metall-Pulver
Die Grundlage für jede DMLS-Kreation ist das Metallpulver selbst. Diese feinen Metallgranulate, die in der Regel zwischen 15 und 63 Mikrometer groß sind (das ist unglaublich winzig!), gibt es in einer Vielzahl von Geschmacksrichtungen, die jeweils einzigartige Eigenschaften für bestimmte Anwendungen bieten. Hier ein kleiner Einblick in einige der beliebtesten DMLS-Metallpulveroptionen:
Metallpulver | Zusammensetzung | Eigenschaften | Anwendungen |
---|---|---|---|
Rostfreier Stahl 316L | 16-18% Chrom, 10-14% Nickel, 2% Molybdän | Ausgezeichnete Korrosionsbeständigkeit, hohe Festigkeit, biokompatibel | Medizinische Implantate, Komponenten für die Luft- und Raumfahrt, Schmuck |
Titan 6Al-4V (Grad 23) | 90% Titan, 6% Aluminium, 4% Vanadium | Hohes Festigkeits-Gewichts-Verhältnis, gute Biokompatibilität, ausgezeichnete Korrosionsbeständigkeit | Luft- und Raumfahrtkomponenten, medizinische Implantate, Sportartikel |
Inconel 625 | Superlegierung auf Nickel-Chrom-Basis | Außergewöhnliche Hochtemperaturfestigkeit, Korrosionsbeständigkeit | Turbinenschaufeln, Wärmetauscher, Kernreaktoren |
Aluminium AlSi10Mg | Aluminiumlegierung mit 10% Silizium und 0,5% Magnesium | Leichtes Gewicht, gute Korrosionsbeständigkeit, hohe Wärmeleitfähigkeit | Automobilteile, Kühlkörper, Elektronikgehäuse |
Kupfer | 100% Kupfer | Hohe elektrische Leitfähigkeit, gute Wärmeleitfähigkeit | Wärmetauscher, elektrische Komponenten, Wellenleiter |
Werkzeugstahl (H13) | Legierter Stahl mit hohem Chromgehalt | Hohe Verschleißfestigkeit, gute thermische Stabilität | Formen, Gesenke, Schneidwerkzeuge |
Nickel | 100% Nickel | Ausgezeichnete Korrosionsbeständigkeit, gute Duktilität | Chemische Verarbeitungsanlagen, elektrische Komponenten, Wärmetauscher |
Kobalt-Chrom (CoCrMo) | Kobalt-Chrom-Legierung mit Molybdän | Hohe Festigkeit, Verschleißfestigkeit, biokompatibel | Medizinische Implantate, Zahnprothetik, Verschleißteile |
Gold | 100% Gold | Hohe Duktilität, Verformbarkeit, ausgezeichnete Korrosionsbeständigkeit | Schmuck, Elektronik, dekorative Anwendungen |
Diese Tabelle gibt einen Einblick in die vielfältige Welt der DMLS-Metallpulver. Jedes Material verfügt über einzigartige Stärken und eignet sich daher für eine Vielzahl von Anwendungen. Bei der Auswahl eines Metallpulvers spielen Faktoren wie die gewünschten mechanischen Eigenschaften, Korrosionsbeständigkeit, Gewichtsüberlegungen und Biokompatibilität (für medizinische Anwendungen) eine entscheidende Rolle.
Jenseits der Tabelle: Ein tieferes Eintauchen in die Eigenschaften von Metallpulvern
Es ist wichtig zu wissen, dass es sich bei diesen Metallpulvern nicht um irgendeinen Staub handelt. Sie wurden sorgfältig entwickelt, um eine optimale Leistung während des DMLS-Prozesses zu gewährleisten. Hier sind einige wichtige Merkmale zu beachten:
- Partikelgröße und -verteilung: Eine gleichmäßige Partikelgröße und -verteilung sind entscheidend für einen reibungslosen Pulverfluss und ein gleichmäßiges Laserschmelzen.
- Sphärizität: Sphärische Partikel bieten eine bessere Fließfähigkeit und Packungsdichte, was zu einem gleichmäßigeren Bauprozess führt.
- Fließfähigkeit: Die Fähigkeit des Pulvers, in der DMLS-Maschine frei zu fließen, ist für eine gleichmäßige Schichtbildung unerlässlich.
- Scheinbare Dichte: Dies bezieht sich auf das Verhältnis zwischen der Masse des Pulvers und seinem Gesamtvolumen. Bei einer höheren scheinbaren Dichte kann mehr Material in jede Schicht gepackt werden, was zu einem dichteren Endteil führt.
- Laser-Absorptionsvermögen: Die Fähigkeit des Metallpulvers, die Energie des Lasers effizient zu absorbieren, bestimmt den Schmelzprozess und die Gesamtqualität der Konstruktion.
Die Hersteller unternehmen große Anstrengungen, um sicherzustellen, dass ihre DMLS-Metallpulver diese strengen Anforderungen erfüllen. Durch die sorgfältige Kontrolle dieser Eigenschaften schaffen sie Pulver, die speziell für eine optimale DMLS-Leistung entwickelt wurden.
Von digitalen Träumen zur metallischen Realität: Der DMLS-Prozess Schritt für Schritt
Nachdem wir nun die Bausteine erforscht haben, wollen wir nun in die fesselnde Welt des DMLS selbst eintauchen. Hier ist eine Aufschlüsselung des Prozesses, Schritt für Schritt:
1. Wählen Sie das geeignete Metallpulver: Wie bereits erwähnt, ist die Auswahl des richtigen Metallpulvers entscheidend für das Erreichen der gewünschten Eigenschaften des Endprodukts.
2. Erstellen Sie ein 3D-Modell mit einer 3D-Modellierungssoftware: Die Magie des DMLS beginnt mit einer digitalen Darstellung des gewünschten Objekts. Mit einer 3D-Modellierungssoftware, die dem Meißel eines Bildhauers im digitalen Zeitalter ähnelt, können Ingenieure komplizierte Geometrien entwerfen, die mit herkömmlichen Fertigungsmethoden unmöglich zu realisieren wären. Diese 3D-Modelle geben jedes Detail des endgültigen Teils vor, von der Gesamtform bis zu den inneren Kanälen und komplizierten Merkmalen.
3. Bereiten Sie die Bauplattform vor: Stellen Sie sich eine digitale Leinwand vor, die zum Leben erwacht. Die Bauplattform der DMLS-Maschine bildet die Grundlage, auf der das Metallobjekt Schicht für Schicht aufgebaut wird. Diese Plattform wird sorgfältig gereinigt und nivelliert, um einen glatten und konsistenten Startpunkt für den Bauprozess zu gewährleisten.
4. Legen Sie das Metallpulver auf die Druckplattform: Eine dünne Schicht Metallpulver, die in der Regel zwischen 20 und 100 Mikrometer dick ist, wird gleichmäßig auf der Bauplattform aufgetragen. Diese Schicht dient als erster Baustein für das Objekt. Um eine gleichmäßige und konsistente Pulverschicht zu erhalten, können verschiedene Techniken eingesetzt werden, z. B. ein Rakel- oder ein Walzenbeschichtungssystem.
5. Der Laser schmilzt die Magie: Hier geschieht der eigentliche Zauber. Ein Hochleistungslaserstrahl, der anhand des digitalen 3D-Modells genauestens gesteuert wird, scannt über das Metallpulverbett und schmilzt die Partikel selektiv zusammen. Die Leistungsdichte des Lasers und der Scanpfad werden präzise gesteuert, um die gewünschte Geometrie für jede Schicht zu erzeugen. Während der Laser das Pulver schmilzt, verschmelzen die Partikel zu einer festen Masse und bauen das Objekt Schicht für Schicht auf.
6. Schicht für Schicht nimmt das Objekt Gestalt an: Das DMLS-Verfahren folgt einem sich wiederholenden Zyklus. Sobald die erste Schicht geschmolzen ist, wird eine neue Schicht aus Metallpulver aufgetragen. Der Laser scannt dann über diese neue Schicht, schmilzt das Pulver und verschmilzt es mit der zuvor aufgebrachten Schicht. Dieser Zyklus setzt sich Schicht für Schicht fort, wobei das Objekt sorgfältig von unten nach oben aufgebaut wird, bis das gesamte Design fertiggestellt ist.
7. Abkühlung: Nachdem die letzte Schicht aufgeschmolzen ist, lässt die DMLS-Maschine das gefertigte Objekt langsam in einer kontrollierten Atmosphäre abkühlen. Dieser kontrollierte Abkühlungsprozess trägt dazu bei, Eigenspannungen und Verformungen innerhalb des Teils zu minimieren und seine Maßhaltigkeit und strukturelle Integrität zu gewährleisten.
8. Entfernen der Stütze: Ähnlich wie bei Gerüsten, die im traditionellen Bauwesen verwendet werden, sind bei DMLS-Bauten oft Stützstrukturen erforderlich, um zu verhindern, dass empfindliche Merkmale während des Druckprozesses zusammenbrechen. Diese Stützstrukturen werden in der Regel aus demselben Metallpulver hergestellt, sind aber so konzipiert, dass sie nach Abschluss des Bauprozesses leicht entfernt werden können. Mit Techniken wie maschineller Bearbeitung, Wasserstrahlschneiden oder mechanischer Entfernung können diese Stützstrukturen entfernt werden, so dass das fertige Metallobjekt in seiner ganzen Pracht zum Vorschein kommt.
9. Nachbearbeitung der DMLS-Technologie: In einigen Fällen kann das im DMLS-Verfahren hergestellte Objekt zusätzliche Nachbearbeitungsschritte erfordern, um die gewünschte Oberflächenbeschaffenheit oder mechanischen Eigenschaften zu erreichen. Diese Schritte können eine Wärmebehandlung zum Spannungsabbau oder zur Verbesserung der Festigkeit, Sandstrahlen für eine glattere Oberfläche oder eine maschinelle Bearbeitung für eine höhere Maßgenauigkeit umfassen.
Die Vorteile und Grenzen von DMLS aufzeigen
Die DMLS-Technologie bietet eine Fülle von Vorteilen gegenüber herkömmlichen Herstellungsverfahren:
- Gestaltungsfreiheit: DMLS ermöglicht die Herstellung unglaublich komplexer Geometrien, einschließlich Innenkanälen, Gittern und anderen komplizierten Merkmalen, die mit herkömmlichen Techniken nicht oder nur mit hohem Kostenaufwand hergestellt werden könnten.
- Schnelles Prototyping: Die Möglichkeit, funktionale Teile direkt aus einem 3D-Modell zu erstellen, ermöglicht ein schnelles Prototyping, so dass die Ingenieure ihre Entwürfe schnell und effizient überarbeiten können.
- Gewichtsreduzierung: DMLS ermöglicht die Herstellung von Leichtbaustrukturen mit hohem Festigkeits-Gewichts-Verhältnis und ist damit ideal für Anwendungen in der Luft- und Raumfahrt sowie in der Automobilindustrie.
- Anpassungen: DMLS erleichtert die Herstellung kundenspezifischer Teile und Kleinserien und eignet sich daher perfekt für Spezialanwendungen oder einmalige Projekte.
Allerdings gibt es auch beim DMLS Grenzen zu beachten:
- Kosten: DMLS-Maschinen und Metallpulver können teuer sein, so dass sich das Verfahren weniger für große Produktionsserien eignet.
- Begrenzte Baugröße: Das Fertigungsvolumen von DMLS-Maschinen ist im Vergleich zu herkömmlichen Verfahren in der Regel begrenzt.
- Oberflächenbehandlung: Während einige DMLS-Teile eine gute Oberflächengüte erreichen können, benötigen andere möglicherweise eine zusätzliche Nachbearbeitung für eine glattere Ästhetik.
- Materielle Einschränkungen: Die Palette der für DMLS verfügbaren Materialien entwickelt sich weiter, obwohl sie ständig erweitert wird.
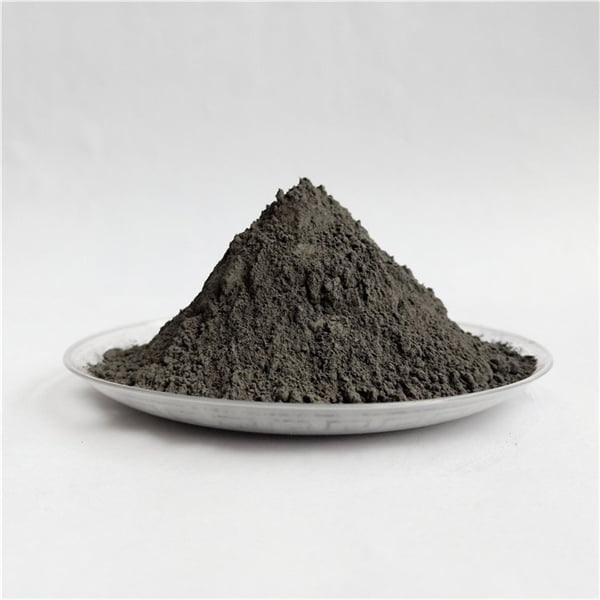
FAQ
F: Was ist der Unterschied zwischen DMLS und SLS?
A: Sowohl DMLS als auch Selektives Lasersintern (SLS) sind 3D-Druckverfahren, bei denen ein Laser eingesetzt wird, um Objekte Schicht für Schicht zu erzeugen. Ein wichtiger Unterschied liegt jedoch in den verwendeten Materialien. DMLS arbeitet mit Metallpulvern, die zu einem festen Objekt zusammengeschmolzen werden. Im Gegensatz dazu werden beim SLS typischerweise Kunststoff- oder Nylonpulver verwendet, wobei die Partikel gesintert (verschmolzen) werden, ohne sie vollständig zu schmelzen. Aus diesem Unterschied ergeben sich mehrere wesentliche Abweichungen:
- Materialeigenschaften: Im DMLS-Verfahren gedruckte Objekte sind in der Regel wesentlich stabiler und haltbarer als SLS-Teile, was auf die inhärenten Eigenschaften von Metall im Vergleich zu Kunststoff zurückzuführen ist.
- Anwendungen: DMLS eignet sich für die Herstellung funktioneller Metallteile für die Luft- und Raumfahrt, die Automobilindustrie und medizinische Anwendungen. SLS eignet sich hervorragend für das Prototyping und die Herstellung von Kunststoffteilen mit guter Ästhetik.
- Kosten: Das DMLS-Verfahren ist im Allgemeinen teurer als das SLS-Verfahren, was auf die höheren Kosten für Metallpulver und die komplexeren Maschinen zurückzuführen ist.
F: Wie stabil sind DMLS-gedruckte Teile?
A: Die Festigkeit von DMLS-gedruckten Teilen hängt von dem verwendeten Metallpulver und den Nachbearbeitungstechniken ab. DMLS-Teile können jedoch unglaublich stark sein und erreichen oft mechanische Eigenschaften, die mit denen ihrer (traditionell hergestellten) Knetteile vergleichbar sind. Faktoren wie die Wärmebehandlung können die Festigkeit des Endprodukts weiter erhöhen.
F: Welche Möglichkeiten der Oberflächenbearbeitung gibt es für DMLS-Teile?
A: DMLS-gedruckte Teile haben in der Regel eine etwas raue Oberfläche, was auf die schichtweise Art des Prozesses zurückzuführen ist. Es können jedoch mehrere Nachbearbeitungstechniken eingesetzt werden, um eine glattere Oberfläche zu erzielen:
- Bearbeitungen: Traditionelle Bearbeitungstechniken wie Fräsen und Drehen können verwendet werden, um eine glatte und präzise Oberfläche zu erzeugen.
- Sandstrahlen: Bei dieser Technik wird ein Strom von Schleifpartikeln eingesetzt, um die Oberfläche des Werkstücks zu glätten.
- Polieren: Durch mechanisches oder chemisches Polieren lässt sich eine hochreflektierende Oberfläche erzielen.
Die Wahl der Oberflächenbeschaffenheit hängt von der gewünschten Ästhetik und den funktionalen Anforderungen des Endprodukts ab.
F: Was sind die Umweltaspekte des DMLS?
A: DMLS hat, wie jedes Herstellungsverfahren, einige Auswirkungen auf die Umwelt. Hier sind einige wichtige Faktoren zu berücksichtigen:
- Energieverbrauch: DMLS-Maschinen benötigen eine erhebliche Menge an Energie, um den Hochleistungslaser zu betreiben und eine kontrollierte Atmosphäre aufrechtzuerhalten.
- Materialabfall: Abhängig von der Teilegeometrie und der Konstruktion der Stützstruktur kann während des DMLS-Prozesses etwas Metallpulver verloren gehen. Einige Maschinen bieten jedoch Möglichkeiten zum Pulverrecycling, um den Abfall zu minimieren.
- Emissionen: Beim DMLS-Verfahren können je nach dem zu bedruckenden Material geringe Mengen an Staub und Dämpfen entstehen. Geeignete Belüftungssysteme sind entscheidend für die Minderung dieser Emissionen.
Die Hersteller sind ständig bemüht, die Effizienz und Nachhaltigkeit der DMLS-Technologie zu verbessern. Die Forschung wird fortgesetzt, um energieeffizientere Maschinen zu entwickeln und die Abfallerzeugung zu minimieren.
Die Zukunft des DMLS: Ein Blick auf die Innovationen von morgen
Die DMLS-Technologie ist ein sich schnell entwickelnder Bereich, der ständig die Grenzen des Machbaren verschiebt. Hier sind einige spannende Trends, die die Zukunft des DMLS bestimmen:
- Multi-Material-DMLS: Die Möglichkeit, Objekte mit mehreren Metallpulvern in einem Arbeitsgang zu drucken, eröffnet die Möglichkeit, Teile mit einzigartigen Eigenschaftskombinationen zu erstellen.
- Größere Bauvolumen: DMLS-Maschinen mit größerem Bauraum sind in der Entwicklung und ermöglichen die Herstellung noch größerer und komplexerer Metallobjekte.
- Schnellere Druckgeschwindigkeiten: Fortschritte in der Lasertechnologie und bei den Mechanismen zur Handhabung des Pulvers führen zu kürzeren Druckzeiten und machen DMLS für Produktionsanwendungen effizienter.
- Neue Materialien: Die Palette der mit DMLS kompatiblen Werkstoffe wird ständig erweitert und umfasst neue Legierungen und sogar exotische Materialien wie Titanaluminid (TiAl).
Die DMLS-Technologie entwickelt sich weiter und hat das Potenzial, verschiedene Branchen zu revolutionieren, von der Luft- und Raumfahrt über die Automobilindustrie bis hin zur Medizin und darüber hinaus. Mit seiner Fähigkeit, komplexe, funktionale und leichte Metallteile herzustellen, ist DMLS in der Lage, eine bedeutende Rolle bei der Gestaltung der Zukunft der Fertigung zu spielen.